To explain the advantages of using ResinDek® flooring panels on elevated surfaces traveled by robotic automation, a new video has been released by Cornerstone Specialty Wood Products, LLC®.
The video details how concrete flooring on mezzanines, industrial work platforms, and pick modules can negatively impact the functioning of AMRs and AGVS.
Scott McGill, Director of Sales for Cornerstone:
“Concrete often has worn and uneven surfaces that disrupt the functioning of laser-based navigation systems, or cracks and spalling that lead to wear and tear on robot wheels and hardware. Further, concrete floors tend to not be level. Because most robots are not equipped with a braking system, an un-level floor can cause a robot system to roll away from its target point, requiring unscheduled downtime and manual intervention to get it back in its proper position.”
McGill continues:
“Conversely, applications utilizing ResinDek flooring panels specified with either the TriGard or MetaGard finish ensures optimal AMR and AGV performance. Both finishes have been extensively tested with robotics for coefficient of friction, surface roughness, wear resistance, and light reflectivity, in accordance with ANSI standards, as well as unique application specifications.”
TriGard coating technology
TriGard® is a proprietary finish developed and engineered specifically to endure the consistent, repeated travel patterns associated with AGV and AMR robotic traffic and is designed to withstand 10 years of high-frequency repeat traffic.
The TriGard finish comes standard with electrostatic dissipative (ESD) finish that protects electronic equipment from damage and complies with ANSI/ESD Association specifications.
MetaGard steel surface
MetaGard® is engineered for extreme wear. In testing, ResinDek with MetaGard has been shown to be 5x more abrasion resistant than concrete in heavily trafficked areas where dirt and debris are not routinely removed, such as 24/7 operations that may be quarantined from employees.
ResinDek with MetaGard has been proven to withstand more than 2 million annual pivoting passes generated when AGVs change direction.

To create a cost-efficient flooring solution for robotic applications it is recommended to use a combination of ResinDek with MetaGard in the higher traffic, debris-laden areas and ResinDek with TriGard in the cleaner, lower traffic regions or where debris is not an issue.
Aligning the proper finish with the demands on the floor will maximize the performance of the platform while decreasing the overall cost of the robotics flooring system.
Further, ResinDek flooring panels can be customized for load capacities, required finish type, and volume of robotic traffic. ResinDek composite engineered flooring panels have the proven structural integrity to support dynamic and static pallet jack limits from 2,000 – 8,000 lbs and the rigorous demands of robotic traffic such as AGVs and AMRs.
ResinDek panels are backed by comprehensive design engineering services and a 10-year product warranty.
Cornerstone Specialty Wood Products, LLC
Cornerstone Specialty Wood Products, LLC, has been at the forefront of testing and innovating flooring panels for the Material Handling Industry since 1994. In 2007, Cornerstone began providing ResinDek® panels for robotic applications. Much of Cornerstone’rsquo;s initial research and development occurred with AGVs.
In the last decade, they have provided a variety of ResinDek flooring products to numerous Automated Guided Vehicles (AGV) and Autonomous Mobile Robots (AMR) manufacturers for their testing labs. As a result, millions of square feet of ResinDek panels are in service worldwide with robotic traffic in distribution centers, warehouses, and retail environments.
Article topics
Email Sign Up
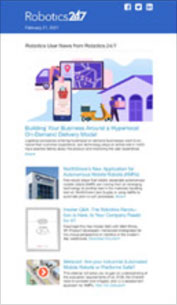
