Turbulent times are, perhaps, the greatest catalyst for technological change and growth. Simulation for design has taken center stage during the pandemic to aid engineers, workers and public health officials as they solve problems and strive to be best prepared to combat the spread of COVID-19.
Design and simulation software is in the spotlight more than ever, as it’s an instrumental way to create solutions and help many overcome obstacles, problems and challenges that have arisen due to the coronavirus and all that goes with it.
“Engineering simulation software technology has been able to address critical issues at the personal, societal and business levels. Engineering simulation software is being used in a variety of ways as part of the pandemic, used to model both the protection of the general public as well as patient treatments,” says Marc Horner, senior principal engineer, health care, Ansys.
The utility of engineering software and modeling has flexed its muscles best during the pandemic, providing data and information to public health officials in an unprecedented way. Simulation technology is applicable to health issues and to influencing better decisions and pathways to best practices and behaviors.
Horner says that from a public health perspective, engineering simulation software has helped establish the underlying reasons for following the recommended best practices for social distancing and wearing of personal protective equipment (PPEs).
“Computational fluid dynamics simulations of breathing, sneezing and coughing clearly illustrated how the droplets that leave our mouth can travel long distances before falling to the ground,” notes Horner. “We are not able to see aerosol particles with the naked eye; therefore, these simulations were quite valuable when establishing the need for complying with WHO (and other health agency) recommendations.”
Another public safety concern Horner addresses is virus transmission via contaminated surfaces in public spaces, such as airplanes or hospital rooms.
“Proper cleaning and disinfection are required because the virus can live on surfaces for an extended period of time,” he adds. “This resulted in significant interest in designing automated UV-C light systems that could rapidly and efficiently decontaminate exposed surfaces, allowing for that airplane, train or hospital room to be returned to service as quickly as possible. In this case, light simulation modeling using Ansys SPEOS helps to ensure sufficient doses of UV light are delivered to deactivate virus particles on surfaces.”
Regarding the dangers of the pandemic, simulation is presenting a new venue to mitigate, control and aid the population who is so vulnerable to its danger.
Paweł Chadzynski, senior director of product marketing at Aras, says simulation allows us to explore and probe various medical and behavioral approaches to mitigate, control and help resolve the pandemic.
“Much of the investigation and prediction around the nature and spread of a virus can be conducted safely using validated scientific numerical methods and physics-based simulations,” advises Chadzynski. “While the process for developing a vaccine requires human clinical trials towards the end, the path to the trials does not. This is a role for simulation technology and the pandemic simply highlighted the importance of it.”
Chadzynski says that while simulations approximate reality, they also provide a sense of direction.
“The approximation aspect opens the door to questioning the predictions,” he says. “The direction aspect opens the door to overplaying the potential risks. These often create tension between scientists and politicians, and that is exactly what is at play when simulation is used to mitigate, control and help resolve the pandemic. The process becomes confusing to all when used in support of conflicting objectives, as in the case of the current situation. This is not a problem of technology but rather a question of what role technology should have in making fundamental life-and-death decisions.”
From simulation to finished product
The role of technology in such decisions has made its way into many products, devices and objects that help keep people safe. Safety is a primary goal at organizations as well as communities everywhere throughout the world. Simulation and designs that are rapidly transformed through fabrication into useful forms and objects is a key benefit they provide.
“Employees’ health and safety were the number one goal at most organizations,” says Gurvinder Singh, global product director for injection molding for Protolabs. “Engineers were forced to figure out a way to collaborate, design and bring products to market while social distancing and in most cases working remotely from home.”
Singh adds that what further complicated things was that supply chains were completely disrupted, impacting sourcing and distribution logistics; engineers had to figure out which suppliers were agile and reliable to deliver during those uncertain times.
“The pandemic was growing at an exponential pace so speed to market was the number one objective of the engineers and executives stepping up to respond to the virus,” says Singh. “Engineers didn’t have the time to iterate. They need to get designs right the first time and required partners that would help them get there.”
