As the Coronavirus outbreak accelerates, some carmakers are exploring the option to reconfigure their supply chain and production facilities to address the serious shortage of ventilators at the hospitals.
GM, Ford, and British carmaker McLaren are among those that have expressed a desire to contribute production muscle and design expertise, as reported by ABC.
In Italy, one of the hardest hit countries, local brands Ferrari and Fiat are now in discussion with ventilator makers to see if they can boost production of the critically needed breathing apparatuses, according to New York Post.
Like these carmakers, a number of well-known fashion designers are now joining the fight against the virus. According to this BBC report, doctors and nurses may soon be strapping on surgical masks made by Yves Saint Laurent and Balenciaga.
DE editor Kenneth Wong spoke to Keith Meintjes, CIMdata Fellow and executive consultant, and Joe Barkai, independent consultant and speaker, to understand the logistical challenges and opportunities for carmakers to pull off a rapid response. The following are excerpts from their conversation, with slight edits for clarity.
(For the full unedited discussion, listen to the audio below)
Kenneth Wong: A lot of people are hoping the carmakers can address the ventilator shortage problem. I'd like to understand the challenges of reconfiguring the supply chain and assembly lines to produce a new product. Can this easily be done?
Joe Barkai: Based on what New York Governor Cuomo has said, we do not have time to reconfigure the supply chain, no time to rebuild assembly lines. We need the ventilators today. Therefore, whatever action it is, it has to leverage the existing resources, whether it is physical materials, manufacturing facilities, or human resources.
(Cuomo has said, “It does us no good if [carmakers] start to create a ventilator in three weeks, or four weeks, or five weeks. We’re looking at an apex of 14 days,” per CNBC report, March 24.)
Keith Meintjes: A vehicle is a large, heavy device, so a vehicle assembly line may not be appropriate for manufacturing something like a ventilator. In terms of a facility through the automotive supply chain, those who produce air compressors and air conditioners might be a better fit.
Wong: Can certain components in the automotive design be readily adapted for ventilators?
Barkai: Medical devices have different QA requirements; they also have certain characteristics that are not relevant to cars. Take the fan, for example. Cars have fans. Ventilators have fans. You can lubricate the fan in a car, but you cannot do that to a fan that blows air into a patient's lungs. But certainly there are parts that can be good candidates [for ventilator production]. Automotive engineers can help identify these parts. I don't think the automotive industry should be doing QA on ventilators, because the QA standards in medical equipment are different.
But we may be talking about coming together as a team, to help provide machining or use 3D printing to create parts that do not exist.
Meintjes: We have capabilities we didn't even have a few years ago. For example, using 3D printing to make tooling to build components for ventilators. You can do that to get production up and running very quickly.
Wong: How is this crisis different from the past crises?
Meintjes: The only thing comparable is the switchover of the American industries during World War II to make vehicles, weapons, ammunitions, and aircrafts. Back then, it was switching from building ordinary cars to building jeeps, for example. This, being a medical crisis, adds a different set of issues.
Barkai: The Defense Production Act allows the President to order businesses to produce things that are necessary for defense. The Act was created during the Korean War.
Wong: Manufacturing has changed a lot since Word War II or the Korean War. Right now it is pretty much a globally dispersed activity. Are we better prepared to pull off a quick response?
Meintjes: Things like internet communication plays a prominent role in the response to the Coronavirus, much more so than 20 years ago. Rapid response to competitive pressure in manufacturing is a reality, has been so for some time. If a footwear manufacturer comes out with a new design, their lead time in sales is just a month or two before others respond with similar products. We see the manufacturers' willingness to get involved—for example, Ford and GM.
Barkai: Even ten years ago, manufacturing was much more vertically integrated, so the field capabilities are relatively narrow. It used to be very local. The global phenomenon we're dealing with today, with global sourcing, gives us an opportunity. Automakers are particularly good at supply chain and logistics. They can find material sources, and they have the buying power most do not have.
About the Author
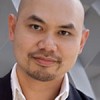
Follow Robotics 24/7 on Linkedin
Article topics
Email Sign Up
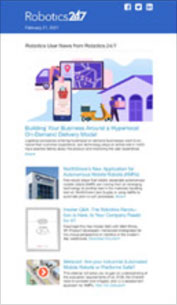
