Grippers may seem a small part of materials handling systems, in comparison with robot arms, software, and other costly components, but they're the only elements that directly interact with products, according to The Gripper Company ApS. The company today introduced its MAXXgrip system, which it claimed will enable warehouse and logistics robots to handle a wide range of objects.
“MAXXgrip is able to access a significantly wider range of SKUs with simplified training at previously unmatched throughput and still with high reliability and gentleness, compared to the state of the art for gripping,” said Preben Hjørnet, chief technology officer of The Gripper Co.
The Aalborg, Denmark-based company worked for two years with experienced system builders, suppliers, and end users to hone its design, he said. MAXXgrip is designed to take advantage of the latest 3D AI perception innovations to achieve human-like capabilities, noted Hjørnet.
“For the past half-year, people were desperate to get the product,” he told Robotics 24/7. “Vision perception had surpassed gripper performance, and the food, grocery, and e-commerce industries knocked on my door.”
The Gripper Co. designs to KPIs
Gripping capability directly influences overall equipment efficiency and the return on investment (ROI), said The Gripper Co. To help automation manufacturers meet key performance indicators (KPIs), the company claimed it has combined several technical innovations.
Hjørnet described five KPIs that the MAXXgrip is designed to satisfy:
- Variation: Counting picked items and their pose and neighboring environment
- Throughput: Facilitated by vision perception, motion control, and planning, as well as gripping
- Gentleness: Damaging SKUs can be the most costly fault, which he said it must be avoided even if cycle time suffers
- Ease of use: Counting relaxed gripper control, mounting, and maintenance
- Job customization: The ability to configure and apply targeted control settings and strategies on both a deployment and single cycle level to optimize performance
Just as hand-eye coordination is critical for human manipulation, so too must robot designers understand the key capabilities to maximize robotic gripper performance, he said.
MAXXgrip is designed for dexterity
The new gripper combines flexible fingers, a suction cup, and fast-mounting interfaces for safe handling, said The Gripper Co.
“The inherited self-compliance capability will not just ease up gripping training effort, but [also] provide a high level of adaptability to variance in part size, shape, surface and rigidness,” it said. “[The] same underactuated kinematics resist unintended collision that otherwise would lead to costly SKU and or tool damage.”
“The principle of having an extendable/retractable linear actuator as a one- or two-stage pneumatic cylinder relaxes the well-known challenge of collision avoidance and arm reach, as the approach/depart is carried out by the gripper itself, and the finger kinematics stay above the often restricted initial pick location deep down into a tole, or equivalent,” explained the company.
“Downscaling the job of the center pickup device—say, a single centered suction cup—to what its good at, namely peeling the pick-item up and out of the dense neighboring item collection,” The Gripper Co. added. “[It can] successively have a joint clamping finger arrangement leveled close to the TCP mounting flange. [This] adds the safe holding of the picked part while transferring to the placement location.”
More gripper specifications
The Gripper Co. said its new platform includes a modular architecture and “intensive topological optimization,” taking advantage of additive manufacturing and materials science. It weighs between 1.4 to 2.1 kg (3 to 4.6 lb.), depending on the configuration, and it can carry up to 5 kg (11 lb.).
Thanks to a telescopic linear air-operated actuator, the EOAT can grasp parts the size of a golf ball or small blister pack, depending on the suction cup arrangement. It can hold a wide range of shapes and surfaces, even loose or nonrigid objects, said the company.
The MAXXgrip's actuation is designed so it can be executed in parallel with the approach/depart motion segments used in pick-and place cycles. Its response time is 0.15 to 0.4 sec., but as this motion typically takes around the same time for the robot arm to move, it minimizes dwell time in successive picking cycles, said the company.
Test results show speedy picking
“The MAXXgrip has undergone extensive tests to ensure solid evidence of its capabilities and performance,” he added. “We have surveyed the series of job settings related to logistics and warehouse material handling robotics.”
Hjørnet said that the end-of-arm tool (EOAT) has been stress-tested with consumer products and parcels. The Gripper Co. worked with leading warehouse automation suppliers to specify the test criteria.
In testing, the gripper picked varied consumer goods from a 340 mm [13.3 in.]-deep tote and placed them onto a moving conveyor belt similar to placement into a cardboard box, recalled Hjørnet. The Gripper Co. recorded rates of 20 to 30 cycles per minute, or 1,200 to 1,800 picks per hour, he said.
Tote transport systems will have to speed up to support the gripper, Hjørnet remarked. “We'll see if the benchmarking for gripping things such as apparel or grocery items can keep up with the AI planning,” he said.
EOAT compatible with robot arms, controllers
Hjørnet added that MAXXgrip comes with a compact, high-performance Air Control Unit for vacuum and air flow control. Its control interface is intended to adapt easily to robot control systems.
The gripper comes with mounting rigs out of the box for all major robot arm brands, said The Gripper Co. It recommended using arms that feature a hollow wrist tool flange for the best cable and hose management.
Hjørnet said The Gripper Co. is working with major industrial and collaborative robotics suppliers, e-commerce retailers, and motion-planning firms.
Digital twins and submission form available
“We are very excited to have gotten to the point where we are ready to release the MAXXgrip into an industry that really needs a better gripper offering,” Hjørnet said. “[This will] strengthen their ability to meet customer expectations and accelerate the global deployment of warehouse and logistics robotics handling systems.”
In addition, The Gripper Co. has prepared reference cell programs including digital twins for simulating gripper units to accelerate adoption with vendors. Interested parties can submit an online request to be among the first customers.
“As we have conducted a large scale of tests, we hope to be able to give prompt and documented answers and guidance so our customers will have a seamless, quick, and exciting experience taking the MAXXgrip into their solutions,” said Kim Nielsen, CEO of The Gripper Co. “During the coming months, we will introduces a series of add-ons that will enable targeted applications to benefit from a collection of unit-level options, like soft fingertips, actuator variants, and more.”
“We'll be at LogiMAT 2023 and other upcoming events and will have webinars to demonstrate how to best use the unique capabilities of our platform,” Hjørnet said.
Founded in 2019, The Gripper Co. said its mission is “to make reliable, intuitive, and affordable gripping solutions in a sustainable fashion.” It is looking for resellers in the U.S. market, said Hjørnet.
About the Author
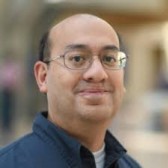
Follow Robotics 24/7 on Linkedin
Article topics
Email Sign Up
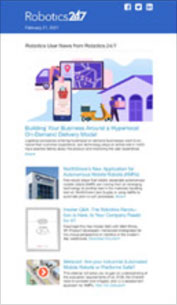
