Inventory control at the warehouse level is simple, right? You just need to follow warehouse management system processes, set some minimum SKU levels, and be diligent about scan verifications to track consumption. While that worked 20 years ago, in today’s world, with automated systems to store inventory, you may need a warehouse execution system or WES.
Forget global supply chain snarls for a moment, and consider another changing reality for inventory management—the increasingly complex flow of goods and transactions in fulfillment centers. While warehouse management systems (WMS) have long been responsible for inventory control in distribution centers (DCs), this complexity and the need for visibility is a far cry from manual DCs, where one forward picking zone often served the whole operation.
Today, fulfillment centers might have multiple zones, with subsystems like automated storage and retrieval systems (ASRS) or goods-to-person (GTP) robots. This automation may have software that manages some aspects of inventory, along with storage and bin location functions.
Getting these subsystems to interoperate smoothly with WMSes is no small feat when it comes to real-time inventory allocation as part of order release, as well as timely replenishment of SKUs needing by multiple picking systems.
From WMS to WES
Metering the flow of goods around order release is part of the value proposition for WES software, which sits between the automation and the WMS. A number of vendors, including some WMS providers, offer warehouse execution systems.
“In today’s distribution, it’s all about product flow,” said Dan Gilmore, chief marketing officer at software provider Softeon. “And certainly, there is a segment of the market where DCs are growing larger and more complex. In these environments, that means there’s more and more processes and systems that need to be synchronized. And, if you can’t do that well, you wind up with bottlenecks.”
The core inventory management features in WMSes remain relevant, however. The use of bar-code data capture to verify inventory consumption or moves remains WMS table stakes. So are functions like cycle counting and tracking minimum SKU levels as part of managing replenishment of forward pick locations.
But when it comes to metering the flow of inventory to automation as part of a nimbler approach to order release, things are changing.
Managing inventory flow for automation
A primary use for a warehouse execution system is managing order release to processes and systems on the floor in a way that creates a workflow that makes the most of automation. The WES market has multiple players, including integrators and major warehouse automation vendors.
In most cases, the WMS remains the system of record for most inventory data, but WES functionality is increasingly being deployed for smart order release, including real-time monitoring of inventory levels. The beauty of WES is that it level loads and pulls work through a warehouse, which triggers inventory allocation and replenishment activity, according to Gilmore.
“Clearly, there is some opportunity now with WES capabilities to achieve a much more level-loaded flow of work, and that’s true whether it’s manual processes, automated facilities, or some combination,” he said.
While some automation subsystems track minimum inventory levels and request inventory from a WMS or a WES, some operations may want the WES to actively monitor different zones and determine when replenishment or other inventory moves are needed, Gilmore added.
“The advantage of letting the WES do it is that it can look at the whole flow of work and inventory more holistically—not just what one goods-to-person system is doing, but all the other automated and manual systems—and manage the whole flow of goods,” he said.
WMS software is still the transactional foundation for the warehouse, added Gilmore. He said it is essential for controlling inventory as part of processes like receiving, putaway, crossdocking, or pack out and shipping workflows.
However, a WES shines at the orchestration role as it examines the order pool, looking at resource and inventory availability as it releases work and triggers needed inventory allocation. With the fewest number of SKUs and inventory replenishments, DCs can reach maximum throughput in a given amount of time, said Gilmore.
WES capability also helps by dynamically changing work routing decisions. For example, a WES can sense congestion at a put wall system, and temporarily route work that is normally processed by that put wall though some alternative method, like a cart-pick process. Then when congestion at the put-wall system clears, the WES can start releasing work back to the put-wall system.
“This is very different than what most WMS solutions have done in the past,” Gilmore noted. “More smarts and machine learning come into play. You want to be able to take advantage of all the optimization opportunities.”
Robots require more coordination
With more automation in warehouses, major WMS vendors have been building out their WES capabilities to communicate on a near constant basis with automation systems when it comes to order-release and inventory-disposition decisions, noted Sean Elliott, chief technology officer at Körber Supply Chain, which offers WMS and WES software.
A WMS typically tracks and manages inventory at an aggregate level in the DC, while a WES is aware of the automation status, knows current inventory levels in the automation, and has logic and rules to prioritize what system to assign the work to.
“You do see more inventory disposition decisions being required for optimal execution,” said Elliott. “WMS vendors have taken on more execution capabilities because it’s the only way you can orchestrate that kind of inventory view into the execution plan. That aggregate inventory view is helping determine what to dispatch, when to dispatch, and when to replenish, which becomes a critical component of how a WMS fosters that execution optimization.”
Near-constant communication with automation systems through application programming interfaces (APIs) allow a WMS or WES to know the current inventory in different systems, but it’s up to the WES logic to make the smartest order-release and inventory allocation decisions, Elliot explains.
On paper, one automation system might be more efficient at fulfilling orders in the order pool, but if that system is in the middle of replenishment and is short on inventory needed to complete the work, a different system may end up being faster, explained Elliott.
