The future of automation solutions for warehouses, fulfillment centers and factories is looking more and more mobile. Instead of relying on fixed automation systems, the high-growth niche these days is mobile automation, most notably autonomous mobile robots (AMRs).
Market research firm Interact Analysis predicts more than 4 million AMRs will be deployed globally by the end of 2027, with the segment growing between 30% and 40% through the forecast period. Besides AMRs, growth is also expected for automatic guided vehicles (AGVs) and autonomous lift trucks.
In short, much of the automation going into fulfillment centers and plants will be mobile. That fact begs the question: Are the wireless networks and charging infrastructure deployed today ready for this future?
Providers of cellular network technology and wireless charging solutions say operations need to assess whether they have the right communications and charging infrastructure in place to support all the robots that are going to be zipping around a site.
AMR providers say they typically can get good connectivity with most WiFi networks, though some may need to be tweaked to achieve adequate signal. As for chargers, while robotics vendors typically provide chargers, now vendors are specializing in wireless chargers that promise advantages over contact-based units.
For end-user organizations, it may come down to how heavy your use of mobile automation already is or will soon become.
“I think the less mobile you are, the less immediate need you’re going to have for something like [private] 5G networks, while the more mobile your systems are, I think you stand to benefit greatly from advancements in 5G and wireless communications in general,” says Josh Schwartz-Dodek, chief technology officer at Sojo Industries, a company that offers variety packing services and modular robotic technology solutions for variety packing operations. “If you can rely on wired Ethernet or fieldbus for your automation and don’t have a lot of assets that move around, you’re probably in pretty good shape, but as more of your assets become mobile, you may need to invest in new advances.”
Wireless network evolution
The thing to understand about WiFi networks is that they tend to be a work in progress, with most user companies steadily progressing to newer generations of WiFi at their own pace, explains Christian Siefen, senior engineer for ResGreen, an AMR and AGV provider.
Most companies have progressed to newer generations of WiFi that support dual-band technology, though fewer are on the latest generation WiFi 6, says Siefen. To date, none of ResGreen’s customers have deployed the latest private cellular networks.
Additionally, for simple Internet of Things devices that support fleets, like stop-light devices, sometimes the best wireless protocol to employ is long-range LoRa technology, even if the fleet taps the WiFi for communications.
ResGreen will study the WiFi network at a site to spot any weak areas, says Siefen, but typically most newer WiFi networks will work fine, with the main tweak being to decide the WiFi band to use for the fleet.
Overall, he adds, most operations are cautious about over-hauling their wireless networks unless they see performance issues, though he expects some operations will eventually deploy private cellular networks.
“It’s going to take time for private 5G to become commonplace,” Siefen says. “In general, most companies want to watch a couple of big companies they know do it first, watch how that goes, and if it really makes a difference, they might jump on board.”
The new evolution with wireless networks is the ability to set up private 5G networks, which are designed for low-latency connectivity to mobile assets or devices. The more mobile assets you have, the trickier it is with WiFi to have a seamless handover of connectivity between access points.
Private cellular, meanwhile, requires fewer access points with the whole infrastructure designed to maintain deterministic connectivity as assets roam, says David Callisch, head of marcom for Celona, a provider of enterprise private wireless solutions.
WiFi and private 5G networks have some similarities, adds Callisch, in that they both use wireless access points. But with private 5G networks, the assets being connected get outfitted with a SIM card or eSIM, which helps ensure robust security, and importantly, high reliability with no loss of signal as assets roam.
Private cellular networks need cellular access points, adds Callisch, but the long-range performance of cellular means that typically, indoors, a site would need five or more WiFi access points to equal the same coverage that a single cellular access point provides, while outdoors, it’s a 10:1 ratio.
“WiFi is a best effort technology that is prone to problems that private cellular networks don’t have, such as media contention and erratic signal attenuation,” Callisch says. “With a private 5G network, you see much better wireless coverage, better control over the network, more reliable connectivity, and you typically get it at a cost that rivals conventional WiFi, because you’re not deploying as many access points.”
Private 5G gets real
It took until 2020 for this band to be ready for commercial use in the U.S. market, and in just three years, various organizations have tested or deployed private networks using 4G/long-term evolution (LTE) or 5G cellular technology. Dozens of vendors are involved in providing solutions, including some turnkey providers like Celona and others who provide all the access points, SIM cards, management software and other needed technology.
An industry group—the OnGo Alliance—is even focused on certifying equipment and evangelizing the benefits of private cellular networks. According to the alliance, more than 350,000 CBRS access points are now in use.
Industrial facilities with mission-critical mobile automation are prime candidates for benefitting from private cellular networks, says Callisch. The secret sauce with private 5G, he says, is low latency and high reliability as mobile assets or devices travel through a facility.
“With cellular, you have a SIM card, which provides better control over what devices connect and how you connect,” says Callisch. “These advantages are growing more important, because in industrial environments, there is more use of smart mobile equipment to make operations more efficient. You don’t necessarily want these mobile assets being prone to issues because they’re having to constantly struggle to connect and reconnect to different access points as they move through a facility or yard.”
Del Conca, a global tile manufacturer based in Italy, has deployed a private cellular network using Celona’s solution set at a plant in Loudon, Tenn., that manufactures and ships tile products. The network supports communications for the plant’s AGV fleet from SACMI, which are used to automate the transportation of sections of tile through various production steps in the plant, covering close to 30 acres indoors and outdoors.
A small gateway router module with a SIM card plugs into each AGV to access the network, which is running reliably and avoiding issues the site previously had in trying to run its AGVs reliably with WiFi connectivity.
