As society becomes increasingly aware of the importance of health and wellbeing, workplaces are doing everything they can to ensure their employees are happy. But when it comes to seasonal peaks, it can be challenging to maintain a healthy work-life balance while meeting higher demand.
Give your elves a break
For many retail warehouse operators, a better work life balance around the seasonal period is an unrealisable dream. While they long to be at home with their families, they instead deal with the pressures and demands of the festive rush. As staff motivation dwindles, so does productivity.
Add to that the rise in seasonal affective disorder, the lack of daylight due to longer shifts could lead to even more challenges for your staff. What is supposed to be the most wonderful time of the year can quickly turn into a wellbeing disaster. And when the holiday season can represent as much as 30 percent of annual retail sales, this is surely something to be avoided at all costs.
Robotic harmony
Advances in technology are constantly helping us to improve our lives. Robotic vacuum cleaners allow us to put our feet up instead of manually cleaning floors, and personal assistants in our smartphones mean we don’t even have to move our thumbs to make a command. We are accepting robotics and artificial intelligence into our lives more and more, because it makes things easier. Warehouses should be adopting this attitude too.
Collaborative robots, or cobots, are already helping some warehouse operators to achieve a better work-life balance. Cobots are robots that are designed to work alongside or directly interact with humans in a shared space. This concept combines the speed and efficiency of a robot with the human advantage of a conscious mind.
Swisslog’s ItemPiQ is an excellent choice for all year-round productivity gains and our robots do not mind not having a break at Christmas! Equipped with safety sensors and four gripping possibilities, it allows the human operator to focus on adding value to individual orders. The robot can pick and place products from a source into a target bin or carton, allowing companies to better cover seasonal peaks.
A flexible solution
Modular good-to-person systems, such as CarryPick, offer another efficient way of boosting productivity throughout seasonal periods. These automated solutions can be expanded and adapted according to changing demands. Throughout the busier times of the year, more robots can be added to the system to further increase productivity and decrease pressure on the human workforce.
CarryPick is an innovative automated storage and picking system designed for multi-channel intralogistics. A swarm of mobile vehicles, developed by Swisslog together with its parent company KUKA, delivers mobile racks to workstations for picking and reducing the travel path for operators.
For the Hamburg-based lifestyle company HAGEL GmbH, CarryPick was the ideal solution to meet growth-related challenges. A total of 28 mobile robot units perform all transport tasks in the warehouse. The Swisslog software platform SynQ ensures that the average of 190,000 permanently stored articles quickly reach the workstations in the picking process.
CarryPick for work-life balance
Picking is often considered one of the most labour- and cost-intensive processes in intralogistics. Especially during peak seasons, relying on hard-to-find labour or adding pressure to existing staff significantly increases business risk. The use of CarryPick can mitigate that risk in multiple ways.
Goods-to-person picking solutions increase the productivity of warehouse personnel. Many CarryPick customers find they can increase pick rates by as much as 50 percent using goods-to-person picking, reducing the need to further burden staff during peaks. Less pressure means happier staff and an improved work-life balance throughout the festive season.
A Swisslog CarryPick solution can be designed to have more robots only for Christmas. When you don’t need them anymore, we can take them back.
CarryPick for returns
The volume of returns can also increase for some warehouses over the seasonal period. Some operations opt for a separate system to deal with returns, but there is always the question of the challenge it creates for already time-pressed staff.
The CarryPick system is designed to meet the rigours of today’s return-heavy logistics. The solution allows returned items to be stored using random putaway and picked first in subsequent orders. Algorithms behind CarryPick are configured to manage up to 20 orders simultaneously at any one pick station, meaning returned products are allocated to new orders in the quickest time possible.
The wellbeing robot
As robotics increasingly make our everyday lives easier, it’s time for retail warehouses to follow suit. There is no question about the time-saving, productivity and cost-efficiency benefits of robotic and data-driven solutions.
But customer expectations over the seasonal period rise every year, and without the aid of automation, the wellbeing of your workforce will likely be compromised. For companies looking to prioritise the wellbeing of its employees at this important time of year, there is a clear advantage to investing in a modular automated solution like CarryPick.
Article topics
Email Sign Up
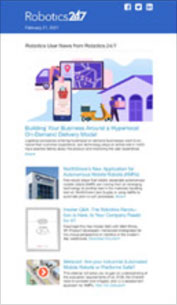