Editor’s note: The following column by James Beale, operations manager at Invicta Pallet Racking, is part of Modern’s Other Voices column, a series featuring ideas, opinions and insights from end-users, analysts, systems integrators and OEMs. Click here to learn about submitting a column for consideration.
————-
Most businesses are always looking to be more efficient, but never more so than in the present day. A variety of difficult business conditions mean that warehouse and logistics operations are increasingly looking to save money and space. Oftentimes, the best way to do this is to invest in technological solutions - upgrading the infrastructure that your business relies on every day.
Some of the improvements that can be made to warehouse and logistics infrastructure are more familiar, while others are more on the cutting edge. From smarter shelving to roving robots to simply investing in your staff, here are five innovative ideas to make your warehouse space more efficient.
Telescopic handlers
While the traditional forklift has gone through a number of design tweaks over the years, the basic design is very familiar. The telescopic handler represents something of a design revolution. The use of a telescopic forward reach boom provides more flexibility than a traditional forklift, and could improve your operational efficiency as a result.
Telescopic forklifts can allow you to take advantage of and optimize outdoor and indoor storage space by allowing vehicles to load goods directly from one side of a curtainside trailer, shelving or stack. Not only does this require less space for loading and unloading, it also gives you more flexibility in how you store your products, as the arm can reach pallets or items at different depths and heights. These vehicles can also be electric, potentially saving money on fuel and improving the air quality - and therefore quality of life for employees - in and around your facility.
Smarter storage
While there are plenty of cutting-edge technologies you can apply to your warehouse, an equally effective solution is simply to reappraise your storage. A higher density form of pallet racking could easily increase your available storage space by more than half - or double the amount of floor space you have available for other tasks - giving you ample room to grow.
From a simple narrow-aisle pallet racking solution to the flashier pallet shuttle racking, a new racking layout won’t just provide you with more storage space - it also affords you the opportunity to reconsider how you store goods. You may decide that you want to use different varieties of system for different products or areas of the warehouse, such as double-deep racking for long-term storage and live pallet racking for more transient goods.
You can also go a lot smarter, and integrate elements of automation with your racking. Perhaps the most popular emerging system is an automated storage and retrieval system (AS/RS). Suitable for small items which can be easily picked by a robotic arm or similar device, an AS/RS system can fetch items from a large, deep racking system and deliver it to a human operative - massively increasing the speed and efficiency of retrieval.
Android phones
If you run a logistics operation, it’s likely that your workers use some kind of mobile or handheld system, either for inventory management or manual data entry. According to surveys by Renovotec, around 70% of the industry currently relies on Windows-based mobile operating systems for their devices - despite the fact that support for these systems is due to end in January 2020.
With many of these devices now outdated and open to security risks, now may be the time to switch to an Android based system, such as those offered by Honeywell. These devices can be just as durable, and will benefit from an increase in speed and functionality. The Android operating system will also be more familiar to younger employees - and with the help of an IT firms, it shouldn’t require substantive changes to your warehouse management system.
Employee training
Many warehouse and logistics businesses offer some sort of training to employees to help them carry out their roles, often in the realm of health and safety. However, by going above and beyond to offer additional skills training, you can both improve the quality of people’s work and reinforce the ties that bind them to your business. Offering and incentivizing training courses can be a great way to sharpen skills, improve practices within your warehouse or logistics operation, and even to fill roles that you may be struggling with or anticipating a need for.
One example is a scheme called Warehouse to Wheels, offered by parcels carrier Tuffnells. By offering free 12 month driver training to warehouse employees, individuals receive valuable training and a pathway to further career progression. This not only stands to attract people to work at the warehouse in the first place, but also helps to fill roles with employees who have a specific and high-standard level of training. Just as importantly, they are likely to value the time you’ve invested in them, increasing retention and making them want to work even harder.
Automation
Warehouse automation isn’t just the future - for many businesses, it’s the present. While Amazon has been the front-runner in this field, they have kept most of their advances to themselves. Thankfully, numerous companies have stepped into the breach to develop similar autonomous robots and other automated systems, which shepherd pallets and individual items around the warehouse.
The advantages of automation are numerous. Autonomous vehicles and robots can be more reactive, as they receive an order from a WMS and immediately know where to go to carry it out. They also present safety benefits, as they can support heavy loads and pose no risk of injury to human operators, with sensors to prevent them from colliding with people. Their suitability for menial, repetitive work also reduces the physical and mental load on human operators, who can be moved to other tasks.
Robots can now be bought, leased as part of a Robotics as a service (RaaS) deal, or leased on a pay per pick (PPP) deal, meaning that these platforms can be affordable to most businesses, and easily scaled as you grow. Robotics also extends past autonomous vehicles that navigate your warehouse floor, and to slightly more static systems, including AS/RS and automatic picking systems. Instead of conducting several stages of a task - e.g. picking and delivering - these systems tend to perform a single task more quickly, allowing you to pick and choose where you implement autonomous systems.
Article topics
Email Sign Up
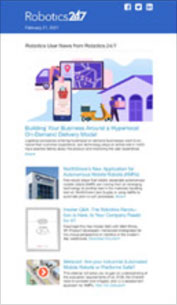