For the deployment at Del Conca’s site in Tenn., Celona performed a study and recommended using eight indoor Celona AP 12 LTE units and four Celona AP 11 LTE outdoor units. The connectivity is working well for the AGVs and also lift trucks that access the network from forklift mounted computers. According to Luca Chichiarelli, head of IT operations for Del Conca USA, the new network has proven reliable, avoiding past connectivity issues at the site.
“Celona’s unique approach to private wireless allowed us to quickly overcome many of the wireless issues we’ve been facing for a while now,” says Chichiarelli. “With it we’ve been able to reduce latency, improve mobility, expand coverage and, most importantly, increase the reliability of the wireless services that have become the foundation for automating our manufacturing operations.”
There are other examples of 5G networks being used to support mobile automation. According to AMR provider ForwardX Robotics, its customer TCL, a major electronic company in China, has deployed what is thought to be first 5G AMR deployment at its plant in Huizhou, China, as part of a 5G digital transformation initiative.
The Huizhou factory and warehouse uses ForwardX AMRs for autonomous pickup and drop off of raw materials between lineside storage areas and points across its production line. By integrating 5G communication modules from Qualcomm into its AMRs, the AMRs have a fast, reliable connection to the fleet software, with a latency threshold of no more than 60 milliseconds.
Charging forward
AMRs, AGVs and other mobile automation run on batteries, and that means charging infrastructure. While automation vendors can set up a fleet with contact-based charger stations to support autonomous self-docking, the trend over time will likely be less use of hot-shoe chargers and more use of wireless charging.
Wireless inductive charging offers multiple advantages, says Matthieu Ebert, director of product and technology for PULS Wireless, formerly Wiferion. Wireless charging requires less maintenance because charger contacts don’t exist, so no elements can get fouled or jammed. “Our wireless charging is basically maintenance free and doesn’t require precise docking,” Ebert says. “It just makes the whole approach to the opportunity charging process more robust.”
Wireless charger stations can also service different AMRs with the same charger, which could lower infrastructure costs as companies begin to deploy multiple AMR fleets, Ebert says. Longer term, he adds, wireless charging vendors could offer energy management software with dashboards to visualize trends and provide data insights on optimal times to charge AMRs, to help achieve aims like upping the priority of opportunity charging to coincide with times of high availability for renewable energy resources.
This sort of charging optimization will take time to develop, Ebert says, since currently little “harmonization” of job priorities exists among different robot fleets, but the first step is to have cloud connected chargers and analytics over data from the chargers.
Multiple vendors offer contactless wireless charging solutions. For example, ResGreen partners with WiBotic to provide wireless chargers for its LilBuddy AMRs. According to Siefen, wireless charging not only eliminates maintenance expense and effort related to failed contacts, the on-board charger module is compact, which is a benefit for AMR vendors that don’t have much space on small compact AMRs for traditional charger contacts and transformer elements.
“I would prefer wireless charging in 99% of scenarios,” Siefen says. “The downside is they are more expensive than the spring-type contact chargers that most people use.”
Wireless chargers avoid maintenance issues and also support quick autonomous charging, says Harold Vanasse, global senior director of marketing for motive power at EnerSys, which introduced its NexSys AIR wireless charger earlier this year. NexSys AIR works with all EnerSys battery technologies across a range of automated materials handling equipment. While the currently available version works with AGVs, the company is currently developing a version to work with manually operated equipment as well, adds Vanasse.
“The wireless charging offered by NexSys AIR is fully automated, and it also eliminates all mechanical connections between the battery and charger. This eliminates all charging wear parts and their required maintenance,” Vanasse says. “In addition, a single NexSys AIR unit is able to charge multiple types of AGV equipment—giving operations flexibility in terms of the quantities and locations of their chargers, as well as the mix of AGVs they’d be able to deploy in their facilities. As a result, NexSys AIR fulfills the true promise of automation by eliminating both human intervention for the charging process and maintenance associated with mechanical charge connections, all while giving operations flexibility.”
The wireless charging space is attracting a mix of startups as well as more familiar names like Enersys. Not all wireless charging systems work exactly alike.
For instance, the wireless charging solution from CaPow uses thin charging “stickers” placed at strategic places over the movement surface to provide what it calls “continuous power delivery” to robots outfitted with CaPow’s receivers. Generally, with any inductive charging solution, some type of receiver module is placed on the robot to take in the charge, with an allowable air gap of a few inches or more.
Grayson Zulauf, CEO at Resonant Link, which offers wireless chargers, says the company’s wireless chargers can charge either manual lift trucks or autonomous units with a 10-inch alignment tolerance between the charger base station and the on-vehicle receiver module. That air gap creates time savings for operators and fleets, he adds, because it’s easier to position a unit for an opportunity charge, and with manual trucks, there is no cable to plug in.
Longer term, analytics that comb data from chargers could help an operation right size its fleet or optimize charging practices, but the immediate benefit is time savings for lift truck operators or the teams running automated fleets.
“Our view is that to make fleets as productive and cost competitive as possible, whether it is with mobile automation or manual lift trucks, wireless charging is going to be imperative,” says Zulauf.
About the Author
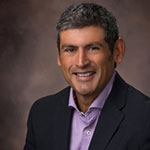
Follow Robotics 24/7 on Linkedin
Article topics
Email Sign Up
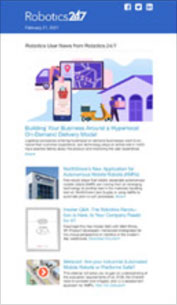
