If a new process for handling consumer electronics continues to deliver results, the future of materials handling may include a striking red robot with big digital eyes, bushy digital eyebrows and a quizzical expression that makes you want to smile.
At Genco’s campus in Ft. Worth, Texas, Baxter, as the robot is known (Rethink Robotics), is working side by side with team members on a packaging line. The campus includes 1 million square feet of distribution space spread across three buildings and handles the return, repair and refurbishment of consumer electronics products such as cell phones and GPS navigation systems.
In this process, employees load four products—one at a time—into a form that goes into the sealer. When they come out the other side, Baxter picks and places four packages at a time on a takeaway conveyor that delivers them to the next step in the process.
Why the interest in piece-picking robots? “The cost and flexibility of the technology has lowered the barriers to entry for robotics,” says Jeremiah Miele, a Pittsburgh-based project engineer who is leading Genco’s robotics efforts. Read more about how Baxter works in this facility.
“There’s an ability to do things with robotics that didn’t exist five or 10 years ago,” adds Pete Rector, executive vice president of technology and lean solutions for Genco. “We think it’s just a matter of time before robotics are mainstream in materials handling. It’s going to happen faster than people think.”
The journey to lean distribution
As a rule, third-party logistics providers (3PLs) such as Genco are reluctant to adopt mechanized equipment. The short contracts common to the business aren’t compatible with the multi-year payback associated with automation, something Rector and Miele acknowledge. “If you’re 18 months into a three-year contract, you’re going to be reticent to make an investment in something with a two-year payback,” says Rector, “especially if the customer won’t help you capitalize the cost of the new technology.”
What’s more, the most common mechanized technologies, such as conveyors, sorters and carousels, are bolted to the floor. If a customer brings the processes in-house at the end of the contract and doesn’t need the equipment for its uses, the 3PL might not be able to repurpose the equipment for its next client.
As the largest U.S.-owned 3PL in North America, with 40 million square feet of distribution space, Genco is rethinking that traditional approach to automation. In part, the exploration of automation is driven by a commitment to lean distribution and continuous improvement focused on three areas.
1. The elimination of waste: “Most organizations are good at adding processes but not so good at taking them away as the need changes,” says Rector. Over time, even lean processes that have not been “refreshed” can become cumbersome. “We want to remove anything that no longer adds value,” Rector says.
2. Centralize processes: Whenever possible, Genco wants to centralize common tasks in one place. “We’d rather have three people doing something in a single centralized location than more people doing that same thing in multiple facilities,” Rector explains.
3. Mechanize where possible: As described by Miele, Genco looks for applications where automation can be a workforce multiplier. That is a task where one piece of equipment can do the work of several people, ideally across multiple shifts. “We want to reserve for people tasks that people do well and reserve for machines those things that are repetitive and standardized in nature,” Miele says. “In situations like removing packages from forms, machines help people perform better.”
The evolution of some types of materials handling automation is putting it in reach of 3PLs. For instance, robots like the ones being used in Ft. Worth have come down dramatically in price. “With end effectors and warranties, the robot we’re using costs around $35,000,” says Miele. “You don’t need an engineer to program it—a team member can train it. Then, it can work side by side with a team member from a safety perspective, and it is very reliable. If the function is no longer needed, we can put it on a truck, ship it to another facility and get it up and running in a very short period of time.”
What’s more, some new technologies are more flexible than conveyors and sorters—or even other materials handling robots. Baxter does not have to be fenced off like a palletizing robot. It can work side by side with a team member. It is not bolted to the floor, which allows it to be easily moved from one workstation to another within a facility. “You can train the robot to do a task, like run 50,000 things that need to be packaged and shipped,” says Miele. “When that job is done, you can unplug the robot, move it to another area, retrain it and you’re done. We’ve never had that type of agility before.”
Adopting robotic technology
The Genco robotics project began to take shape when Rector read a press release about the Baxter robot. Following a conversation with the manufacturer, a local distributor gave the Genco team a demonstration of the robot’s capabilities. They were intrigued. “The user interface is so easy to use that the operator working next to the robot can make simple modifications to how the robot operates just by moving the robot’s arms,” says Miele. “In the past, that is something would have required engineers and technicians to do during a shift change.”
