Mobile Industrial Robots ApS today announced two new autonomous mobile robots for transporting pallets and other heavy items around factories, warehouses, and logistics centers. The Odense, Denmark-based company said the MiR600 and MiR1350 robots can lift up to 600 kg (1,322 lb.) and 1,350 kg (2,976 lb.), respectively. They are designed to to safely and efficiently perform material handling tasks in challenging industrial environments, it added.
“Customers testing AMRs within their facilities have learned that they want to transport heavier loads and that successfully investing in large fleets for core production demands ever greater levels of reliability, safety, and quality,” stated Søren E. Nielsen, president of Mobile Industrial Robots. ”Our new industrial and robust robots meet these requirements, making them an easy choice to integrate directly into companies’ workflows.”
Mobile Industrial Robots (MiR) makes collaborative autonomous mobile robots (AMRs) that enable companies to manage internal logistics and free employees for higher-value activities. Hundreds of midsized through large multinational manufacturers and logistics providers, along with several hospitals around the world, have installed MiR’s robots. The company said it has a distribution network in more than 60 countries.
In 2018, Teradyne Inc., a leading supplier of automated test equipment, acquired MiR. Teradyne also owns collaborative robot arm leader Universal Robots and autonomous tugger and lift company AutoGuide Mobile Robots.
MiR designs robots to withstand dust and water
The MiR600 and MiR1350 are the market’s first Ingress Protection 52-rated AMRs, according to MiR. Their electrical components are protected and can tolerate dust and water drops, which is important in the food-handling industry.
“We're seeing a lot of food and beverage interest,” said Matt Charles, sales director for the Midwest U.S. and Canada at MiR. “This will also help out customers with similar needs. IP52 will help us out with the majority of applications.”
“We've been working on these robots for a couple of years—ever since launching the MiR1000 in 2019,” he told Robotics 24/7. “The No. 1 request was for bigger robots. We've been evaluating form factor and size in Denmark, and significant testing went on. We reinforced the chassis of the system, strengthened the casters, and used drive wheels similar to the MiR1000.”
“With AMRs increasingly integrated into core productions, downtime is not an option,” Nielsen said. “Our new AMRs are industry-grade and constructed for a long lifetime with easy serviceability, thanks to components and cables that are industrial and easy to access.”
Sensors and safety
Like MiR’s smaller AMRs— the MiR100, MiR200, MiR250, MiR500, and MiR1000—the two new models can navigate smoothly and safely among people and other transport equipment in dynamic surroundings, said the company. Sensors, 3D cameras, and the latest laser scanning technology ensure 360-degree vision for precise navigation and operations.
“We learned from the MiR250 that cross-eyed cameras in addition to 3D sensors can see more above and below than safety-rated lidar,” Charles said. “The 3D cameras were there for object detection, but the new cameras can see overhanging objects or obstacles on the ground ahead of time.”
The new AMRs are designed to comply with the industry’s latest safety standards, including ISO 3691-4 and ANSI/RIA R15.08-1-2020.
“Many companies now integrate our mobile robots as an alternative to manned forklifts, which can be expensive to staff and dangerous to operate,” Neilsen said. “The streamlined transport provided by AMRs frees employees to carry out more value-creating activities and support processes in production while they increase shop-floor safety.”
The MiR1350 has the same speed as the MiR1000 at 1.2 m/sec. (2.6 mph), said Charles. The new robots also use a dense 48v battery pack that can charge in one hour and provide eight to 10 hours of runtime.
New AMRs automate inbound, outbound logistics
Mobile Industrial Robots said its MiR600 and MiR1350 are ideal for autonomously transporting heavy loads of materials and goods in the following locations:
- Loading bays
- Production and assembly areas
- Warehouses
- Material delivery areas
“Before the MiR1350, we couldn't quite handle the maximum capacity of GMA [Grocery Manufacturers Association] 40x48 [in.] pallets of 2,800 lb.,” said Charles. “This will be huge for us in the pallet-transfer and materials handling spaces.”
For inbound and outbound logistics, MiR's new AMRs can work with AutoGuide's autonomous lift trucks. “For us, it's taking products from loading docks to long-term storage or the production line or, flipping things around, taking finished products from the line to fork trucks, which take them from there and load them on trucks,” Charles said.
Demand for scalability and adaptability
Where is demand for higher-capacity AMRs coming from?
“Certainly, automotive manufacturing is driving a lot of it, with deliveries to the production line and taking products from the line,” Charles replied. “The biggest one we're seeing is FMCG—fast-moving consumer goods, which are growing exponentially this past year, with COVID-19 and everyone shipping products. Everyone is trying to optimize internal logistics, from candy to pharmaceuticals. They're also trying to limit fork truck traffic.”
“Logistics and e-commerce is the third space we're seeing demand higher-payload robots,” he added. “There is demand for AMRs in grocery, but those are mainly smaller loads that are prepicked, sorted, and taken to areas to transfer to customers. Cold storage has come up quite a bit.”
Although there is some interest in mobile manipulation, it has been more for UR cobot arms on the MiR250, and issues with power and control still need to be worked out, said Charles. “We're seeing more use cases for tasks such as visual inspection for quality control than machine tending or pick-and-place tasks, which don't always make sense for ROI [return on investment],” he said.
On the software side, Version 2 of MiR's fleet management software is available, and the company and some of its customers are watching various interoperability efforts.
“Our system is fairly open,” said Charles. “With REST APIs [application programming interfaces], you can get fleet and position information from the robots, whch is what you need for systems from different vendors to work together. A lot of software providers are looking at providing another layer.”
Top modules from partners such as ROEQ for the MiR600 and 1350 offer flexibility “out of the box” without requiring extensive customization for different tasks or workflows, said MiR. These top modules enable the AMRs to pick up and drop off pallets and carts for easy integration and scalability throughout the entire value chain, it claimed.
“Dimensionally, the new robots are close to the MiR500 and MiR1000, so they will work with existing pallet racks and top modules such as a conveyor deck,” said Charles. “It's the same mechanical and electrical interface; we're just adding some capacity.”
About the Author
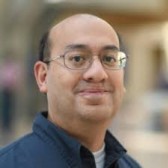
Follow Robotics 24/7 on Linkedin
Article topics
Email Sign Up
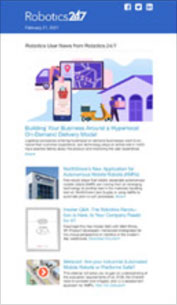
