Denmark-based Danfoss Power Solutions is a multinational company with more than 71 factories in 20 countries and $7 billion in revenue. Its North American headquarters in Ames, Iowa, has 200,000 sq. ft. of production space, along with office space and 1,000 employees.
As a manufacturer of hydraulics for the construction, agriculture, and other off-highway vehicle markets, the company’s primary materials handling requirement at its North American headquarters was the connection of its assembly lines to its fixed paint line. Danfoss had automated processes in assembly and then again at the paint line, but nothing to bridge the two islands of automation.
In the short term, Danfoss needed a safer way to provide flexibility to its supply chain and help mitigate a scarcity of labor and space. In addition, the county that encompasses Ames has a historically low unemployment rate in recent years, so finding workers is a challenge. Due to the size of some of the manufacturer’s equipment, the solution needed to have a small footprint.
On a longer-term basis, Danfoss’ five-year plan involves multiple parallel systems, so it needed a system that could lay the groundwork for future activities—without tying it to fixed automation, such as automatic guided vehicles (AGVs) or conveyors. This assessment led the company to consider autonomous mobile robots (AMRs).
Danfoss uses mobile robots for lights-out operations
Danfoss deployed two AMRs from OTTO Motors to transport large payload materials from the end of assembly to the paint lines that operate three shifts, 24/7 for lights-out engineering. The robots enabled the company’s workers to focus on high-value production tasks, improved safety, and reduced transportation waste, as robots now move products throughout the production facility.
The AMRs offer flexibility, scalability, and security through fleet management software, said Danfoss. As a plant’s layout changes over the years, a software update will ensure the AMRs continue to connect various islands of automation.
“Simple features, such as turn signals, stop zones and procedures, and regulation of speed, have made the AMRs a very visual participant for my colleagues working on the paint and assembly lines,” said Stephen Hines, manufacturing engineer at Danfoss Power Solutions’ North American headquarters.
“Without the [AMRs] in place, I’ve calculated that I would need 4.5 additional material handlers to do the work,” he added. “Even if we could find the workers, which we can’t, we wouldn’t have room for them. [OTTO] has given us the means to transform in the short-term, while creating a framework for future growth and scalability.”
Article topics
Email Sign Up
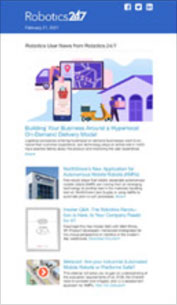
