Recent ProMat and North American materials handling shows have seen the introduction of automatic guided carts (AGCs), mobile robots and, more recently, hybrid lift trucks to the AGV portfolio. What’s more, new players have entered the market, such as Kiva Systems, RMT, Seegrid, SI Systems, INRO and Kollmorgen. Lift truck manufacturers are also getting into the game, including Toyota Material Handling USA, Crown, Mitsubishi Caterpillar Forklift America (MCFA) and The Raymond Corp.
All these new vehicles may have you wondering: Just what is an AGV? Look closer, however, and you find that each of these disparate vehicles shares something in common: They open up potential new opportunities for the market if end users embrace them. That last caveat is a big if.
In some respects, the definition of an AGV has not changed in years, argues Mark Longacre, marketing manager for JBT Corp. and chair of the automatic guided vehicle product section at the Material Handling Industry of America (See 60 seconds with Mark Longacre, p. 58). “We define an AGV as a computer-controlled mobile robot used to move materials around a facility,” Longacre says. “The way they look and what they can do has changed, but there’s nothing in that definition that didn’t apply 10 years ago.”
In fact, Longacre contends that even the interest of lift truck manufacturers in the AGV space is a blast from the past: In the late 1990s, FMC Technologies, JBT’s predecessor, teamed up with Hyster to develop the HyBot, an automated walkie pallet truck.
Longacre may have a point. Conventional AGV providers like Murata Machinery USA and Savant Automation are busier than ever: “There are still plenty of pallets around, and we’re seeing plenty of demand for conventional fork-style AGVs that interface with our automated storage and retrieval systems (AS/RS),” says Tom Meyers, national sales manager for Murata’s logistics and automotive division.
“There are a lot of great new developments out there from other companies,” adds Garry Koff, president of Savant Automation. “But in my world, most end users can’t justify them. They can justify an AGV that is user friendly, non-intimidating and easy to maintain.”
Still, these new developments are hard to ignore. It is a story told through the product introductions at the materials handling shows, going back to 2005.
ProMat 2005: Automatic guided carts
At the 2005 ProMat, Jervis B. Webb introduced a new type of vehicle to the broad market: the automatic guided cart or AGC. Webb had been toying with the design since 2002, according to Brian Stewart, president and co-CEO of the Daifuku Webb Holding Co., which now owns Webb. An AGC was basically an AGV stripped down to its core: A simple, light-duty platform designed to follow magnetic tape and deliver relatively light loads of around 1,200 pounds from point A to point B. Where an AGV used a roller bed or forks to carry a load, a cart was designed to move a frame that held the product it was moving.
Carts didn’t make much of a splash at the show. Conventional AGV makers dismissed them as a novelty. But Webb believed there was a market. “We believed we had come up with a low-cost solution that reduced customers’ costs for getting into AGVs,” says Stewart.
Webb initially promoted them to the auto industry as an alternative to tuggers to deliver parts to the line. Over time, AGCs have evolved into flexible, moving production lines. “With the right kind of frame, the cart can move an assembly from one workstation to another without bolting conveyor to the floor,” says Stewart. “If your production needs change, it’s very easy to move the tape and create a new layout for the line.”
Today, carts are a significant reason for the rise in the number of AGV units being produced every year. “A smart cart is now in the $15,000 range,” says Stewart. “And, with production volumes rising, we’re getting to the point where we will be able to go into mass production mode, like a lift truck, and bring the price down to a point where you can’t ignore them in distribution environments.” That includes carts that can move loads of up to 5,000 pounds, Stewart adds. “Our goal is to have a world-class mass production line within the next seven to 10 years,” he says.
NA 2006: Automatic truck loading
Webb was back with another innovation in 2006. Set up at its booth was a mini-warehouse, including a pallet pick up station, pallet rack for putaway and picking, and an enclosed space the width of a trailer with a dock plate. During the demonstration, the AGV automatically picked up a palletized load from the staging area and then loaded it into the pallet rack or onto the back of the trailer.
Two years of research and development with Anheuser-Busch led up to that moment. “There were conveyorized systems for automatically loading trailers, but the conveyor was bolted down and you needed to own your own fleet of customized trailers,” Stewart says. “Anheuser-Busch challenged us to come up with a vehicle that could replace fixed hard automation. We thought we could do it, and they had some creative people who worked with us.”
Webb was not alone. At that same time, Egemin and Transbotics were also touting automatic trailer loading technology, or ATL as it’s now known, and JBT had vehicles in development.
Five years later, ATLs are still a niche vehicle, but customers are adopting them. JBT, for instance, has installed ATLs at three plants for one major soft drink bottler with plans to roll out five more plants.
