Autonomous vehicles (AVs) are moving out—slowly, it seems. They’ve been talked about for decades, as far back as the 1930s at the New York World’s Fair. In 2020, there’s been more talk about their use, potential, application and the transformation they offer to the world.
But design engineers creating autonomous vehicles must consider many factors. Operational accuracy and safety are among many critical considerations. Add to this a growing number of design tools, technologies and approaches—what’s a designer to do?
Proceed carefully while considering the tools and approaches available. But be sure to factor in all the ramifications of safety and performance as the autonomous revolution takes grip and vehicles begin to roll soon.
DataArt is a technology consultancy that designs, develops and supports unique software solutions. The company’s autonomous driving technologies are progressing, and the next autonomous driving level shift will be significant, according to Max Ivannikov, a solutions consultant at DataArt.
“It’s hard to name the exact date when it will happen, but the technology is changing our world already,” says Ivannikov. “Driverless shuttles are being tested in medical facilities, on huge campuses, at airports, for last-mile deliveries and for other purposes and places. The demand for the autonomous shuttles is constantly high, so we are about to see ecosystems emerge and regulations change around the globe. New human-machine interfaces are expected to emerge as well. There are voice assistants on the market already, and they’ll become more sophisticated. The industry is experimenting with all kinds of displays, sensor panels, rearview mirrors, cameras [and] heads-up systems. The drivers and time will decide which of them become a future standard.”
“Intelligent transportation networks are highly interconnected due to emerging communication, computing and artificial intelligence algorithms,” notes M. Hadi Amini, assistant professor in the School of Computing and Information Sciences within the College of Engineering and Computing at Florida International University in Miami. They integrate a wide range of technologies to provide affordable, equitable and reliable mobility services to the community. These technologies, however, lead to new challenges for society.
Ivannikov says vehicle data and monetization have attracted interest from analysts and original equipment manufacturers (OEMs), nudging their imagination.
“If we speak from the technological side, the industry is ready for it, the technology exists,” he explains. “But there are still a lot of talks on how to implement it best from the business point of view, and how to build a healthy ecosystem around it. So, once it happens, we will see the dramatic impact on all areas: smart parking, smart cities, insurers, gas and electric stations [and] body shops. Safety issues of the sort will always be affecting innovative projects. It’s more about us, about our lifestyles and feeling safe. We are all aware that a lot of people die in car crashes every day, yet we don’t really consider stopping using cars. Speaking of self-driving cars for enterprises as an emerging trend, I immediately think of self-driving trucks like the ones on the roads in Sweden, or Elon Musk implementing his autonomous tanker ships’ plan.”
Product Line Engineering
Whether it’s Musk or someone else rising to the top, autonomous vehicles are complex, requiring integration of many features. It is important to ensure that a ready portfolio of design tools is available to design engineers.
BigLever Software is an Austin, TX-based provider of product line engineering (PLE) tools. PLE approaches design with a portfolio of related technology tools and products and shares such assets to organize and build efficiency in how a product is created; AVs are ideal candidates for PLE due to their complexity.
BigLever uses PLE for its work with manufacturers, including leading automotive companies, to help them address the complexity, product variation and design challenges of manufacturing advanced automobiles.
“Reducing the risk of automotive defects is one of the most critical issues facing automotive manufacturers today, to protect the well-being of consumers, as well as their own reputations and financial health,” says Cathy Martin, vice president of BigLever Software. “This is especially challenging when you consider the extreme degree to which the hardware, software, systems and subsystems contained in an AV must work together, seamlessly, to replicate the actions of a human driver. Most new models on the road today have self-driving features to autonomously accelerate, brake or steer, such as adaptive cruise control, lane-centering or hands-free steering. Imagine how this complexity grows when you consider the entire automotive product family.”
Martin emphasizes feature-based PLE, stating that auto manufacturers are turning to it to influence how their product lines are engineered, produced, maintained and evolved. “PLE allows an organization to create a ‘superset’ of digital assets that are shared across the product line,” she says. “These assets are equipped with all the feature options offered in the product line. Product line features are contained in a feature catalog, which becomes the ‘single source of feature truth’ for the entire organization. The features chosen for each product are specified in a bill-of-features, which is used by the PLE product configurator to assemble and configure the digital assets to create a product instance.”
Integration of Functionalities
Incorporating all necessary features into AV design means integrating the many functionalities that apply. This is a design challenge that must not be overlooked.
“Advanced AV technology requires component innovation and integration of functionalities,” says Andreas Minatti, head of business development, automotive, at Datwyler in Germany.
“At any level, these systems require a high degree of sensor functionality, whether it be in the form of cameras, radars, lidars or lasers; how these components are secured, housed and sealed is a critical element to ensure their optimal performance. This is extremely important, as given the roles of these technologies, their reliability is directly connected to the safety of the vehicles they are embedded within, and ultimately the safety of the global road-using public,” he says.
