BASF 3D Printing Solutions GmbH unveils new products for photopolymer and laser sinter printing methods. The BASF subsidiary has also established several new partnerships for the development and distribution of 3D printing solutions and products.
B3DPS has entered into a strategic partnership with the San Francisco, CA-based company Origin, for the further development of photopolymer printing processes.
“Within the framework of an open business model, we are combining BASF’s material know-how with Origin’s expertise in printer software programming and the manufacture of the corresponding hardware,” explains Volker Hammes, managing director BASF 3D Printing Solutions GmbH. The collaboration has already shown the first signs of success. Origin has developed a new printing method where BASF’s new Ultracur3D photopolymers can be processed particularly well. The technology offers an optimal combination of a good surface finish and high mechanical stability, while also allowing for high material throughput.
B3DPS is working together with Photocentric, a manufacturer of 3D printers and their corresponding software and materials, on the development of new photopolymers and large-format photopolymer printers for mass production of functional components. Based in Peterborough, UK and Phoenix, AZ, Photocentric has developed and optimized the use of LCD screens as image generators for its own printing systems. The two partners plan to offer the industry 3D printing solutions that replace parts of traditional manufacturing processes such as injection molding for small series, as well as enabling the production of large components.
The objective of the cooperation with Xunshi Technology, a Chinese printer manufacturer headquartered in Shaoxing, and operates in USA under the name Sprintray, will be opening new fields of application in 3D printing for the Ultracur3D product range of B3DPS.
B3DPS has grouped well-established and new photopolymers designed for the respective 3D printing processes under the brand name Ultracur3D. BASF has developed raw materials for its new products that enable special part properties.
“Our Ultracur3D portfolio enables us to offer customers various UV-curable materials for 3D printing that provide far better mechanical properties and higher long-term stability than most available materials,” explains András Marton, senior business development manager at B3DPS.
Expansion of Distribution Network
Innofil3D, a subsidiary of B3DPS, is entering into a partnership with Jet-Mate Technology, based in Tjanjin, China, for the distribution of plastic filaments in China. In parallel, a distribution agreement has been concluded with M. Holland in Northbrook, IL, for the distribution of filaments in the U.S. “Since the USA is the largest market for filaments, we intend to strengthen our activities there,” says Jeroen Wiggers, business director 3DP Solutions for Additive Extrusion at B3DPS, adding: “Asia is another important market for us. We will be developing further distribution channels there and putting our Ultrafuse filaments on the Asian market in 2019.”
BASF’s portfolio of filaments for 3D printing are comprised of two categories; the Innofil3D filaments based on generic polymers for conventional applications and polymer-based Ultrafuse filaments for advanced formulations used in technical applications. One of the broadest filament selections on the market, this portfolio covers customer requirements, ranging from prototype to industrial-scale production.
SLS: New 3D Printing Material
New flame-resistant Ultrasint Polyamide PA6 Black FR meets UL94 V2 fire protection standards and is a new material class for use in selective laser sintering (SLS) processes, distinguished by high stiffness and thermal stability. In cooperation with a developer of public transportation vehicles, B3DPS has developed new components that meet vehicle fire protection requirements. “Together with our partner, we are currently producing prototypes, spare parts, and small series components, and are working to further improve flame resistance to meet additional certification specifications,” explains Hammes.
BASF introduced at formnext, Ultrasint PA6 Black LM X085, which is based on polyamide 6, and can be processed at 175-185 degrees Celsius therefore making it suitable for most current SLS machines.
B3DPS Adds Polypropylene to Portfolio
Ultrasint PP is a polypropylene-based product. Ultrasint PP has plasticity, low moisture uptake, and resistance to liquids and gases. Prototypes and small batches can now be produced from the same material as used for traditional serial production. Post treatments such as thermoforming, sealing, and dyeing can be performed after printing.
Sources: Press materials received from the company.
More Info
About the Author
Press releases may be sent to them via [email protected]. Follow Robotics 24/7 on Facebook
Follow Robotics 24/7 on Linkedin
Article topics
Email Sign Up
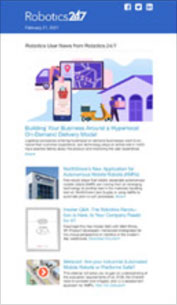