At Pack Expo in Las Vegas last month, Honeywell International Inc. announced its Smart Flexible Depalletizer. The system is designed to automate the process of unloading pallets, reduce the risk of injury, and mitigate the effects of labor shortages.
Thomas Evans, chief technology officer at Honeywell, spoke with Robotics 24/7 about the Charlotte, N.C.-based company's latest technologies and its approach to developing for warehouses and distribution centers.
How was Pack Expo 2021?
Evans: It was busier than I expected. It was the first time I've given an in-person interview or had a live presentation rollout since the pandemic began. It was great to have the team on the floor.
Our research and development team was working this year to be ready for all enchancements and performance benchmarks to be met by August.
Developing and testing the Smart Flexible Depalletizer
In developing products such as the Smart Flexible Depalletizer, what has been more difficult—hardware like the gripper, or the machine learning (ML) aspects?
Evans: Our biggest challenge is bridging the gap from R&D to production. We want to make sure the voice of the customer is included dring product development.
Robotics is multidisciplinary. My R&D team includes simulation, robot controls, machine vision, ML, and AI.
We ran pilots with major retailers at the beginning of the year, concurrently with our own organic development schedule. It was great for our internal engineers to get insights into what customers want.
We want to make sure the product is deployable and that we can maintain uptime. That's where it's helpful to scale with Honeywell—they company as a whole enables to integrate quickly and maintain and service all customers.
Can you give an example of something you learned during the pilot projects?
Evans: Any one that's going to be running, for ROI [return on investment], customers will throw everything at it. We had retailers pushing our system to the limits, so we had to determine if something was a development issue or them trying to see if they could break it.
It was a great learning experience. We're measured on uptime, reliability, and performance. The customer guides success by throughput, or packages per hour.
Another concern from a certain vendor was how to handle particular packages and pallets. With force-torque sensing, we found that our system could move differently or slow down for more fragile packages.
What aspects of artificial intelligence is Honeywell working on?
Evans: We're focused on AI and ML, both for vision and motion control. We want to have optimization with ML base models to perform reliabliy and get caught up to speed, such as during holiday rushes. Our product needs to accurately maneuver around production to pick and place parcels to a conveyor.
As for capacity, the vision system needs to be able to look for products on the spec sheet. Something could be outside our dimensions or weight because of the form factor of the robot arm and end-of-arm tooling. If customers ask us to increase the payload for other dimensions, we can put it into our development cycle.
As machine learning models mature, we try to generalize global solutions for 80%. We also want to go to the customer site and see operations in the commissioning phase for two to four weeks. We can go live in the same amount of time as other automation equipment.
Now that we've gotten to the commercial release of our product, we're halfway there. Then project execution will meet their demands at rollout.
Honeywell keeps focus on customers
Speaking of meeting customer demands, how have you managed during the rapid growth of e-commerce?
Evans: We have global service support and project engineering teams. They're trained by our engineers who have developed the systems and know them inside and out.
My operations division is a hybrid between R&D and mechanical engineering. The dedicated team has standups first thing in the morning.
In the commissioning phases, pilots, and lab environments, they work with LSS [Level Six Sigma] teams on installation. The teams have also worked with our machine vision scientists and can service robots in the field, thanks to the reach of Honeywell.
At the same time, how have you tightened your focus for the palletizing system?
Evans: We're initially looking at depalletizing in North America. We had 20 to 30 R&D engineers within Honeywell doing this.
We've had interest from other sectors, but we want to see how far-reaching the technology can be. It could upstream, at parts, and also on the back end for shipping and receiving in e-commerce, retail, distribution, and fulfillment.
The technologies that make up this product—robot control and machine vision, hardware and software—could spin off into other products for bin picking and more applications. Mixed-SKU palletizing is on the horizon.
Depalletizing and other robots
Honeywell has also developed a robotic unloader—could you see that working with the Smart Flexible Depalletizer?
Evans: That's where I want to go. We want to look for a commercial product user as a co-developer. We need to get to high-volume runs to understand the intricacies.
To get to commercialization, we have to develop the data interfaces and see how a single cell and a network of robotic cells can work.
What about compatibility with autonomous mobile robots, or AMRs?
Evans: One of the applications we see is an integrated solution. Our customers would like our traditional pallet conveyor to close that loop of automation.
If it's a brownfield site, you may not have the square footage, which is where AMRs or a shortened section of pallet conveyors could be useful.
It could be the same way with the unloader and traditional material handling equipment, which could fold into our larger portfolio and experience.
Peak season and beyond
How have Honeywell's existing customers reacted to your latest product?
Evans: Right now, a lot of customers are preparing for peak season, so they don't want to deploy new automation. We're available to deploy and to provide insights or any solutions that would make their operations more efficient.
Looking forward, we want to keep enhancing the product and growing what we're doing in development. In 2022 and 2023, we'll see where this product can go and serve customer demand.
We're currently developing our roadmap and strategy for next year.
How realistic are goals for fully autonomous facilities?
Evans: As long as there are edge cases, we want the most advanced vision systems and ML models to address them. Given the complexities of automating, we will still need human intervention for some time, but we want to minimize that.
About the Author
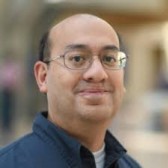
Follow Robotics 24/7 on Linkedin
Article topics
Email Sign Up
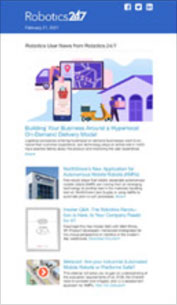
