International Data Corporation (IDC) published an IDC Innovators report profiling four companies in the 3D metal printing market. IDC Innovators are companies that have introduced innovative new technologies or business models. The four companies are Desktop Metal, ExOne, Rapidia and Velo3D.
Key trends, such as manufacturers seeking manufacturing flexibility, supply chain efficiency, lightweighting and part consolidation are making the 3D metal printer market one of the fastest-growing segments of the 3D printing business. From the supply side, new 3D metal printing technologies are reducing costs while providing greater quality and production speeds than have been available in the past.
“The 3D metal printing market is seeing dynamic growth, and a key part of that growth is the development of new technologies and materials. These new products are creating new capabilities that enable a wider set of manufacturers to adopt 3D metal printing,” says Tim Greene, research director, 3D printing. “But it's not just adoption, the lower costs, better quality, and faster production are also allowing wider utilization within the companies that use 3D metal printers, up to and including the production of end-use parts.”
The report, IDC Innovators: 3D Metal Printers 2020 (IDC #US46160820), profiles four companies that are expected to have an impact on the 3D metal printing market due to their innovative new technologies and groundbreaking business models.
Desktop Metal was recognized for its Shop System, a new binder-jetting based 3D printer that is more productive and less expensive than powder-bed fusion 3D printers, that should enable digital transformation in job shops.
ExOne was recognized was recognized for the combined launch of the X1 160 metal binder jetting system, its patented Triple ACT technology, and a new clean-burning metal binder that will enable future binder jet 3D printing of premium metals such as Inconel 718, titanium and aluminum.
Rapidia was recognized for its “office friendly” water-based 3D metal printing technology. Its two-step process accelerates turnaround times while its water-based metal and ceramic pastes help to reduce costs.
Velo3D has developed a process that enables the production of “impossible” geometries. Velo3D is best known for its ability to build low-angle geometries without support structures, which reduces materials and labor cost and accelerates production cycles.
Sources: Press materials received from the company and additional information gleaned from the company’s website.
About the Author
Press releases may be sent to them via [email protected]. Follow Robotics 24/7 on Facebook
Follow Robotics 24/7 on Linkedin
Article topics
Email Sign Up
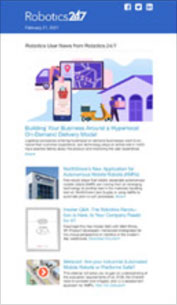