J&J Vision Care - Jacksonville, Fla.
Size: 200,000 square feet
Products: Vision care products
SKUS: 30,000+ SKUs and growing
Throughput: 10,000 orders per day across a global distribution
Shifts: 24/7 operations
Employees: 200+
J&J Vision Care’s Jacksonville facility uses a variety of picking technologies to fill orders based on the velocity of movement of the SKUs involved. Here’s how product flows through the facility.
Receiving:
The warehouse is adjacent to J&J Vision Care’s manufacturing plant and receives in the in-bound finished goods area (1) on a 24/7 schedule. Raw materials arrive at the back end of the plant, and are processed into finished products that are then transferred by lift truck into a quarantine area prior to a quality control inspection. Once new product is approved, it is received into the warehouse management system (WMS), staged for putaway and available to fill customer orders.
Putaway:
The legacy WMS chooses a storage location in the pallet rack storage area located in the finished goods warehouse (2). Lower level locations are designated for case picking of fast movers; upper levels are designated for reserve storage. The lift truck driver scans the pallet into the appropriate storage location.
Replenishment:
Manual flow racks support picking processes in the A-frame picking area (3) and pick-to-light pick modules (4). When an inventory location reaches its min/max level, a replenishment signal is sent to the WMS. Associates pick cases to a stock picker in the finished goods warehouse (2) and then induct the cases onto the conveyor system. Cases are then conveyed and sorted to the right zone, where an associate scans a case into the appropriate flow rack location.
Re-slotting:
SKUs are assigned to a pick technology based on their velocity: The fastest moving SKUs go to the A-frame (3); then to the pick-to-light (4) and then to the new automated storage and goods-to-person technology (5). A new product launch, for instance, will begin in the A-frame (3) and then move to the pick-to-light (4) as demand levels off and new products outpace the current demand. J&J Vision Care employs an optimization tool that looks at the order volume for each SKU and recommends re-slotting as required.
Order fulfillment:
All orders begin the same way. An order tote is electronically married to an order through a bar code scan and is then inducted onto the conveyor system.
The WMS analyzes the order and then directs the tote through the facility. The first stop is the pick-to-light pick mezzanine (4). The VLM pick area, which handles just a small number of SKUs, is also located in the pick-to-light area. Once all the items for an order are picked in that zone, a robot takes that tote and empties it into the main tote that will go to another pick area where associates use wrist scanners for hands-free picking. If required, the tote travels next to the A-frame (3), where items are automatically dropped into the tote. Finally, it travels to the new goods-to-person pick station (5).
In the goods-to-person area (5), totes are picked by mobile robots within the storage units and then conveyed to the pick station. There, the associate is directed by light to one of the four quadrants in the tote. The associate picks the right number of pieces and places them in the order tote. The order is now ready for packing.
Packing:
Once the order is picked complete, it is conveyed to one of the packing stations in the order packing area (6). At that point, every item is scanned to verify that the lot number and SKU are correct. Once the WMS verifies that the order is complete and accurate, a shipping label is printed and applied to the shipper box. It is then sealed and placed on the shipping conveyor and delivered to the out-bound shipping area (7). From there, the box is conveyed to the right lane for UPS or FedEx shipping, depending on the location of the delivery.
A crossdocking operation is used for some large retail customers ordering for several hundred stores, requiring J&J to pack orders by store. In those instances, a shipping carton may contain 30 to 50 orders that are overnighted to the retailer’s DC. There, the cases are opened and the individual orders are sorted by store.
System suppliers
System integration and conveyor: Bastian Solutions
Automated storage and goods-to-person picking: OPEX Corporation
A-frame picking solution and conveyor: SI Systems
Spiral conveyor: AmbaFlex
Bar code scanning: Cognex
WMS: Legacy system from J&J, picking system from SI Systems
Mezzanine: Wildeck
Lift trucks: Crown
About the Author

Follow Robotics 24/7 on Linkedin
Article topics
Email Sign Up
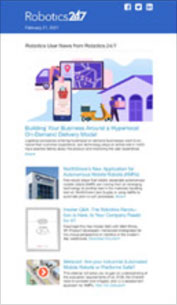