By the time they visited the Rethink Robotics booth at ProMat last January, the team was fairly certain it wanted to run a pilot program. They chose the Ft. Worth, Texas, facility because it was a “target rich environment”—a facility with a lot of manual handling. And, Brian Morris, the director of engineering for the technology group in Ft. Worth, was willing to give it a go.
Following a visit to Rethink Robotics headquarters in Boston, a robot was shipped to the Ft. Worth facility in June. The Genco team did a safety assessment to find out if the robot safely did what it was advertised to do. Convinced that the robot could indeed work side by side with a teammate, they looked for an application within the Ft. Worth facility for a pilot and chose unloading the packaging sealer.
Before launching the pilot, Miele and Morris emulated the application as closely as possible in a laboratory environment. They mocked up dimensions for the sealer and the fixture and used live product. “We were checking the full range of the robots motion and monitoring cycle times,” says Morris. “We wanted to be certain that if we did roll out into a live pilot on the line that we’d have a high probability of success.”
During the lab process, they designed a new hand for the robot. The one that came stock could support a variety of applications, but was not ideal for this application.
In mid-July, roughly a month after receiving the robot, the pilot went live. The process is relatively simple (see page 25). Upstream, Genco teammates place the consumer electronic devices and accessories such as power cords and collateral material into a clam shell package. When the clam shells arrive at the workstation, a teammate loads four packages—one at a time—into a turntable fixture. Then, they indicate to the sealer that it can rotate to the next position. The robot communicates with the sealer through a programmable logic controller (PLC). Once product is sealed, the turntable rotates and presents the fixture to Baxter. The robot removes four packages at a time from the fixture and deposits them on a takeaway conveyor.
According to Miele, the Genco team took a cautious approach to the pilot. “We babysat it for the first two weeks,” says Miele. “But after that, the robot was going full speed.” Teammates got the hang of working with it quickly—some in as little as half an hour. “We weren’t sure how our teammates would react to working with a robot,” says Morris. “But, the teammate in charge of Baxter had no problems, and we found that other teammates were excited about seeing the robot at work.”
By the end of the month-long pilot, Miele and Morris were convinced the robot could meet the reliability and cycle times required to go live on the line and that they had enough data to make a business case for robots.
Getting an ROI
What then was the business case? First, because the robot can be used across multiple shifts, Genco has seen an increase in productivity. More importantly, the pilot revealed other opportunities to take waste out of the overall process, such as the addition of a new conveyor line to feed downstream processes and opportunities to combine or eliminate tasks within the existing process. “We now have a roadmap and a plan of attack to make those changes,” Miele says. They have also identified other processes where the robot can be applied—expanding that multiplier effect.
As with any new technology, there are limitations to what the robot can do, says Rector. “It’s a little slow, and it has a limit on the payload it can pick up,” he says. At the same time, Genco is offering suggestions to the manufacturer on how to improve the robot. “We want to be on the ground floor of this technology,” he says.
More importantly, Rector believes there is a future for robotic materials handling in distribution. “As people, we have a limit on how fast we can work on our own,” he says. “And when you look at robotics, there’s an ability to do things now that didn’t exist five or 10 years ago. Imagine if you take a robot like Baxter and equip it with Siri. You now have a robot that can talk to you. How far is that? It’s closer than you think.”
“As a company,” he adds. “We want to be part of that.”
System suppliers
Robots: Rethink Robotics
Automatic lift trucks: Balyo; Yale
About the Author

Follow Robotics 24/7 on Linkedin
About the Author

Follow Robotics 24/7 on Linkedin
Article topics
Email Sign Up
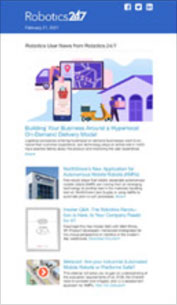