Minatti says simulation is a key design tool for AVs and can help support the development of these essential and complex component systems.
“Consider housings for control electronics as an example,” he explains. “Such housings are often manufactured using a thermoplastic material that forms a stable shell to protect the sensitive interior from environmental influences. Another key component of the housing is the elastomeric seal. In addition to ensuring the static seal between the housing base and cover and protecting the interior, the seal or the sealing material’s elastic structure keeps electronic components in place via buffer elements.”
Advance Driver Assistance Systems
To be sure, integrating functionality is at the core of aiding an AV to safely operate with assistance. Jordi Soler Castany is vice president, global business development, electromagnetic simulation, and electronic solutions at Altair.
Castany emphasizes the importance of assistance systems in designing AVs. Assistance systems are key to the safe operation of autonomous vehicles as they are deployed for actual use.
Specifically, he cites advanced driver assistance systems (ADAS) as being key to AV design. In fact, the global ADAS market size is projected to grow from $27 billion in 2020 to $83 billion by 2030, according to a report available from MarketsandMarkets.
“One of the challenges for AVs is the design and integration of the different types of required ADAS sensors, including radars, ultrasonic, cameras and lidar,” says Castany. “These sensors are required, considering the different levels of vehicle autonomy, while we move forward to the high and full automation levels. As AVs are integrating more and different types of sensors, electrification is a key and challenging topic. Electrification comes with an increased presence of electronics, with higher voltages systems, which without a proper design can generate electromagnetic interferences [EMI]. This can cause big issues for the safe operation of the vehicle, which test car manufacturers’ and suppliers’ need to pass before being able to sell their products.”
Going Electric, Carefully
ADAS is key, and so is the drivetrain of the planned vehicle. For AVs, this means focusing on using tools, technologies and design principles for robust electric power. Electric drives enable maneuverability and the agility that AVs require to operate with diverse functional demands. There are numerous concerns in designing electrical drive systems.
“The electric powertrain consists of three main components: battery (energy storage), power electronics (conversion of electrical energy) and the electric drive (conversion of electrical energy into mechanical energy),” says Rachel Fu, technical director, R&D Strategy, SIMULIA, for Dassault Systèmes. “These three components have strong interdependencies and therefore need to be developed together; a model-based systems engineering approach is used to manage the dependencies and complexities.”
Castany adds that electromagnetic interference is another challenge for electric vehicles (EVs) and AVs that Altair’s high-frequency (HF) electromagnetic simulation (EM) solutions can address. “Testing with simulation before hardware prototypes are available, at both the component and vehicle level, helps to improve designs and to create new design guidelines and processes,” he notes.
“In an EV, range is one of the most important owner concerns,” says Ed Tate, industry process senior director, SIMULIA, for Dassault Systèmes. “Achieving high range requires both expensive batteries and an efficient vehicle. Higher vehicle efficiency allows a reduction in battery cost for the same range. Efficiency is achieved through the powertrain, reduced aerodynamic drag, more efficient tires, a lighter structure and an efficient cabin comfort system. Finding the right solution requires trade-offs between multiple teams. Engineers will need a broad understanding of multiple disciplines to effectively collaborate on these complex development programs. With access to the right tools these renaissance engineers can handle the complexity and move much faster than ever before.”
Companies like Ansys also emphasize the importance of system-level simluation in AV development via platforms like Ansys Autonomy. This level of simulation not only helps test the interaction of the various systems and disciplines involved, but also enables the simulation of millions of miles of road testing required to ensure vehicle safety. (See “Riding the Virtual Road.”)
Advancing Autonomous Collaboration
Matthew Putman is the co-founder and CEO of Nanotronics. He notes that AVs perform well. But, like so many other modern inventions, they face scaling issues.
“It is possible that this was a design problem from the start, where production and costs should have been considered from the onset,” Putman says. “But it is not too late to take the engineering advances we have seen and rethink how products are built.”
Altair’s Castany emphasizes the need for smart collaboration from many stakeholders. Different stakeholders are part of the team that gets design results. Pulling together various disciplines and using different and emergent design principles, concepts and tools is key.
“Engineers will need more expertise and teams will need to become more multidisciplinary to successfully design these vehicles,” says Castany. “No longer will engineers work in silos. Rather, they will need to pull insights from all aspects and apply them to the design of these complex vehicles.”
About the Author
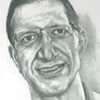
Follow Robotics 24/7 on Linkedin
Article topics
Email Sign Up
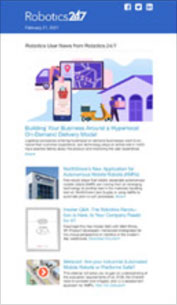
