Your next cup of coffee could be in part thanks to robots. ForwardX Technology Co. last week said that it has collaborated with DHL Supply Chain to deploy assisted picking systems in a flagship warehouse that provides daily replenishment for about 600 chain coffee shops in a single city.
“By leveraging our solution, the DHL warehouse has empowered itself with the steadfast ability to expand in capacity and elasticity, a formidable force prepared to conquer the challenges of a rapidly expanding business,” stated ForwardX Robotics.
Founded in 2016, ForwardX said it has more than 250 employees from leading universities and enterprises around the world. The Beijing-based company has over 350 patents and has developed vision-guided autonomous mobile robots (AMRs) and fleet management software to automate materials handling in warehouses and factories.
With offices in San Diego and Phoenix, as well as in Japan, Korea, and China, ForwardX said it has deployed more than 3,000 AMRs in over 220 facilities.
DHL experiences rapidly growing demand
DHL Supply Chain is part of DHL Group, which claimed it is the world's leading logistics provider. The Bonn, Germany-based company said it combines management and value-added services with integrated systems to drive resilience, efficiency, and quality improvements and create competitive advantage.
DHL said the number of stores supported by its warehouse has doubled from 300 to 600 in just one year. Peak shipment volume has reached 400 cubic meters (14,125.9 cu. ft.), it said.
The coffee chain anticipates high growth this year, and DHL projected that its warehouse will have to support an expansion to about 1,000 stores. This will pose challenges, including an increased workload for picking personnel, difficulties in recruiting new workers, and high training costs, it said.
ForwardX Flex 300-S AMRs yield results
To address its warehouse challenges, DHL implemented ForwardX Flex 300-S AMRs. Within just two months, it reported a 100% increase in units picked per hour (UPH) and 30% savings in operational costs.
These results demonstrated the assisted picking system's accuracy, reliability, and ability to reduce costly mistakes, said ForwardX. The company said its AMRs use advanced sensor fusion technology and computer vision cameras for perception.
This combination provides a comprehensive view of the environment, enhancing perception capabilities and reducing blind spots, claimed ForwardX. It also ensures safe navigation and minimizes the risk of collisions, the company said.
Case-picking operations can be made even more efficient and safe when the AMRs are integrated with ForwardX's assisted case-picking system and use a batch picking method, it said.
Safety before autonomy
ForwardX acknowledged that manual lift carts and forklifts are still “indispensable” for warehouses needing to pick cases of small and medium-sized items. “Ensuring safe collaboration between humans and machines is of utmost significance in such settings,” said the company.
It also noted that not all AMRs work seamlessly alongside lift trucks. The sensors of laser-based AMRs are often positioned in a way that may create blind spots near the ground, since they rely on horizontal beams and have limited detection angles, said ForwardX.
Placing laser sensors above a forklift's fork can lead to a higher risk of collisions and safety incidents, especially when dealing with heavier payloads, it added, touting its vision-based guidance.
ForwardX asserted that its deployment with DHL demonstrated how its systems can enhance productivity, reduce picking errors, and save costs.
Article topics
Email Sign Up
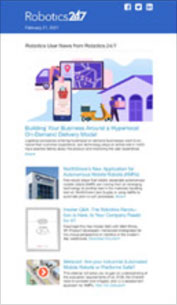
