When it comes to fine jewelry, terms like cut, color and clarity come to mind, but what about speed and efficiency?
Louisiana-based Stuller, Inc. creates fine jewelry for more than 40,000 jewelry professionals worldwide, including some of the largest retailers in the United States.
Rapid, high-quality production is critical in this highly competitive industry with its significant brick and mortar and fast- growing online fulfillment demands.
Enter mobile robots from Adept Technology.
Named “Fred” and “Stella” by Stuller employees, both robots are Adept Lynx® autonomous intelligent vehicles (AIVs) outfitted with custom shelves for moving small parts. Lynx vehicles are designed to transport goods throughout large operations without requiring building modifications–ideal for Stuller’s 600,000-square-foot facility. Lynx robots intelligently self-navigate, avoiding obstacles and choosing the shortest path to complete their task. Equipped with LIDAR and sonar for safety, Lynx AIVs work cooperatively with people.
Fred works in Stuller’s wax mold department, continually running a 12-minute route to move finished jewelry molds from technicians’ workstations to an expediter for casting. The robot autonomously navigates between 40 stations, stopping to greet the technician by saying their name while picking up finished materials. At first workers moved out of the aisle way for the moving robot, but soon learned that Fred safely navigates around them and any other obstacles.
During the day shift, the job was originally done by three employees, who have since been re-deployed to other positions in the facility. “We don’t know what we’d do without the robot,” said Angel Savoie, manager in the Stuller wax department. “Fred eliminated wasted time we had in our transportation process and has helped us utilize labor in other areas where we were lacking.”
Manufacturing Mobile Robots 101
Adept’s Lynx family of mobile robots is providing rapid, reliable goods transport in manufacturing and warehousing facilities around the world. They are quick-to-deploy, naturally avoid obstacles, and work safely alongside humans.
This webinar will teach you how Lynx autonomous intelligent vehicles (AIVs) are changing the way material and work in progress (WIP) is moved throughout the manufacturing floor. You will learn how AIVs function in a manufacturing setting, queuing tasks from the Manufacturing Execution System (MES) to efficiently and effectively pickup and deliver material and WIP. We’ll examine several use cases on the manufacturing floor and learn about the qualities of these unique mobile robots that allow them to work collaboratively and safely around their human counterparts.
View the Manufacturing Mobile Robots 101 Webinar
Stuller was so satisfied with Fred the company purchased a second robot they named Stella. Stella works in stone setting, moving work-in-progress (WIP) throughout the department, allowing two runners to move to other jobs. In personnel time alone, the Lynx robot’s ROI was just one year.
According to Shane Guidry, director of stone setting, the robots also encouraged a larger change in the company. To plan for Stella, the Stuller team re-examined its WIP process and adopted a more continuous workflow, eliminating wasted down time. In the weeks leading up to robot deployment, the team ran a pilot program, using a human runner working on Stella’s anticipated route to fine-tune their process.
Once they deployed the robot, their results were tremendous; the team was able to fill orders days faster. With Stella in place during the Christmas rush, the company accomplished 22 percent more production time, while incurring 21 percent less overtime than the prior year.
The Lynx mobile robots work alongside their human co-workers five to six days per week, two shifts each day, stopping only briefly to recharge during the night. They’ve both been given company badges, and true to his namesake, at the end of each day shift Fred says goodbye to team members with a “Yabba dabba doo!”
Article topics
Email Sign Up
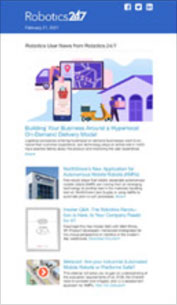
