The rapid growth of e-commerce and rising consumer expectations are prompting retailers to adjust their order fulfillment strategies to keep up with these demands.
Luckily, several enabling technologies are coming of age which allow retailers to respond accordingly.
Here's a quick overview of the most effective strategies and solutions currently available, which can be combined and integrated in multiple ways to meet any fulfillment operation's unique needs.
Enhance Picking Productivity
Many DCs have already made the shift to paperless picking solutions, which increase productivity by up to 50 percent. Depending on your business needs, productivity can be enhanced with one or more of the following:
Pick-to-light - These scalable, easy-to-use systems combine intuitive colored displays that guide the pick with sophisticated algorithms that reduce movement times and accommodate hot picks.
Minimal training is required, and built-in diagnostics enable easy troubleshooting - making pick-to-light the industry's most efficient, accurate and high-speed order fulfillment solution.
Put-to-light - Similar to pick-to-light, put-to-light solutions direct pickers to the correct bin or slot to place an item. Best suited for batch-picking applications, put-to-light brings comparable improvements to accuracy and productivity when compared to traditional manual sorting.
Voice picking - This solution provides voice commands via a wireless network, leaving the picker's hands free while increasing picking speed and accuracy rates. Voice commands can also be programmed in multiple languages, significantly decreasing training requirements for non-English speakers.
Voice picking can be used as a cost-effective, stand-alone system or as a fully integrated enhancement of other solutions.
Radio frequency (RF) technology - Handheld and mobile RF devices are ideal for lower-velocity SKUs, enabling 99.9 percent accuracy and increasing productivity by 10 to 15 percent.
Mobile picking carts - For low-velocity applications, mobile cart systems combine advanced pick-to-light components, voice automation and RF scanners in a system with go-anywhere flexibility.
Improve Omnichannel Distribution with Put Walls
Whether DCs rely on operator-to-goods batch picking, disparate zone-picking processes, or an automated storage and retrieval system (AS/RS), put walls maximize efficiency by serving as points of demand consolidation.
Ideal for multi-line orders, flash sales or seasonal demand, put walls save time and labor by enabling intelligent order batching, adjustments and other allocations among wave, pick and put.
Automate for efficiency
Respond to ever-changing business needs quickly while minimizing labor with intelligent automation solutions:
Warehouse execution systems (WES) - WES software optimizes your facility with an operational brain, delivering real-time responsiveness with automated decisions based on constant analysis of orders, inventory, labor, processes and equipment.
Automated storage and retrieval solutions - Ideal for operations with high-turn inventory storage and short order cycles, AS/RS systems provide quick access to products, while reducing storage labor and footprint requirements.
Unit sortation - Designed for ultra-light, irregularly shaped and polybagged items, these systems deliver the highest throughput at minimum speeds for years of reliable, low-maintenance operation.
Intelligrated is an experienced designer, manufacturer and installer of all these solutions.
Related White Papers
Conquer High-volume E-commerce with Goods-to-operator Order Fulfillment
This white paper, the second installment in a series of AS/RS materials from Intelligrated, outlines how workflow adjustments and shuttle technology can increase efficiency for high-volume e-commerce fulfillment operations. Download Now!
Zone Skipping Strategies to Reduce E-commerce Shipping Costs
This white paper explains the zone skipping strategy and outlines the sortation technology best suited for operations, based on criteria like packaging type, footprint, labor availability and throughput requirements.
Using LMS to Address Omnichannel Challenges
The key roles labor management software play in omnichannel order fulfillment: meeting rising customer service expectations, driving labor savings and ensuring process rigor. Download Now!
Article topics
Email Sign Up
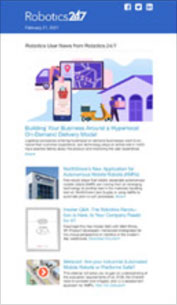