“To make the most optimal decisions, you can’t effectively do that without one system that actually understands the whole truth,” he said.
Division of duties
Some automated systems are configured to let a WMS, a WES, or another host system control its inventory, while others have their own inventory software which in some instances triggers inventory replenishment requests.
Even when a host system manages replenishment for a fleet of goods-to-person robots or an ASRS, it’s typically the automation software that performs fleet management or controls bin positions.
This leaves the WES or WMS to do the broader orchestration, explained Chris Bratten, manager of logistics consulting at Bastian Solutions. Bastian is a warehouse integrator and solutions provider whose Exacta software offers WMS and WES capabilities.
Bratten said it’s usually best to have one higher-level system that can manage inventory and order release. However, it ideally involves granular, two-way communication, with the robots having purview over movements and bin manipulation, reporting inventory consumption as it happens.
“The host-level system is coordinating all the work that needs to happen, and giving the machine parameters about when that work should happen, so the system can be prepared to move efficiently. The host system typically gives it some flexibility in how it completes its tasks,” Bratten said.
Not all GTP systems or system deployments are implemented in the same way, but generally, a WMS, WES, or some other host system oversees inventory levels and replenishment, he said.
“It really can run the gambit from the [goods-to-person] system being completely dependent on the host system [for inventory management], to some version of them working together and sort of holding hands through the process,” said Bratten.
APIs aid integration
With some older WMS or host systems, the architecture is such that continuous, API-based inventory reconciliations may be hard to achieve, but newer, Web-based APIs from major WMS providers make integration between automated storage and host systems highly effective, said Douglas Card, director of systems and integrator sales at ASRS provider Kardex Remstar.
“It’s gotten much better over the years because of the more open platforms that accept what are known as “REST APIs” which are like a common dialogue for disparate systems to talk to each other easily,” he said.
A WMS or a WES can function as the overall inventory management system, while Kardex Remstar’s software manages detailed inventory data, said Card.
In many deployments, the host system views an ASRS like “virtual location or bin,” he said. The host wants to know how much inventory is in the bin, but it may not care exactly where it’s stored in the moment.
Monitoring minimum inventory levels can be handled by Kardex Remstar’s software to trigger replenishment, but more typically, the WMS tracks minimum SKU levels and handles the replenishment process.
Card adds that while effective two-way integration with WMS is not difficult to achieve today, organizations that want to use automated storage systems should have processes to capture accurate data on item weights and dimensions.
“If you have good dimensional and weight data, it allows you to maximize the cube utilization potential of the [ASRS],” said Card.
Smarter coordination possible
Ultimately, WMS remains the key system for inventory management in most DCs. But as more DCs become fulfillment centers with automated zones to hold inventory, WES-level visibility into that inventory and associated rules around dynamic order release, routing, and related inventory allocation become more important.
Not all WMS solutions are created equal, with some having more WES capabilities, along with more traditional inventory control functionality. At the end of the day, it’s a more complicated world at the warehouse level, and that complexity involves inventory.
“Automated warehouses require more orchestration and inventory transactions, and this is where WES comes in,” said Laura Bickle, senior offering manager of WES at Honeywell. “WES is smarter in coordinating with each subsystem and decision point. It makes decisions in real-time, allowing for intervention and optimization throughout the fulfillment process.”
“WES enables last-minute decisions that would increase order-fulfillment efficiency in the warehouse,” she added. “Honeywell’s WMS and WES have been tightly integrated to play to the strengths of both systems, with WMS used to plan the order fulfillment and WES executing it, while adjusting to various inventory exceptions that happen in a warehouse every day.”
Warehouse execution systems won't necessarily manage all inventory details at the automation level, but they can function like a near-real-time intermediary when it comes to inventory, said Bickle. A WES can constantly exchange data with mobile robots or automated storage and communicate with supply chain systems that management replenishment.
Integration enables scalability
“Industry focus recently has been on integrating the various systems together,” she said. “This opens up real-time communication of data to reduce the unknowns. It provides enough information so customers can efficiently fill orders without having WES control the inventory in every zone of the facility.
“WES ‘talks’ to various automation systems to interchange information needed to intelligently orchestrate order fulfillment and provide a high-level inventory snapshot to WMS so it can communicate with the upstream systems,” Bickle continued.
“This level of integration ensures the systems are in sync, irrespective of who manages the inventory,” she said. “Having a fully integrated WMS and WES enables as much or as little automation and allows for scalability as the warehouse grows.”
About the Author
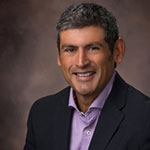
Follow Robotics 24/7 on Linkedin
Article topics
Email Sign Up
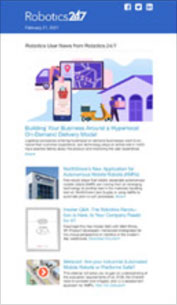
