The Robotics and Biology Laboratory (RBO) at the Technische Universität Berlin won the first Amazon Picking Challenge last week, marking a milestone in the development of commercially viable automated piece picking in unstructured environments.
The centerpiece of the record-attendance IEEE Conference on Robotics & Automation in Seattle, the challenge was created to help develop a robotic system that autonomously grasps several objects from a shelf. The scenario recreates the process that occurs in an Amazon warehouse when a client buys one or more products. Currently these tasks are supported by robotic shelves which move around autonomously within the warehouse.
Entries included robotic arms from ABB, Fanuc, Rethink Robotics, Universal Robots, Willow Garage,and Yaskawa-Motoman, using a variety of grippers, hands, suction and scoops. The RBO team used Barrett Technology’s WAM arm to finish in 1st place with 148 points. The Massachusetts Institute of Technology, using an ABB arm and a gripper with creative finger geometries, finished in 2nd place with 88 points. The 3rd place finisher came in at 35 points. Among the other participants were top universities like UC Berkeley and Georgia Tech, as well as many robotics companies.
“This has been a fantastic team effort,” said professor Oliver Brock of TU-Berlin. “Every single member of our team contributed with enthusiasm and ingenuity, enabling us to produce a compelling showcase for mobile manipulation as a winning approach to industrial manipulation.”
The two-day competition challenged entrants to build robot hardware and software that can attempt simplified versions of the general task of picking items from shelves. The robots were presented with a stationary, lightly-populated inventory shelf and were asked to pick a subset of the products and put them on a table. The challenge combined object recognition, pose recognition, grasp planning, compliant manipulation, motion planning, task planning, task execution, and error detection and recovery. The robots were scored by how many items were picked in a fixed amount of time, and participants were encouraged to share and disseminate their approach to improve future challenge results and industrial implementations.
Click here to see a video of the winner in action.
Article topics
Email Sign Up
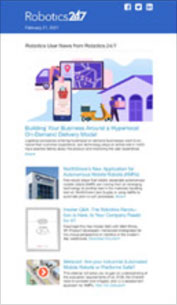