What’s more, the capabilities have evolved beyond simply loading pallets one at a time. Egemin, for instance, can also unload trailers, work with pallets or slipsheets, and adapt to multiple sized pallets and loads on the same truck. In addition, one of Egemin’s customers is using an ATL to load pallets 20 deep in a pushback rack system. “That’s a direct result of ATL technology,” says Mark Stevens, vice president of business development for Egemin.
But what automatic truck loading has really done is expand the business case for AGVs.
“Truck loading is an enabler,” Stevens says. “Not the end game.”
ProMat 2007: Mobile robots
In 2007, RMT Robotics, Kiva Systems and Seegrid introduced mobile robots to the industry. They were to AGVs what go karts are to Formula 1 race cars: small vehicles designed to move small loads. But what really distinguished them is that they had unique guidance systems that didn’t require fixed paths, such as magnetic tape on the floor or reflectors and lasers, to find their way around the facility. Instead, they could learn to find their way to almost any spot in a facility.
Like ATLs before them, they were the buzz of the show, even if no one quite knew what to do with them.
Initially, at least, all three vendors resisted the term AGV, although each makes a vehicle that fits Longacre’s definition. Part of the reason is that they didn’t want to be identified with the baggage that went along with early AGV systems. “Back in the 1970s, AGVs were touted as a technology that would revolutionize the way materials handling was done,” says Bill Torrens, director of sales and marketing for RMT Robotics. “Many of those early vehicles never lived up to the hype and some early adopters had negative experiences.”
While each has taken a different path to the market, all three used their small size and navigation capabilities to their advantage. Kiva, for instance, doesn’t think of itself as a vehicle company at all, says Mitch Rosenberg, vice president of marketing and product management. Instead, “We are a warehouse control software company,” he says. “We’ve created a software platform for goods-to-person picking that happens to have these devices that are part of a broader order fulfillment solution.”
RMT, like Kiva, saw an opportunity for a low-cost, flexible vehicle that could do more than move a heavy pallet from point A to point B. “We saw the benefit of AGVs in promoting the lean direction of manufacturing,” says Torrens. “We developed a vehicle with a navigation system that lets the vehicle go anywhere it needs to go based on what it sees in real time. That lets us deliver what’s needed at the line, when it’s needed and in the quantity that’s needed in an expedited fashion.”
And while Seegrid began by carving a niche for itself by enabling case-picking solutions, the company is now licensing its vision-based navigation system to lift truck manufacturers, including Raymond and Linde, which will use the technology to transform lift trucks into automatic guided vehicles.
As an executive from Seegrid explained, “Supply chain professionals want the ability to integrate unmanned distribution activities with their warehouse management system (WMS). A vision-based guidance system gives you the flexibility to easily send the robot wherever you want it to go so that it can be interwoven with the WMS just like a lift truck operator. That’s where you add value.”
ProMat 2009: New players
Think Toyota Material Handling USA and you probably think world’s largest lift truck manufacturer. Think SI Systems, and you probably think manufacturing systems, including tow line vehicles.
But if you attended ProMat 2009, you saw something different at both companies’ booths: automatic guided carts.
The technology was not new. However, the entrance of two new players not previously identified with AGVs or carts said something about how the market was evolving. And while different catalysts sparked the interest of these two companies in automatic vehicles, at the end of the day, both companies entered the field because the needs of their customers were evolving.
SI Systems, for instance, realized that in some assembly applications, a fleet of AGCs was more economical than a towline assembly system. “When you have a vehicle-intense system, few decision points and a lot of work in process, a tow line system makes a lot of sense,” says executive account manager Craig Sleep. “But in smaller assembly systems, we were losing business to carts.” What’s more, they began to see other companies installing carts for line-side delivery in plants where SI Systems was installing a towline. “We had never gotten into line-side delivery before, but we saw an opportunity to offer a more complete solution.” There were even opportunities to combine the two technologies, for instance, using a cart to pick up a fixture at the end of the towline and deliver it to a kitting area.
Toyota, meanwhile, had exhibited its first AGV at ProMat in 2007. The Toyota Tug-Cart Mouse AGV was already being used throughout Toyota manufacturing plants to take subassemblies from one part of the plant to the main assembly line. By 2009, Toyota had expanded the product line to include the L-Cart, a system that allows an end user to use a variety of components to create a cart that fits its needs, almost like an erector kit. Toyota devoted more floor space and offered AGV demonstrations at its booth in 2009, sending a message that it was as serious about AGVs as it is about lift trucks.
In Toyota’s view, AGVs are a complement to its lift truck business, not competition. “We do not believe it’s enough to just be a lift truck salesperson,” says Martin Boyd, vice president of marketing and product planning. “We want to help you apply the Toyota Production System philosophy to your plant and see where you might benefit from automation. AGVs allow us to get our foot in the door to start that conversation.”
In 2009, Toyota also began working with AutoGuide Systems, which developed a plug-and-play kit that converts a Toyota Class III tugger vehicle into an AGV. At the end of the lease, the kit can be removed and installed on the next leased tugger. “We now have plans in motion to apply that technology to more models in our product line,” says Boyd.
