Editor’s note: The following column by Matt Meersman, vice president of sales for JLT Mobile Computers, is part of Modern’s Other Voices column, a series featuring ideas, opinions and insights from end-users, analysts, systems integrators and OEMs. Click here to learn about submitting a column for consideration.
————-
The first wave of industrial automation saw the wide-spread use of computers and robotic systems to improve productivity. Now we’ve entered an era, termed Industry 4.0, where intelligent networked systems go beyond mere machine control via feedback systems, interdisciplinary cooperation, IoT technology, and advanced resource/demand management to morph into “smart” factories and warehouse operations.
Industry 4.0 employs evolved computer hardware, extensive sensor technology, local and cloud-based software analytics platforms, and vastly expanded networking to provide access to value-added real-time data at all levels of the enterprise. This enables instant action and reaction, time-critical optimization and fine-tuning of processes and procedures, as well as instant mining of historical data to see trends, patterns, risks, and opportunities. All this works towards the promise of Industry 4.0 – that of optimizing operations and maximizing productivity at every level.
All systems however, even those as elaborate and sophisticated as a well-oiled Industry 4.0 installation, are only as strong as their weakest link. Hardware, software, sensors, cloud connectivity, human interface systems and a myriad of other things can all be that weakest link, keeping both IT and the workforce on their toes. In warehouse operations, more often than not, that weak link is network connectivity. Why is that, and how can it be fixed?
The problem is that, unlike corporate offices or many other operations, warehouses are not static. Only one part of a warehouse, the structure, is fixed. Everything else is in a constant state of flux. Goods are moved around and stored in various locations. Nothing stays in the same place for long. Personnel is mobile as well, stocking goods, picking orders, and moving them on foot or with forklifts and other vehicles. Trucks come and go. There are loading docks, cranes, packing areas. Everything changes all the time, and such a dynamic environment has a huge impact on connectivity.
Rock-solid connectivity is the lifeblood of every warehouse enterprise. And yet, reliable connectivity remains a vexing, frustrating issue in all too many operations. That’s because while part of a warehouse communication system can be wired, the mobile part cannot. Workers with handhelds, forklift operators with vehicle-mounts, trucks with onboard computers, and anything else that moves requires wireless communication. That means safe, secure, reliable, hardened WiFi. Easy, one might think. WiFi is a mature technology.
But in a warehouse WiFi is not that easy. It starts with the number of access points required. One is needed for approximately every 800 square feet. That’s 20 for the average warehouse in the US (16,400 square feet, per government data), and it can easily be many hundred access points for larger warehouse operations. IT has decades of experience in setting up even very large wireless systems in office buildings or on shop floors, but warehouses are different in several critical ways.
Steady, reliable coverage depends on signal strength and the elimination of weak and dead spots. That’s fairly easy to handle in static settings where things don’t move around. But in warehouses they do. The variety and volume of goods, ever shifting storage locations, and different packing materials that may either reflect or absorb signals (such as cardboard, liquids, and food items) all affect the network. Signal strength varies, and dead spots may materialize anywhere. Add to that the almost certain presence of multiple networks (warehouse, shipping, manufacturing, transportation, guests, etc.) and roaming becomes an issue, as do disconnections, access security identifications, and all sorts of frustrating, productivity-killing slow-downs and restarts.
The inherent mobility in the warehouse makes it that much worse. Everyone and everything is constantly on the move. Solid wireless connectivity does not just rely on the type, reliability, placement, and effective management of access points, but also on the type, location, and performance of mobile devices that send and receive data. If any part breaks down, there goes the promise and benefit of Industry 4.0. Warehouse managers can’t meet their target. Workers are frustrated. Customers get disgruntled, productivity tanks, and so does profitability of the entire warehouse operation. What can be done to avoid those challenges?
One solution is to address problems on the mobile device level. Many systems are designed for standard office Wi-Fi operation, but aren’t up to much more demanding warehouse deployment. They may have single antennas with poor roaming performance. The location of antennas may be such to preclude optimal performance. Wireless modules themselves may be marginal both in terms of performance and ruggedness, and not suited for the demands of warehouse operation. Signal strength may be insufficient. Apart from that, devices may simply be ill-suited for warehouse deployments. Operation may be confusing and inconsistent between devices. Handhelds or tablets may not be locked down with custom images that preclude distractions and accidental or deliberate switching to other networks. All that must be addressed.
Overall, warehouse-specific connectivity issues must be dealt with at a holistic level. That means assessing the whole operation not only in terms of physical layout, but also by kind, size and location of goods, anticipated movement of goods, types of mobile devices deployed, time-to-load considerations, integration of historical trending data, and various other related variables.
An increasing number of warehouse operations are going this route, often assisting in-house IT by outsourcing network design and management to vendors that offer “Wi-Fi as a Service” (WaaS). WaaS is offered by industry-specializing suppliers as a turnkey, enterprise-level LAN solution based on a detailed expert analysis of a warehouse operation. The WaaS vendor then designs, deploys, and optimizes a proactively managed Wi-Fi network that takes into consideration every detail of a specific warehouse setup. Usually that includes a 24/7 network operation center that continuously monitors network performance, health and overall optimization, often in conjunction with HaaS – Hardware as a Service, thus providing and maintaining task optimization on the mobile and vehicle-mount hardware side as well.
What it all amounts to is nothing less than harnessing the potential of Industry 4.0 for the warehouse. Few things are one-size-fits-all, and least of all industrial settings and operations. In the warehouse, the key to success is network customization, making it fit, focusing on what matters, and making sure those crucial areas work just right.
Article topics
Email Sign Up
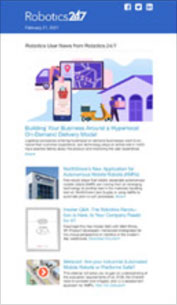