Location: New Hope, Tenn
Square Footage: 212,000 square feet
Product: Cast iron cookware, cookware accessories, seasoned carbon steel cookware, enamel coated cast iron cookware
SKUs: 600 SKUs
Throughput: 800,000 to 1.3 million pounds handled per week
Shifts Per Day/ Days Per Week:1 shift per day, 5 days per week
In designing its new distribution center, Lodge Manufacturing was focused on reducing lead times, speeding up delivery times and creating the infrastructure to support a growing e-commerce channel today, and perhaps, drop shipments tomorrow. A key element to making that work is its Cloud-based WMS system and Apple-based mobile computing and data collection tools.
Click here to read the full feature article on the Lodge Manufacturing distribution center redesign
Receiving
While a small portion of total receipts are sourced elsewhere, the vast majority of inventory is manufactured just a few miles from the distribution center in Lodge’s foundry. New inventory is received (1) in standard pallet quantities identified by a pallet ID label. Pallets are scanned before they’re loaded onto the truck at the foundry, which enters that pallet into the Cloud-based WMS. The pallet is scanned again when it’s unloaded from a trailer in the distribution center by a lift truck operator using an iPhone for mobile computing and a Bluetooth scanner.
Storage
A newly received pallet can follow several paths. One is conventional putaway into a storage location. Pallets can be stored in a rack area dedicated to overstock (2) or reserve storage. Another is a rack area for standard picking (3). A third is that inventory can be stored in the new DTC area (4), or direct-to-consumer, which is set aside for each picking.
Large customer orders for 200 to 1,200 pallets, generally ordered by customers rolling out product to all of their stores, are directed to a large order production/staging area (5) where they are staged as they are received by the foundry. These are generally manufactured over a period of weeks or months and shipped (6) as required.
Last, if there is a customer order for the inventory on the pallet, it can be directed to an order staging area (7) where full pallets for smaller orders are staged and also where mixed pallets are built and staged for multiple customers. Pallets are also wrapped for shipment in this area.
Order fulfillment
The Cloud-based WMS manages multiple picking processes.
Pallet pick
If a customer orders enough for a full pallet, a lift truck operator receives instructions on an iPhone. The driver is directed to a storage location (2), scans the pallet and location, and is then directed to the order staging area
Drop zone
When several customers order the same mix of product, lift truck drivers are directed to retrieve pallets from storage and deliver them to a drop zone in the order staging area (7). There, the inventory is used to build mixed pallets that are then labeled; stretch wrapped; and staged for shipment (6).
Mixed pallet pick path
Lift truck operators are directed by the system to storage locations in the standard picking rack area (3). Items are then scanned to the pallet. Products were originally slotted according to velocity; but Lodge is presently reconfiguring the system to slot items according to the best way to build a pallet.
As an example, a 14-inch skillet makes a great platform for stacking odd sized items, such as accessories. Smaller skillets, meanwhile, provide a good base for a pallet load. Once a pallet is built, it’s delivered to the order staging area (7), where boxes are labeled, the pallet is wrapped and then staged for shipping (6).
DTC pick area
This new pick area (4) is in development. At present, it is used to manually fill customer orders received online, using a cart pick process. In the future, Lodge intends to expand this area to provide drop shipments for its retail customers. Items are picked, labeled for shipment and delivered to a parcel shipping area (8) for UPS and FedEx pickup.
Packing and shipping
The shipping process begins when a customer order is received in the system. Because the WMS knows the weight of products, the shipping department is able to call and arrange routing before orders are picked.
Per above, once a pallet is considered ready to ship, it is labeled, stretch wrapped, and staged at an assigned shipping dock door (6), based on the routing information.
System suppliers
About the Author

Follow Robotics 24/7 on Linkedin
Article topics
Email Sign Up
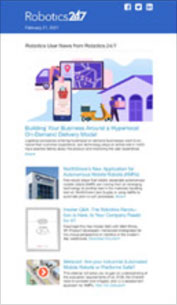
