Last month, I received a copy of the 4th annual survey of manufacturers and distributors by Sikich, a Chicago-based accounting and consulting firm. You can download the whole survey here. The survey goes out to Sikich clients as well as others across the U.S.
Before looking at the results, I had a chance to talk to Jerry Murphy, the Sikich partner in charge of the survey about what struck him by the results. “A lot of what comes out of this are best practices, and that allows us to make suggestions on what business leaders should be doing to address the challenges identified in the report, “ Murphy told me.
What were Murphy’s take aways? “Over the last couple of years, the Internet of Things has become a bigger pain point for the respondents along with workforce challenges that are becoming a barrier to growth,” he said.
“I talked to several clients just last week who were turning down work because they don’t have the resources.” And what surprised him the most? “One is that 75% of respondents said they were prepared for cyber security; they’re confident,” he said.
More importantly, he added, in many areas, “the respondents are behind in taking steps to address the issues confronting them. They’re getting attention, but not enough planning is being done.”
The survey covered a variety of topics, including things like succession planning. I honed in on three: robotics, the Internet of Things and the talent shortage.
Internet of Things
The real-time, connected supply chain has long been a dream of supply chain managers, and the potential for collecting more actionable information at more nodes in the supply chain using sensors, RFID, bar code scanning, GPS and cellular communication means that dream is closer to reality than ever.
That is the promise of the Internet of Things, where every individual, device, machine and asset that matters can communicate in real time. At the same time, Sikich round that while awareness of IoT is increasing, adoption is slow.
Only 23% of respondents are already using IoT (9%) or are implementing now (14%). More than 75% said they are not using it yet, including 13% who said it is irrelevant to their business and 30% who aren’t sure what IoT is.
Talent Acquisition
Survey respondents ranked a lack of qualified workers as their number one barrier to growth in 2018, which will come as no surprise to anyone who follows the news. Despite that, most respondents reported not taking proactive steps to attract talent, including building a talent pipeline before a position opens.
The five most commonly deployed strategies for attracting talent included engaging an outside recruiter (24%); growing talent from within (18%); employee referral programs (15%); paying above market wages (13%); and creative and unique benefit offerings (11%). Only 11% reported that they’re building a pipeline of talent prior to an open position.
Robotics
As anyone who attended Modex in Atlanta this past April know, mobile collaborative and piece-picking robots were the stars of the show. Driving the interest in robotics is a perfect storm of a labor shortage on warehouse and shop floors; dramatically improved reliability; and lower costs for sensors, computing power and off-the-shelf components.
Sikich notes that according to on industry projection from ARK Investment Management, the per-unit-cost of industrial robots could drop to less than $11,000 by 2025. The interest in robotics is reflected in the survey, while 39% of respondents said none of their operations are performed by robots, more than half (60%) reported using robotics in at least some of their operations.
Murphy’s call to action, based on the results? “Every business is going to be impacted by these issues differently, but they’re issues that they can’t ignore,” he said. “They need to take the time to incorporate these topics into their long-term planning.” Remember you can click here to read the whole survey.
About the Author

Follow Robotics 24/7 on Linkedin
About the Author

Follow Robotics 24/7 on Linkedin
Article topics
Email Sign Up
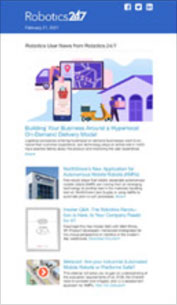
