A large North American paperboard converting plant wanted to enhance its ability to produce mixed loads to send directly to retail locations. Amid SKU growth and increased demand, the company refurbished, relocated and expanded its existing robotic unitizing system to meet present and future needs.
Installed seven years prior, the original five-aisle, robotic unitizing system used five Fanuc robots for centralized unitizing of caseloads. When the system was powered down before relocation, data reported that the robots had traveled up and down the rails the equivalent of 121,000 miles, averaging about 10 miles a day as they scanned, organized, separated and classified products into a unit load.
The original robots and rails were joined by two new robots (Motion Controls Robotics, motioncontrolsrobotics.com) in a new facility with a larger footprint and room to expand. The project added SKU positions along the rails to further increase production flexibility and throughput capacity. Vacuum cups and other wear items on each existing robot’s end-of-arm tooling were refurbished and existing conveyor was also expanded and relocated.
Existing tape inspection stations were relocated and fitted with new technology, and four new random case tapers were added to ensure tape is properly applied to the top and bottom of each case. Bar code scanners were updated with the latest technology to improve reliability and reduce cost to route cases from production to more than 100 SKU locations along the robotic unitizing lines.
“Overall, the biggest benefit from this system is reliability, which was our primary consideration when we were looking for a system,” says the assistant plant manager. “We are also excited to be using new technologies that have exceeded our original expectations in every respect.”
About the Author
Follow Robotics 24/7 on Linkedin
About the Author
Follow Robotics 24/7 on Linkedin
Article topics
Email Sign Up
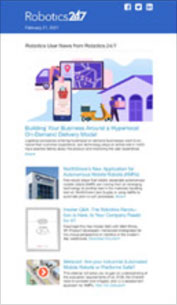