“To say that we’re optimistic about this is an understatement,” Boyd adds. “We see big things on the horizon for lift trucks and AGVs.”
ProMat 2011: Turning lift trucks into AGVs
Toyota may have started the conversation about turning lift trucks into AGVs, but the discussion continues.
That was made clear at ProMat 2011, where the talk of the show was the new vehicles introduced by Dematic and Egemin. Both vehicles are aimed squarely at the distribution center.
Built in conjunction with Crown, Dematic took a solutions-based approach to case picking similar to what Kiva is doing with piece picking. The solution combines a pallet truck with voice recognition technology and order fulfillment software to automate the case-picking process: A voice-directed order selector picks cases to a pallet on the pallet truck; once the pallet is full, the pallet truck is automatically directed to the next step in the process, which could be another pick zone or a drop-off location in the shipping area.
Egemin, meanwhile, teamed up with MCFA to create a hybrid pallet-handling AGV. Turn the key one direction and it can be operated like a traditional lift truck. Turn the key in the other direction, and it operates as a fully automated, conventional AGV with trailer loading and unloading capabilities.
While they were designed for different purposes, the two vehicles share a common vision: The AGV OEMs are providing the navigation technology and automation software while the lift truck OEMs are bringing to bear the quality, reliability and economies of scale that come from mass production along with a nationwide dealer network that can service the mechanical systems of the lift truck.
“Flexibility is a selling point,” says Egemin’s Stevens. “But the value is the lower total cost of ownership that comes from a mass produced lift truck, using off-the-shelf parts that can be serviced by a local network of dealers.
Dematic sees this as an entrée into the distribution market. “We are all trying to move AGVs from manufacturing into distribution,” says Scott Hinke, vice president of product sales. “That’s where we believe there is a good return for our customers.”
While Dematic is beginning with case picking, it has plans to roll out other automated lift trucks as part of its “Automate the Conventional” approach to warehousing. “We can focus on the controls, the smarts and the order fulfillment solutions while the lift truck manufacturer can lower the manufacturing and service cost,” says Hinke. “We think the customer will see this as less of a risk.”
If the market now consists of two classes of vehicles—conventional AGVs as well as carts and mobile robots represented by Seegrid, Kiva and RMT—some in the industry, like Claude Imbleau, chief financial officer for Transbotics, see the potential for a third class of hybrid vehicles. “There will always be a market for specialized vehicles that will be made by AGV manufacturers like Transbotics,” Imbleau says. “However, if we can provide the software and the lift truck manufacturers can deliver the quality that we need, it makes sense to have them make every day vehicles, like a fork vehicle.”
In fact, it seems as if nearly everyone in the AGV and lift truck industry has simultaneously had a similar idea.
Kollmorgen, a provider of navigation and automation software to AGV manufacturers now offers the technology to end users who can have the solution installed on their lift trucks at the factory or retrofit an existing fleet of lift trucks.
INRO, a New Zealand-based startup, is taking a similar approach, with software and technology to automate conventional lift trucks.
In May, Raymond signed a sales agreement with Seegrid to develop an automated lift truck powered by Seegrid’s navigation software in North America. At CeMat, Linde was promoting similar vehicles for Europe.
JBT’s Longacre is right when he points out that the two industries did this dance 10 years ago to no avail. At the same time, a number of computer manufacturers, including Microsoft, tried to introduce tablets a decade ago without success. Today, thanks to a confluence of events, including the iPad, tablets are the hottest piece of technology on the market.
Whether this is the AGV market’s iPad moment and these new vehicles will be embraced by the market is yet to be seen. But it’s clear that the evolution of the AGV market will not stop any time soon.
Companies interviewed for this article
Crown
Daifuku Webb Holding Co.
Dematic, http://www.dematic.com
Egemin Automation, http://www.egeminautomation.com/en
JBT Corporation, http://www.jbtc-agv.com
Kiva Systems, http://www.kivasystems.com
Kollmorgen, http://www.pick-n-go.com
Mitsubishi Caterpillar Forklift America, http://www.mcfa.com
Murata Machinery USA, http://www.muratec-usa.com
RMT Robotics, http://www.adamrobot.com
The Raymond Corp., http://www.raymondcorp.com
Savant Automation, http://www.agvsystems.com
Seegrid, http://www.seegrid.com
SI Systems, http://www.sihs.com
Toyota Material Handling USA, http://www.toyotaforklift.com
Transbotics, http://www.transbotics.com
About the Author

Follow Robotics 24/7 on Linkedin
Article topics
Email Sign Up
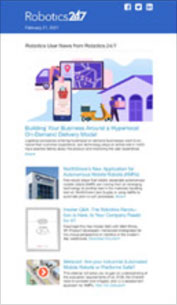