The process begins in the assembly area, where the packaging operator monitors the output at the full pallet pick up locations (1). When pallet loads of finished goods are ready for pickup, the operator presses a call button at the station.
When that happens, the automatic guided vehicle (AGV) software dispatches an AGV to the production line. While the AGV follows magnetic tape, the AGV reads RFID tags located along the guidepath route (2) so the software can track its progress.
The AGV can go to three different lines for full pallet pickup (1). If empty pallets are needed, it goes first to a pallet hopper (3), where empties are automatically loaded onto the conveyor top cart. Once in the production facility, empty pallets are automatically delivered to an empty pallet drop-off location (4). The AGV then moves to one of the pickup location (1), where a powered conveyor moves a unit load onto a specially designed cart. Each AGV cart can carry two pallets up to 63 inches long, or one larger pallet for over-size items. From there, the AGV travels into the finished goods warehouse (5) where the unit loads are transferred onto pallet accumulation conveyor at pallet drop-off locations (6).
Once the delivery is complete, the AGV travels to an auto-charging area (7) for an opportunity charge until it is called again for service.
About the Author

Follow Robotics 24/7 on Linkedin
Article topics
Email Sign Up
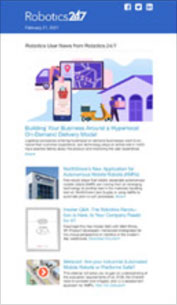
