Nimble Robotics Inc. this week said that its robots have picked and packed hundreds of thousands of customer orders on a daily basis. The San Francisco-based startup claimed that its robots use artificial intelligence to “pick, pack, and fulfill online orders to enable the fastest, most affordable, and most sustainable on-demand e-commerce fulfillment.”
“E-commerce continues to grow rapidly, but the available warehouse labor force is actually declining,” said Simon Kalouche, founder and CEO of Nimble Robotics. “These opposing trends are creating historic labor shortages and a growing labor supply void. Our robots are being used to augment the human workforce to help fill that void.”
Over the past few years, said Nimble, two challenges have stifled the adoption of pick-and-pack robots: reliability and technology integration challenges. E-commerce fulfillment centers hold millions of different products, said the company. Each of those products are different sizes, shapes, weights, textures, stiffnesses, and fragility. Having robots that can reliably handle all of this variability has been considered by many to be impossible, said Nimble.
In addition, integration of technology into warehouse ecosystems is a notoriously painful process, Nimble said. Integration efforts frequently take up to a year, cost hundreds of thousands of dollars, and require thousands of software changes to the warehouse management system (WMS). Nimble said its offering uniquely solves these two challenges.
Nimble touts flexibility, ease of integration
Nimble said it has deployed fleets of robots within warehouse environments across the U.S. this year. It added that it expects existing and new contracts to grow the fleet with over 200 more robots in 2022.
The company said its robots have picked more than 15 million objects across 500,000 unique products, ranging from cosmetics and consumer electronics to apparel, from daily essentials to holiday gift favorites.
“Our robots use a variety of different grippers and supervised autonomy to reliably handle nearly any object or product that fits into a bin,” said Kalouche. “Our AI learns what grippers work best on different objects and automatically switches its gripper to properly pick, pack, and handle each object.”
“Our technology has been proven to be reliable to 99.9% accuracy in production, but what’s often the most impressive and exciting product feature, in the eyes of our customers, is the way in which we seamlessly integrate our robots,” he added. “It’s very fast and easy. Our AI-based integration requires no changes to the warehouse software whatsoever. It also costs nothing to implement. The AI interprets the already existing human operator interfaces to determine what items to pick and where to pack them.”
“A full production integration can all be done in one day using Nimble’s AI Integration tool,” said Kalouche. “When I say, ‘One day, $0, zero code changes,’ it sounds too good to be true, but our customers will vouch for us. This has been a significant competitive advantage allowing us to quickly scale.”
“To my knowledge, we’ve now deployed the world’s largest fleet of e-commerce ASRS [automated storage and retrieval system] picking robots,” he stated. “More robots deployed means more proprietary data being collected. Just like with self-driving cars, more data means higher capability and reliability which further drives customer retention and happiness.”
Big brands turn to picking robots
Nimble said it is working with many of the world's largest and best-known brands including Best Buy, Victoria’s Secret, Puma, NFI/CalCartage, and Weee! It added that its robots are picking in warehouse applications developed by systems integrators such as AutoStore, OPEX, Bastian, Swisslog, TGW, and Kuecker Pulse Integration (KPI).
“We haven’t done any marketing and surprisingly we don’t have any dedicated sales reps, yet we’ve deployed a large number of robots,” said Kalouche. “I think this is a testament to the high demand for what we’re building and to our product and how well it works. We let the robots speak for, and sell, themselves. To date, we have 100% customer retention and 100% repeat customers.”
“With logistics and fulfillment experience at Amazon, iHerb and other retail companies, I've worked with a lot of technology teams, and the Nimble team is the most impressive robotics team I've ever worked with,” said Jonathan Styles, director of continuous improvement-lean at iHerb. “They are bringing to market bleeding-edge technology and solving extremely hard problems in a market that is struggling to find labor. We have over 20 Nimble robots today and plan to add more as we grow our fulfillment capabilities.”
“There are a dozen or so robotics companies that claim to have a robotic picking solution,” said Helmut Leibbrandt, senior vice president, supply chain management and logistics – Americas, at Puma. “Nimble is the only one I’ve seen that has proven, scaled deployments in real warehouses performing real production picking. They developed a solution that integrated seamlessly within our existing physical and WMS/WCS [warehouse control system] structure.”
“Nimble partnered with us last year during the COVID outbreak to help us safely fulfill orders in our warehouse,” said Gary Bravard, co-founder and chief business officer of Adore Me. “Together, we became the first e-commerce fulfillment center in the world with fully robotic picking. The robots now handle our 25,000+ SKUs and can pick over 30,000 units per day.”
Nimble invests in growth
Nimble Robotics said its backers include Accel, DNS Capital, GSR Ventures, and Reinvent Capital. It noted that its board members include AI experts and entrepreneurs Fei-Fei Li and Sebastian Thrun.
Since raising a $50 million investment in March, Nimble has increased its team from 25 to 75 employees and expanded its customer base. The company added that its robots are already helping to fulfill millions of orders for the 2021 holiday season.
Article topics
Email Sign Up
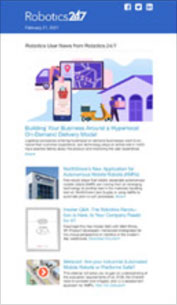