Setting the Strategy
Ferrari is known around the globe for high performance automobiles, and its customers demand and expect the absolute best in customer responsiveness and service.
Faced with increased demands from new markets such as China and the Middle East - where customers are much less willing to wait the standard 12 months for their prized delivery - Ferrari realized that it had to increase production rates in terms of both quantity and speed to meet growing output demand, without compromising on quality.
This presented a profound challenge because each Ferrari is unique. Every customer has the luxury of customizing and tailoring their new purchase, from unique paint colors to the materials that cover the seats and interior, as well as many other personalized details on each car. The result is that no two Ferrari cars are the same. Each buyer has a unique vehicle.
This led Ferrari to realize that it needed a very responsive and flexible manufacturing setup, supported by agile business software that could help the company achieve its targets for new production output.
Ferrari’s owner, FIAT, has a centralized IT policy that specifies that group companies should standardize on SAP to run the business. But, faced with the challenges of delivering faster production in order to capture market share in fast-growing economies, Ferrari quickly proved why it should not adopt such a solution. SAP was not going to deliver what was demanded by the company in terms of coverage of past developments and the business model to be implemented through the ERP.
Infor helps Ferrari Report Sizable Production Increases
Infor has helped Ferrari achieve substantial production growth using Infor LN and Infor ION. Ferrari leveraged its ERP upgrade to Infor LN to meet a growing global demand and increases in production quantity without compromising on quality.
Infor provides Ferrari with the unique capability to build 7,000 individual custom-configured vehicles a year in sequence while maintaining high operating line efficiencies and full sequencing with the supply chain. Ferrari is confident that the speed of transition from Baan to LN will contribute a significant rise in annual production volumes expected especially on the engine production side.
What Makes Infor LN & ION Tick?
The top 10 things you should know - Ten questions and answers
Download the White Paper(s): What Makes Infor’s Intelligent Open Network Tick?
Getting Business Specific
Faced with this demand for speed and agility in its production processes, Ferrari undertook an extensive review of its processes and identified a range of targeted improvements.
After assessing both customization and manufacturing speed demands, combined with the need to maintain the quality that is a hallmark of the Ferrari brand, senior management decided to update its existing ERP (Baan IV) software to the latest version of Infor™ LN. The project has been split into phases covering the industrial (sports car manufacturing), finance and control, spare parts, and Grand Prix (Formula 1) divisions.
Infor LN is well suited to the organizational and operational model of Ferrari, since it provides flexibility and automotive industry-specific functionality. It can handle the complexity of an infinite number of customizations, without compromising on either speed of information delivery or finished product quality.
Infor LN has the unique ability to build individual, custom configured vehicles in sequence, yet maintain high operating line efficiencies and full sequencing with the supply chain.
Other ERP solutions rely on multiple external sequencing and MES systems, which increase complexity, risk, errors, and cost.
Senior management at Ferrari places a heavy focus on the supply chain and manufacturing operations because both are of vital importance to the day-today and strategic focus of the organization. Ferrari has introduced new supply chain processes with the target of “zero shortages” along the production line - that is to say, no parts missing at any point of the production chain, eliminating the unacceptable delay such a shortage would cause.
From a supply chain perspective, this included outsourcing the material handling/warehouse management to an external third-party logistics provider.
As part of the manufacturing aspect of this strategy, Ferrari created a production grid, which takes into account all of the possible combinations of customization elements. The grid enables Ferrari to have all the right components ready and in the right place at the right time. Cars can then be produced quickly and with precision, to the exact requirements of customers, while still making use of the time and efficiency savings of automated processes.
As a result, Infor LN is used widely across Ferrari, from manufacturing and the supply chain, to taking the orders coming from its commercial network worldwide, and providing the finished cars to customers.
This demands a very tight connection between the supply chain and manufacturing technology, driven by a focus on the planned increase in production numbers. This communication has been facilitated by Infor ION, Infor’s own Intelligent Open Network, which provides connectivity between Infor and non-Infor applications.
This has led to integrated business processes, such as order configuration, advanced planning and scheduling, assembly line scheduling and sequencing, and supplier management, increasing control over the Ferrari supply chain and asset maintenance and management. As an example of this control, Ferrari can now freeze engineering changes at the sub-line level, while still making changes to the overall bill of materials.
Doing Business Better
The first phase of supply chain changes has marked a major development at Ferrari. IT now works hand-in-hand with new physical manufacturing technology, since the new setup went live in June 2012. Infor LN currently improves processes and the efficiency of the logistics supply chain at all stages of manufacturing.
The transition from Baan to Infor LN, supplemented by integration to third-party solutions, in-house applications, and Infor ION, was delivered in a fraction of the time, compared to the timescale proposed by other vendors. Ferrari is confident that this transition will contribute toward a significant rise in annual production volumes expected, especially on the engine production side.
A second relevant step was just implemented at the end of 2012. This included the application of a new concept for the supply chain management and manufacturing management of a “new turbo engine production” (including integration with the Siemens MES system used for shop floor control).
The implementation was successfully executed for the V8/V12 engine family in December 2012, and was rolled-out in February 2013 for the V6 engines.
Looking forward, Ferrari will continue to exploit the world-class advanced planning and scheduling, enterprise asset management, assembly line management, and supply chain management capabilities within Infor LN. The extra capacity that has been realized by the use of Infor LN will also enable Ferrari to make engines for other members of the FIAT group, such as Maserati.
Vittorio Boero, chief information officer, Ferrari, explains: “We are much happier with our new IT infrastructure. As well as improving flexibility, we have reduced the number of anomalies in the system, which is streamlining the production process further. It has also been a useful experience for us to make these changes and an opportunity to improve the knowledge all our staff has of our internal processes. With the change encompassing both physical production and the IT supporting it, as well as processes originating at the dealerships, we have been able to establish better relationships between many business departments and IT.
“Among the lessons we have learned, it was the right decision to begin with a careful analysis of our existing processes, identifying the specific weak points and how they could best be tackled. We are also focused on benchmarking, so that we know we have a system that delivers some of the best manufacturing processes used by high-end car manufacturers.
This approach will be also replicated in the next waves planned for the completion of the ERP implementation. “By having a great relationship, supported by close communication with Infor, we have been able to make all the changes we needed efficiently. As we proceed to the next phases of the program, we believe we have the right ways of working to continue to be highly effective.”
S&OP Set to Help Drive 40% Improvement in Supply Chain Performance
Ferrari will also be investing in Infor Sales and Operations Planning (S&OP). The S&OP will be abolishing the age-old legacy systems and spreadsheet-based processes of erstwhile ERP LN contract, to make way for a faster and more precise supply chain planning process.
The contract will help Ferrari to make use of automated workflows of Infor’s S&OP, in order to maintain a constant flow of information between demand from the market/dealer and supply from the automaker’s manufacturing plant.
This in turn, will improve the accuracy, planning and flow of data within the company. In addition to it, Ferrari can also track and alter the changes, taking in the factors of demand from dealer and supply from its production plant into consideration. This effectively will reduce the time taken by company to meet the customer demand by a substantial degree.
News: Infor to Acquire GT Nexus
Article topics
Email Sign Up
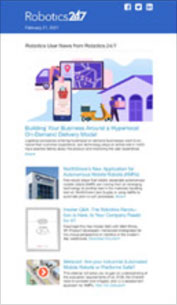
