This is fourth and final article in the Southwest Research Institute's series on collaborative robots. In previous posts, we examined the benefits and limitations of cobots.
Assuming you’ve decided that a cobot is indeed the right choice for your application, read on. Now let's look at how to pick the right cobot from the many options on the market.
Factors to consider when cobot shopping
As described in previous posts, cobots are not all the same in either performance or ease of use. Cobots can fill a wide range of roles, but the best cobot for teaching and educational purposes may not necessarily be the best cobot for an industrial process such as sanding or assembly.
When selecting a cobot, the first question to answer is what are you trying to do with the cobot? The answer to that question will help determine what attributes are most important to you. Once you have answered this question, consider the following factors, evaluated with level of importance for your application, to narrow down your options.
Force-controlled or force-limited: All cobots are force-limited, but not all cobots are force-controlled. If you are solely worried about safety, force-limited is fine.
However, if you want to use force control in your process, you will want to make sure that your cobot is designed to provide high-resolution, low-latency force feedback that can be used in the control system.
Ease of programing and setup: If this is a priority, make sure that the cobot you are looking at is easy to get working out of the box. While cobots are generally designed to be easier to set up and start using compared with traditional robots, some cobots are easier to use than others. Some cobots come with everything they need to work right out of the box and can be simply plugged in and turned on. Others have a setup complexity similar to traditional industrial robot arms.
In addition, cobot control interfaces vary in complexity. Some are designed to be intuitive, while others are simplified versions of traditional robot controllers with similar levels of on-pendant programming capabilities.
While simplicity is typically an advantage, an operator who has experienced working with traditional robots from a certain manufacturer may prefer cobots from that same manufacturer due to interface similarity.
Ask suppliers for a demonstration of cobot models you are interested in, either in person or through instruction videos, when evaluating ease of use of these systems.
Reach and payload: This is where comparing spec sheets comes in handy. In general, newer cobots, with advanced force control, also tend to have higher payloads.
Remember that end effectors tend to gain weight during development, and it is a good idea to have some margin on the design load.
Repeatability: This is also something that you can find on the spec sheet. It is worth putting some thought into how much repeatability you need.
While a small number is better, it is also more expensive to achieve, and you might be able to open your options if you are able to open your spec.
Joint configuration: Many cobot designs use an eccentric wrist design. This can give some unusual performance characteristics that are not found on traditional wrist designs.
A robot with an offset wrist design tends to move significantly more than an inline wrist cobot in small, dexterous operations. This can cause issues in confined spaces and with cable management, as it sometimes takes a substantial amount of joint motion to move the end effector a short distance. This challenge prompted SwRI to develop a specialized cable management system.
Smoothness: This is not something that you are likely to find on a spec sheet, and it is best to test drive a robot, or at least watch a video of one moving, to evaluate it. This is mostly a problem for budget models with low repeatability intended for educational or hobby purposes. In that case, some oscillations during motion might be perfectly acceptable.
If you are interested in a cobot that looks good in still pictures but has an unusually low price, try to find some videos of it moving. Jittery motion is not necessarily a problem, but you want to make sure you know what you are getting.
Ease of use with ROS: SwRI uses the Robot Operating System in almost all its projects, so this is a consideration for us. If you also use ROS, it is always helpful if the robot is currently supported by existing ROS drivers and Unified Robot Description Formats (URDFs), which are essentially robot model files.
However, it is also possible to write your own drivers and URDFs, so this is a relatively minor consideration.
Some Closing Thoughts
Collaborative robots are becoming increasingly useful and capable. It is worth remembering they are really nothing more than force-limited industrial robots. This opens some applications and opportunities for automation and can allow safer operation near human workers.
Also note that cobots still come with many of the same limitations and challenges as traditional industrial robots. As with traditional automation, the key to developing a good solution is understanding the problem and what is required for the system to be beneficial.
If a cobot is part of that solution, then hopefully this guide gets you one step closer to selecting the right one for your application.
To learn more, visit SwRI’s Collaborative Robot Laboratory or read other articles in our cobot series:
Post 1—What Is a Cobot, and Does My Company Need One?
Post 2—Are Collaborative Robots Really Safe and Easy to Use?
Post 3—Choice of a Cobot or an Industrial Robot Depends on the Application

About the author
Cody Bressler is a senior research engineer at the Southwest Research Institute in San Antonio, Texas. This article is reposted with permission.
Article topics
Email Sign Up
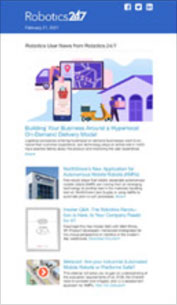
