Warehouses and distribution centers have been a hotbed for new technologies over the last few years, with everything from packing stations to picking equipment to materials handling equipment feeling the impact of these innovations. Not to be left out of the conversation, the loading dock was also ripe for improvement and, as such, is getting more intelligent and safer thanks to new hardware, software and tools.
“There’s no question that companies are realizing the significance of the dock, and the difference between uptime and downtime out on the dock,” says Walt Swietlik, director of customer relations and sales support at Rite-Hite. “Everyone is working with this ‘on-demand mentality’ that everything has to work, period. There’s just no room for failure or interruption.”
To help companies manage these demands, Swietlik says Rite-Hite introduced its smart dock concept about a year ago. At its core, the technology monitors activity from the time the trailer backs up to the loading dock until the moment it pulls away from that dock. During the interim, it tracks the time the trailer spent at the dock; how much time was spent actively loading or unloading the trailer; and how much downtime took place.
Swietlik says the value companies place on these metrics increased in 2020, with the global pandemic turning supply chains and transportation networks on end. “Especially in the past six months, a lot of customers have expressed a keen interest in learning more about these opportunities,” says Swietlik, “not only for their new buildings, but also for their existing facilities.”

Fending for itself
With OSHA reporting that about 25% of all warehouse injuries occurring on the loading dock, worker safety is an ongoing concern for all DC and fulfillment center operators. With new challenges like social distancing, contactless transactions and outbreak-related health issues added to the list, those safety concerns exacerbated further in 2020.
Mike Pilgrim, president at Systems LLC, says end-to-end dock management systems help companies rest easier, knowing that this area of their operations is as safe as it is productive. These systems incorporate vehicle restraints, dock levelers, dock doors, lights and other components that used to be installed individually and weren’t necessarily “connected.” Now, thanks to the Internet of Things (IoT) and other connectivity platforms, the “clutter of componentry around the dock door has been incorporated into a master control panel,” says Pilgrim.
This trend aligns with a broader push to streamline the fulfillment process and deploy technology that helps automate processes, improve throughput and create a safer workplace.
“There are all types of productivity tools, warehouse management systems (WMS) that exist 30 feet inside the dock area and also yard management systems (YMS) for the outside activities,” says Pilgrim. “However, that transitional area at the loading dock, and 30 feet inside the door, has basically been left to fend for itself.”
Making the grade

While some companies continue to rely on Excel spreadsheets, clipboards and verbal communications to manage their docks, others are deploying smart controls, Cloud technology, and data to streamline this area of their operations. To accommodate these needs, Systems LLC began Wi-Fi-enabled smart controllers that companies can use to manage dock operations.
“That was the catalyst behind moving the data that exists at the loading dock area into the Cloud,” says Pilgrim, “where companies can compare periods of time, individual docks and entire facilities with one another.”
Armed with these insights, warehouse operators can establish and drive new key performance indicators (KPIs), improve performance and enhance safety. By bringing these and other metrics to the forefront, dock management systems help employees easily identify which truck is at each door, how long it’s been there, and what’s taken place during that time. This, in turn, helps companies minimize detention fees and get drivers back out on the road faster—a big plus for those that have to comply with hours of service (HoS) rules.
Vendors are also coming up with new ways to integrate their dock equipment with existing materials handling equipment. Parcel Unloaders from Southworth Products Corp., for example, can be used to load a variety of containers onto conveyors and automated sortation systems. With built-in PLC controls, these unloaders provide a simplified integration with existing conveyor/sortation systems. An optional vibratory metering/anti-clumping accessory ensures that all items are fed into the system, all without the need for operator intervention.
How many trucks are we loading?
The Information Age has put a lot of data into the hands of companies that need it, but Rich Schlesinger, director of U.S. distribution at 4Front Engineered Solutions, says dock-related information needs can vary by company and industry. He says the biggest information “asks” right now include: How many trucks are we loading? How quickly are we loading them? And, how can we improve upon these metrics?
“In the past, the shipping and operations manager would know roughly how many trucks they did based off a specific day’s report,” says Schlesinger. In other words, they knew that they moved 20 total trucks in and out of the DC, but they didn’t know when this took place or how efficient those individual operations were.

Using 4Front Engineered Solutions control panels, which include HMI interfaces (versus push buttons), the same managers can break down the activity by different data points like trailer arrival times, how long they sat at the dock, and when they were released from the dock.
By putting actionable data into the hands of dock supervisors and managers, companies like 4Front Engineered Solutions are helping to shed new light on an area of the warehouse that’s been largely left up to its own devices. “We’ve seen a lot of connectivity, efficiency, automation and robotics in distribution centers and manufacturing facilities, but the dock has been largely left out of those conversations,” says Schlesinger, who sees labor shortages and less predictable transit times as two key drivers of dock technology adoption right now.
Overall technology adoption is also creating more interest in smarter, more efficient dock operations. “Everyone is used to getting information constantly about everything—from the thermostats in their homes to video clips of someone ringing their doorbells,” says Schlesinger. “For the longest time, the dock has been a blind spot when everything else has been illuminated.”
Operating in the “new normal”
In a world where contactless transactions and interactions are being favored, Schlesinger says 4Front Engineered Solutions’ 4SIGHT Connect platform includes a gate product that can be set up so drivers don’t have to get out of their vehicles when they enter the premises.
“They can do everything from inside their cabs, and not have to come into your facility or interact with your employees,” says Schlesinger. “For the near-term, that’s going to be something companies want as they strive to limit interactions.”
Looking ahead to the post-Covid world, Schlesinger expects companies to continue pushing the envelope on intelligent docks. For example, driverless yard jockeys and lift trucks will likely gain more traction as organizations work to reduce their reliance on human labor and streamline operations. With warehouse space at a premium and companies working to optimize physical footprints, more of them will need equipment and software to help achieve those goals both on the dock and within their four walls.
To accommodate these needs, Swietlik says Rite-Hite has been integrating automated controls and other technology into its dock locks, levelers and other equipment, regardless of the specific, current demand for those controls. “Whether the company is buying automation now or not, we want to make sure they’re prepared for the future,” said Swietlik, who sees this as a way of helping companies think beyond their current needs and prepare for the future.
Democratization of smart dock technology
Going forward, expect to see a democratization of smart loading dock technology as companies of all sizes strive for efficiencies in this area of their operations.
Pilgrim sees IoT as a key component in this shift in that it can effectively connect multiple different systems and then, using the Cloud, dispense the data and other information to users in a very cost-effective, manageable way.
“The technology is there for companies with five or 10 docks to be able to compete,” says Pilgrim, who tells companies investing in dock equipment in 2021 to take this into careful consideration. “Even if you’re not ready to integrate the controls and set up KPIs right now, you’re mostly likely acquiring capital equipment that will last in the facility for 20-plus years. Even if you’re not ready today, why limit yourself to just the next two decades?”
Companies mentioned in this article
About the Author
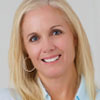
Follow Robotics 24/7 on Linkedin
About the Author
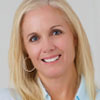
Follow Robotics 24/7 on Linkedin
Article topics
Email Sign Up
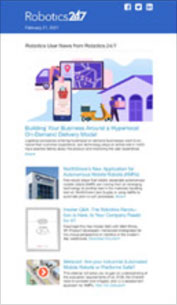
