Collaborative robots offer to help small and midsize manufacturers, among others, adopt flexible automation.
Welcome to the third article in this series on collaborative robots. We previously examined what cobots are and whether they are safer and easier to use than traditional robots.
In this post, we compare cobots to industrial robots in a range of applications and explore the pros and cons to each class.
Cobot roles compared with industrial robots
While collaborative robots are intended to be safe and easy to use, traditional industrial robots are designed to be accurate and operate at high speeds. Traditional robots are not force-limited based on contact, and some of them have payloads exceeding 1,000 kg (2,204.6 lb.).
In contrast, cobots usually have payloads in the 5 to 15 kg (11 to 33 lb.) range, with a few outliers. In addition, cobots can, with some caveats, operate near humans without guarding.
By contrast, industrial robots will always need extra guarding and safety-rated sensors to be safe. While this often makes the choice straightforward, there are other factors involved.
One advantage of some newer cobots is that the force control in the joints can be integrated into the control system. This means force-controllable cobots can be programed to carry out force-sensitive tasks without additional sensors.
An example of this would be sanding a thin composite part. In this application, it is important to control how much force is applied to avoid removing too much material and damaging the composite layers.
Another example might be assembly of parts with threaded fasteners. Traditionally, this task would require precise indexing. However, with force control, the fastener position can be adjusted until it easily threads on.
It is possible to get force control packages for traditional robots, but these usually must be placed on the robot's tool flange, adding additional bulk and cost. While not every cobot allows for force control, procuring one that does can often be a simpler and cheaper way of tackling force-sensitive processes.
Fitting robots to tasks
While it may not make sense to compare cobots and industrial robots in every individual application, most tasks in automation fall into high-level groups. The following table is general in nature and covers common application types and compares cobots and traditional industrial robots.
Application | Cobots | Traditional Robots |
Education and learning about robotics | Good fit: They reduce risk of injury, typically don't need guarding, and tend to have a shallow learning curve. | Mediocre fit: More time-consuming to learn, will require appropriate safety-rated sensors and/or guarding, higher risk of injury. |
High-speed work (e.g. case packing or pick and place) | Poor fit: Lower speed will reduce cycle time and limit the benefits of automation for high-volume products. | Good fit: These systems are designed to run at high continuous speeds. |
Very high-accuracy work (e.g. assembling micro circuit boards) | Mediocre fit: Accuracy varies with cobot models, but in general, it is harder to get very high accuracy in a cobot. | Good fit: Traditional robots are about speed, payload, and accuracy, so finding one that meets the requirements is frequently much simpler. |
High-payload work (moving heavy parts) | Not possible with cobots: As of this writing, cobots range between 3 and 35 kg (6.6 to 77.1 lb.). | Good fit: Traditional robots have payload capacities up to the weight of a car, so payload is usually not a problem. |
Force-sensitive work | Good fit: Most cobots have built-in force controls that can be integrated into the control loop without extra sensors. | Mediocre fit: Traditional robots can have force-control devices added between the tool flange and the end effector, but this is a separate unit and only gives force control at the tool. |
Processes in which the robot is working close to a human | Good fit: Safety and risk assessments must still be considered, but this is a distinguishing cobot feature. | Poor fit: Not possible without safety systems such as guarding and safety-rated switches and sensors in place. |
Explosive environment (e.g. painting) | Not possible for cobots: Currently no explosive environment-rated cobots. | Good fit: Paint robots are readily available for this application. |
This high-level table is a good place to start when considering your application, but the situation becomes more complex when there are competing constraints, such as high speed and working near humans.
Understand your problems
Unfortunately, there is no clear-cut way of solving problems in complex categories. The best approach is to clearly understand the problem and discuss it with an automation specialist who understands implementation strategies for both cobots and traditional robots. They will be able to give you a much better idea of what robot-type works best for your application, the cost, and effort involved, so you can make an informed decision.

In the next post, we will discuss how to pick a cobot. For more information, visit the Collaborative Robot Laboratory.
About the author
Cody Bressler is a senior research engineer at the Southwest Research Institute in San Antonio, Texas. This article is reposted with permission.
Article topics
Email Sign Up
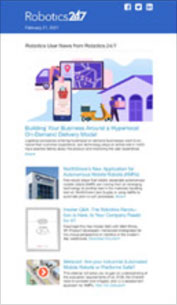
