Carhartt & DHL Supply Chain
Canal Winchester (Columbus), Ohio
Square Footage: 556,000 square feet
Products Handled: Women’s apparel and accessories such as gloves, hats and belts
SKUS: More than 40,000 SKUs, of which 11,000 SKUs are managed in Canal Winchester
Througput: Between 25,000 to more than 100,000 units in a 24-hour period depending on the season.
Shifts: Two 10- to 12-hour shifts, 7 days per week with the exception of Saturday night
Read the full feature article on the Carhartt - DHL Supply Chain collaboration here.
In a facility in Canal Winchester, Ohio, one of several facilities DHL Supply Chain operates in Columbus for Carhartt, autonomous mobile robots (AMRs) have transformed an otherwise manual operation. The success of the project at that location has set the stage for the implementation of robotics and other automation technologies at other Carhartt facilities.
Receiving
Close to 70% of incoming merchandise is floor loaded in shipping containers; the remainder is palletized. Floor loaded cartons are unloaded manually, sorted and received into the warehouse management system (WMS). If there are fewer than 15 cartons of a SKU, they are added to a mixed SKU pallet. If there are more than 15 cartons of a SKU, they are palletized as a single SKU pallet. The remaining merchandise is received on pallets.
Putaway
Although this is the exception and not the rule, if there is immediate demand for a full or mixed SKU pallet, it will be delivered to replenish a picking location.
Otherwise, mixed SKU pallets are scanned into a storage location in a very narrow aisle (VNA) storage area. Full pallets are scanned into a storage location in the single deep pallet rack area. The fastest moving SKUs are stored at the pallet level in a bulk floor storage area for easy access.
Order fulfillment and picking
The facility manages e-commerce, wholesale and retail orders. As such, there three picking processes for item picking, case picking and full pallet picking.
Orders are waved by the WMS by channel and by priority.
E-commerce orders
E-commerce orders are picked from case flow rack to autonomous mobile robots. The robots have been modified to handle multiple totes. Single item orders are batch picked; once all of the totes have been picked, the robot delivers them to the packout area.
Multi-line orders are cluster picked, with a robot capable of handling four to eight orders. When the orders have been picked complete, the totes are delivered to the packout area.
Wholesale and retail
Wholesale and retail orders may consist of a full case, a mixed case or, in rare cases, a full pallet. Full pallets are picked from reserve storage and if they don’t require any further services, they are delivered to shipping.
Mixed cases are picked directly to the outbound carton using the AMRs. Full cases are picked from the VNA, from pallets in the single deep pallet storage area or from the floor picking area. Once orders have been picked, they are delivered to a value-added services area for tags, hangers or other services required by the customer. Once all of the services are complete, cartons are pushed down a manual conveyor to shipping where they are palletized for an LTL order, or placed in a Gaylord for parcel shipping.
System suppliers
- SYSTEM DESIGN & INTEGRATION: DHL Supply Chain
- AUTONOMOUS MOBILE ROBOTS & ROBOTIC EXECUTION SYSTEM: Locus Robotics
- WAREHOUSE MANAGEMENT SYSTEM: Manhattan Associates
- BAR CODE SCANNING AND MOBILE COMPUTING: Zebra Technologies (Motorola)
About the Author

Follow Robotics 24/7 on Linkedin
Article topics
Email Sign Up
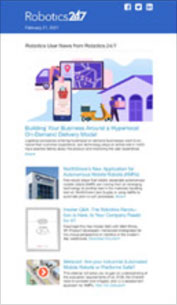
