“When Locus Robotics started, getting 10 robots to work together on the floor - work well together - was a big, big challenge. Now, we have customers running nearly 1,000 robots over a million square feet.”
Neil Bentley, senior director of product management at Locus Robotics, succinctly described the history of the Wilmington, Mass. company. Locus recently surpassed the 3 billion pick mark across its deployments, a major milestone and one that grew from 2 billion to 3 billion item picks in just over eight months.
The chicken or the egg?
As Locus received funding and developed its offerings, the question of whether it was a software or hardware company came to the forefront. Locus’ Origin and Vector AMRs represent its physical entities, while the LocusOne warehouse automation system and the new LocusHub AI-enabled business intelligence engine make up the software side of its roster.
“In terms of where we started, it's interesting because our heritage as a warehouse operator is really where our roots begin,” said Kary Zate, senior director of marketing communications at Locus. “One of the things that the original founders of the company focused on was using the data for forecasting, planning and looking forward. Even long before we had this notion of, ‘How do we capture this data,’ we had been looking at that data.”
In terms of looking forward, with Locus’ robotics-as-a-service (RaaS) business model, the chicken or the egg conundrum spearheaded development between the hardware and software sides of the company. However, it never became a what’s going to come first conversation.
“It really is hand-in-hand,” Zate said. “As far as the company’s concerned, the data was something that helped drive not only operations, but design too.”
Locus’ team has a wide background in warehouse and supply chain spaces. The resulting design of hardware and software for the company’s products now plays a key role in these operations, along with managing the volatility of day-to-day operations in these industries.
“There's still so much that's variable in warehouses,” said Kait Peterson, vice president of product marketing at Locus Robotics. “Every day is unpredictable in warehousing and supply chain. The biggest challenge with things like automating every single decision process with robotics and AI is that supply chain is just too unpredictable. People are really good at understanding the nuances and the unique challenges of their own operation.”
Decision engine vs. recommendation engine
Artificial intelligence and machine learning are everywhere, and Locus is no stranger to these technologies. Locus utilizes advanced analytics, AI and machine learning to provide predictive insights to warehouse managers on how they can maximize productivity, optimize workflows and ultimately, generate more ROI.
One key element of the platform is that LocusHub provides insights to human operators by suggesting optimal processes for their operation. It doesn’t automatically move robots and staff around.
“We'll continue to add additional capabilities, additional AI, additional learning that will enhance that decision support and decision-making capabilities so we can start to make stronger recommendations. But at the end of the day, people are still needed, the expertise of humans is still needed,” Peterson said.
“At the very highest level, humans make the decisions,” Bentley added. “We're giving them data to help them make what we think is the best decision at the time. We're also able to then go back and look at our recommendations versus how things were executed and make our recommendations better over time as well.”
How about the robots and the software in use?
Saddle Creek Logistics’ deployment
In 2020, Saddle Creek Logistics Services was in need of a more efficient way to provide ecommerce services for a Texas-based client. The resulting deployment of 20 Origin AMRs began a relationship between the company and Locus that still runs to this day across multiple Saddle Creek customers.
In 2022, Saddle Creek deployed 30 Origin and eight Vector AMRs in its Kentucky warehouse. And since the release of LocusHub in early 2024, the company has utilized the business intelligence engine to get a better understanding of the data from each robot.
“I think that the easiest way to describe it is we’re now able to speak with data and lead with data,” said Jeremy Moore, senior director of fulfillment operations at Saddle Creek. “It has really improved our visibility and helped us to identify actionable trends.”
As Moore, along with his warehouse managers and associates, have grown more comfortable with the LocusHub platform, they’re also generating more useful data to be used in fun ways - such as associate picking competitions - and in conversations with Saddle Creek customers.
“I think it gives us the ability to put data on paper,” Moore said. “I think boots on the ground, when customers are here, they're seeing the impact of Locus and they're seeing the impact that it has on their operation and how fast it's pushing their operation through. It's not just a conversation in a business review. It's not just a conversation that we have on the phone. When they're here you can see the robots and how it’s pushing out products as well.”
“Saddle Creek has a mixed fleet of our Origin and Vector LocusBots,” Zate added. “LocusHub helps them manage the two fleets based on the use cases that are necessary for those particular missions. It gives Saddle Creek the ability to say ‘We've got the right bot for the role’ and move that robot around, plus the right amount of people who are working in those particular sections.
Making good use of all the data for future improvements
The entire robotics industry, along with its deployments in various sectors around the world, is constantly evolving. LocusOne and LocusHub are no different. As Peterson notes, updates and new features can be rolled out at any time with continual deliveries. When Locus develops new features, they can be delivered to customers right away.
Another rollout on the horizon for Locus involves more flexibility with workflows and robot designation.
“We have customers that their workflow within a day or day-to-day might change substantially,” Bentley added. “They might have a whole bunch of restocking in the morning, a whole bunch of picking in the afternoon. They might have days which are heavy for retail picking and other days heavy for ecommerce picking. So this new mass reassignment capability allows them to see all the work that's in the system and that's been passed to Locus, allow them, based on that, to make decisions on changing what the robots' run modes are or other elements of what the robot has been assigned to do.”
At Saddle Creek, Moore mentioned always asking ‘Can I have more data?’ Specifically, trend data to help him and his colleagues decipher heat zones and patterns over periods of time.
“How can we see the trends and how can we see the learnings,” Moore said. “How can we track that day-over-day, week-over-week, month-over-month and year-over-year? And how can we get that quick view that says ‘Here's the progress that you’re making.”
One new feature, called “Glide Path” was rolled out by Locus to examine exactly that. Glide Path predicts when work will be completed based on the trend from the day so far, and the preceding days. The feature gives operators a way to see, at a glance, whether they are on target for the day based on work volume.
The relationship between Locus and its customers continues to spur development, echoing the creation of LocusHub.
“We had all this data,” Bentley said. “We were delivering part of it and some insights through our legacy dashboarding, legacy reports through our customer success organization. But we knew we could do more with new technology like machine learning and AI. LocusHub at its simplest, just took several different touchpoints between the customer and the Locus solution and consolidated them. We also re-architected them so that we can make use of machine learning and AI and make things better and more efficiently in the future.”
Want to learn more about fleet management? This article was featured in the June 2024 Robotics 24/7 Special Focus Issue titled “Orchestrating mobile robot fleets for success.”
About the Author
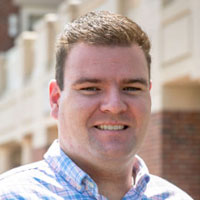
Follow Robotics 24/7 on Linkedin
Article topics
Email Sign Up
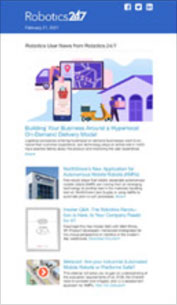
