Donnelly Custom Manufacturing is a leader in short-run injection molding of thermoplastics for industrial OEMs. To quickly switch between tasks and handle different objects, the company sought a cost-effective automated solution. A new collaborative robot can shift to a new task in a matter of minutes as the production line changes.
At its facility in Alexandria, Minn., Donnelly has deployed two robots (Rethink Robotics) on the manufacturing floor to perform duties that are often time-consuming and repetitive, but must be performed without error. The facility is equipped to handle more than 13,000 mold changeovers per year, including multiple changes per day. The robots are integrated to perform tasks such as removing parts from a conveyor belt and stacking each part on customized stacking devices, as well as counting and packing finished products for shipment to customers.
“In short-run molding, we thought using automation to keep up with demand would be expensive and laborious, as our production lines and product mix shifts quickly every day,” says Ron Kirscht, president at Donnelly. “The robots are able to switch tasks easily and adapt to this variable factory environment, allowing us to remain competitive on global pricing while delivering custom products on time to our customers. This also frees our employees to think more creatively and gives them the chance to work on more complex tasks and problem solving.”
About the Author
Follow Robotics 24/7 on Linkedin
About the Author
Follow Robotics 24/7 on Linkedin
Article topics
Email Sign Up
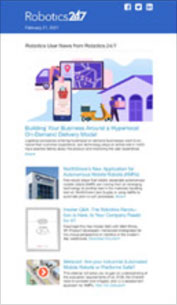