Singh explains that the impetus of Protolabs is built on speed, agility and flexibility. By using on-demand tools, engineers could order a range of COVID-related components, such as testing kits, PPE, ventilators and cleaning/sanitizing solutions. Suppliers were required to be onshore due to the uncertainty of overseas suppliers. Additionally, they had to be vertically integrated to ensure transparency and fit Protolabs’ requirements.
“We have tools that virtually manufacture the part to create a digital twin as part of the quoting process,” notes Singh. “This ensures that we clearly communicate exactly what the customer will receive if they order. This digital process saves time and production costs, and improves part quality before the actual production begins. These tools helped the engineers get their part right the first time.”
Bringing products that are in short, as well as large, supply is a key benefit of producing via 3D printing nowadays. Labs now make things with locally sourced materials in record time, and it’s making a difference.
“There is a desperate need for low-cost hardware to deal with COVID-19 all over the world,” says Joshua Pearce, a professor of materials science and engineering at Michigan Technological University.
“Today, with the evolution of digital manufacturing technologies such as 3D printers and circuit milling systems, humanity can share designs with others who can then replicate medical-grade devices for the cost of locally sourced materials,” Pearce says.
Pearce adds that the pandemic “has taught us that massive distributed manufacturing is possible by sharing open-source designs. This is most clear with the success of PPE manufacturing. Next time we will be ready with far more sophisticated digital designs.”
Using simulation to create reality
Outside of the design aspect, the use of virtual reality and environment simulation for training humans is another useful application of simulation. Its primary advantage, relevant to a pandemic environment, is that it may be used effectively, mostly without human contact or being near others.
“The pandemic has brought safety to the forefront for most corporations,” says Doug Donovan, CEO and co-founder of Interplay Learning. “As such, our firm, Interplay Learning, has seen a surge during the pandemic in the implementation of our online training for the skilled trades with our digital experiential learning platform. This means we create an immersive learning environment online that simulates in-person learning utilizing 3D simulations and virtual reality, while keeping our users safer and socially distanced.”
Donovan adds that their customers leverage a virtual platform to train new techs, refresh experienced techs or assess technical skills to hire an individual in a job. This is all done online, virtually. Donovan points out that the days of in-person classroom learning are becoming unnecessary with technology using 3D simulation and virtual reality.
“We hope this will keep our customers safer, while still enabling them to train to be job-ready,” he says.
Balancing simulation and digital design
But the introduction and embrace of simulation and digital design must be met with careful balance with the way we’ve always done business, and what we can do now. The results that design and simulations provide must fit and apply where and when needed.
“The adoption of digital technologies has varied greatly across industries and company sizes,” says Singh. He believes traditional organizations have been struggling to find a balance between existing operations and digital transformation of the entire value chain.
With digital design and simulation, more tools allow organizations to create products and build practices that represent the agility needed to meet the demands of a world that fears havoc.
Underlying a product’s design and simulation, or even a practice, is a flexible, speedy means of problem-solving. These approaches help organizations do things such as reduce risks to the supply chain, accelerate the speed and timing that goods and solutions meet markets and reduce product cost, which makes it easier for products to reach the users that need them.
“We believe technology is going to play a key role in helping us rethink manufacturing in the U.S. to reduce supply chain risks and cost while improving agility, speed to market and transparency,” says Singh. “We are sitting at an inflection point where thanks to Moore’s law, computing and storage are accessible at minimal cost. Additionally, we continue to make leaps in automation and artificial intelligence that will help us navigate cost in the region.”
About the Author
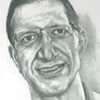
Follow Robotics 24/7 on Linkedin
Article topics
Email Sign Up
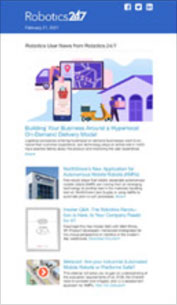
