When it’s time to move from manually building a unit load to automation, more facilities are taking a closer look at robotic palletizers, says Terry Zarnowski, sales and marketing director for Schneider Packaging Equipment.
“The flexibility of robotic palletizers makes them attractive,” he adds. “They can perform simple or complex case stacking patterns, build mixed pallets of different products and sizes, and palletize multiple SKUs simultaneously. Plus, the same robot can easily be adapted to handle a variety of different products: from small bags to 120-pound bags of concrete, to any case type, including trays, lidded trays, standard regular slotted cases or half slotted cases and bundles.”
Placing a single robotic palletizer in a central position (to be fed by two or more lines), says Zarnowski, saves space while increasing efficiency because it can build multiple pallet loads concurrently instead of only sequentially.
“Unlike traditional palletizing equipment that may need multiple mechanical changeovers for different unit load patterns, a robotic system can be ready to go with a simple control menu change,” he explains.
Since a conventional palletizer can only palletize one type of case or product at a time, a long case accumulation conveyor is required prior to their release to the unit load, as are mechanical components—such as conveyor laners, stops, pushers, turners and sizing mechanisms—that sort, pre-orient and align the cases.
Not so with a robot, says Zarnowski, “The robot’s end-of-arm tool picks one or more cases and rotates, flips and/or stacks the cases flat, sideways or at any angle to orient them as required to build the unit load.”
Also, because robots palletize with fewer components than conventional counterparts, they typically offer greater reliability and uptime while using less energy, says Zarnowski.
“Robotic arms are rated for 80,000 hours. That’s an extremely high mean time between failures and one that is far greater than any mechanical system consisting of cylinders, sensors, solenoids, air or hydraulic systems and discrete controls,” he says. Further, typical robot maintenance is an annual grease change and periodic cleaning and lubrication of the end-of-arm tool.
Read more Packaging Corner.
About the Author

Follow Robotics 24/7 on Linkedin
About the Author

Follow Robotics 24/7 on Linkedin
Article topics
Email Sign Up
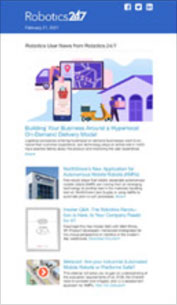