HP is delivering a polypropylene (PP) material for additive manufacturing. The new HP 3D High Reusability PP, enabled by BASF, is a durable and chemically resistant material that has been qualified for HP’s production-grade 3D printing systems, and is ideal for customers in the automotive, consumer, industrial and medical sectors.
HP also unveiled a new partnership with Oechsler, a global design and manufacturing player, to develop applications for both the new PP and HP’s broader materials portfolio, as well as new customer Cobra Golf for its Metal Jet 3D printing technology.
“The response to the COVID-19 crisis is a watershed moment for the industry. HP and its partners have 3D printed more than 2.3 million parts to bridge supply chain gaps, enable local production, and help healthcare professionals on the front lines,” says Ramon Pastor, interim president of 3D Printing and Digital Manufacturing, HP Inc.
Adds Pastor, “As we navigate this new landscape, we continue to execute on our strategy and push innovative new 3D printing materials, solutions, and partnerships forward to help our customers re-open manufacturing and deliver disruptive innovation for the world’s industries.”
PP Designed to Improve Sustainability
Polypropylene is a material ideal for a wide range of automotive, consumer, industrial, and medical applications. The new HP 3D High Reusability PP enabled by BASF provides customers with a genuine new additive manufacturing material offering the same properties as commonly used PPs in injection molding. With its chemical resistance, low-moisture absorption, and long-term durability, PP is ideal for piping, fluid systems and containers. For example, automakers will be able to use the same PP for prototyping and production of final parts found in vehicles’ interior, exterior and under-the-hood.
Developed in partnership with BASF for HP’s Jet Fusion 5200 3D Series, the new PP delivers high productivity and minimizes waste for industrial-level manufacturing. In addition to breakthrough economics and performance, the new PP helps reduce waste by enabling up to 100% reusability of surplus powder.
HP is jointly developing entirely new PP applications with partners, parts providers and customers including Extol, specializing in plastics engineering and innovation with industry leading plastic assembly technology, custom automation and engineering services; GKN Powder Metallurgy/Forecast 3D, a provider of advanced industrial 3D printing, short-run manufacturing and high-volume production; Henkel, high-impact adhesives and engineering solutions provider; Oechsler; and Prototal, one of Europe’s parts manufacturers.
New Professional Services, Expanded Alliances
In additional news, HP announced new and expanded 3D Professional Services offerings and industrial alliances, including:
HP 3D Professional Services: HP is unveiling a variety of new professional services capabilities including design optimization for breakthrough applications, manufacturing process streamlining to enable mass customization and scale production, and applications identification and discovery services.
BASF and HP are advancing their strategic alliance to jointly develop new applications with customers in the automotive, consumer, industrial and medical industries. With the new PP and the introduction of the ULTRASINT TPU01 thermoplastic polyurethane, the two companies are working together to accelerate the design and mass production of 3D printed parts.
A new strategic alliance with Oechsler AG will span the product lifecycle from application design to production of final parts. Oechsler is using its fleet of HP’s Jet Fusion 5200 3D Series printers and its materials portfolio to help leading automakers, global consumer electronics companies, home and commercial appliances, and innovative medical device providers produce various new applications.
Fast Radius has qualified as a new member of the HP Digital Manufacturing Network, a global community of HP production partners to help design, produce and deliver both plastic and metal parts at scale leveraging HP 3D printing solutions. The HP Digital Manufacturing Network includes partners in the United States, Asia, and Europe.
Advancing Metals Mass Production
Cobra Golf, a golf club manufacturer, innovation and design, has selected HP Metal Jet for its entry into 3D printing for product innovation and parts production. Cobra, HP and Parmatech are working together on a strategic, multi-year product roadmap, that leverages the design and manufacturing benefits of HP’s additive technologies to deliver performance-based golf equipment.
Sources: Press materials received from the company and additional information gleaned from the company’s website.
About the Author
Press releases may be sent to them via [email protected]. Follow Robotics 24/7 on Facebook
Follow Robotics 24/7 on Linkedin
Article topics
Email Sign Up
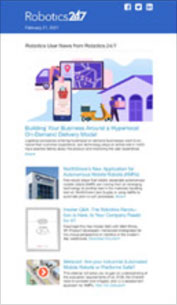
