One of the biggest trends in robotic systems developed for use within warehousing pick, pack and kitting operations has been collaboration. This refers to robotic mechanisms that work side by side with humans and interact as needed within a workcell, but with no physical safety barrier between the two.
ABB Robotics’ latest offering in that space is the small-parts-handling YuMi, says Rick Tallian, manager of picking, packing and palletizing products and applications.” Users with space constraints in their palletizing zones are eager to see the same type of barrier-free interaction on robotic palletizers that are much larger,” he says, adding that ABB is developing such a solution now.
However, some suppliers may be over-promising on current collaborative robotic palletizer capabilities, he cautions. Before a facility considers purchasing such equipment, a few key points are important to keep in mind.
First, standards for the safe design and operation of collaborative robotic technologies (including palletizers) are still under development by the Robot Industries Association (RIA) and the International Organization for Standardization (ISO). There are, however, “very specific guidelines (ISO 10218) established to determine safe operation conditions for robotic devices and the cell around the robot,” Tallian notes.
Second, “both organizations recommend that a trained professional perform a risk evaluation of your operation prior to installing equipment,” he explains. “Make sure you understand the amount of force a robot may impart if it contacts a person, and that speed and torque limiting features should be integral to the robot’s design to prevent injury.”
Third, the robotic palletizer’s task parameters may preclude a collaborative model simply by nature of the packages being handled, Tallian notes: “Most of the robotic operations performed in manufacturing and warehousing are designed to maximize the speed and throughput. But a typical palletizing operation—handling heavy boxes and moving massive robot arms at high speeds—does not qualify for current collaborative robotic mechanisms on the market today.”
For now, he adds, space-limited operations wishing to remove a physical safety barrier around a palletizer do have other options. “There are safety technologies—including light barriers and photo eyes—that detect the presence and proximity of a person and trigger the robot to slow down or stop at certain points for safety.”
About the Author

Follow Robotics 24/7 on Linkedin
About the Author

Follow Robotics 24/7 on Linkedin
Article topics
Email Sign Up
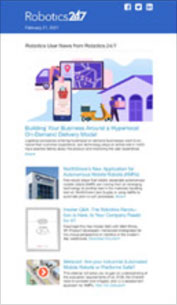