In distribution centers and warehouses, the use of autonomous industrial trucks and manual high-bay forklifts are both common.
However, the automation of these processes helps to make it safer and more accurate for the operator. With driver-assisted forklifts, the driver may not easily be able to judge where the forks enter into the pallet pockets, which makes the risk high for damage to the forks, pallets, bay, or the products.
Automated Guided Vehicles (AGVs) often are used to collect dollies, but there may be challenges with approaching and positioning accurately under the dolly. The process could be slow or prone to error, especially if relying on work instructions, marks on the floor, or point-by-point navigation.
To help with these challenges, SICK’s Visionary-T 3D streaming camera and new SensorApps can help.
What is the Visionary-T?
The Visionary-T takes a snapshot of the surrounding space. Each shot provides data on distance, intensity, and confidence values, which allows it to properly detect obstacles. AGVs and automatic mobile robots (AMRs) equipped with the Visionary-T will be able to slow down, navigate around, or even stop before colliding with the obstacle, thus saving thousands in potential damage or lost efficiency.
The Visionary-T is a 3D vision sensor that offers maximum flexibility for indoor use due to its innovative 3D-snapshot technology. It provides real-time depth information for each pixel, based on the time-of-flight measurement.
This applies to stationary applications as well. The sensors transmit both raw and pre-processed data, which can then be used for a number of applications. Common uses include collision warning and navigation, object detection, and palletizing and depalletizing.
In addition, users may transfer measured values that have already been evaluated for simpler sensor responses. With this method, the right information is always transmitted and customized to suit the respective application.
SICK has developed two SensorApps to enhance the Visionary-T: Dolly Positioning and Pallet Pocket Detection. Because maneuvering packages in warehouses requires a high degree of precision, these SensorApps were developed to allow for the smooth automated flexibility of mobile robots. Human workers also receive significant help from these solutions, thus allowing for a safer and more efficient process.
Dolly Positioning SensorApp
When it comes to automation, success lies in precision. The automated pick-up of dollies with an AGV requires exact identification of the place and position of the dolly. The Dolly Positioning SensorApp helps satisfy this requirement within a working range of 1.5-3m.
It works by positioning the camera in front of the dolly chassis The Visionary-T captures a 3D image and it pre-processes and evaluates the coordinates of the space under the dolly, before outputting that information to the vehicle controller. The SensorApp can provide automated fine positioning determination for a wide range of different dollies, but that’s not its only benefit.
Some benefits of Dolly Positioning SensorApp include:
- Increases the efficiency of AGV in logistics
- Short process times for dolly pick-up
- Low maintenance effort due to stable app hardware combination
- Easy integration on automated guided vehicle systems
- Automated and reliable position determination for nearly any dolly
Because the Dolly Positioning SensorApp is based on SICK AppSpace, it is also possible to load application-specific Key Apps to the sensor using SICK AppManager. This level of customization may be useful in many facilities.
Pallet Pocket Detection SensorApp
The Pallet Pocket Detection SensorApp satisfies a different need: precise detection of storage spaces and pallets. This is especially important at great heights, as is common in the storage and removal of loads using industrial trucks in an Automated Storage and Retrieval System (ASRS).
Much like with the Dolly Positioning SensorApp, the Pallet Pocket Detection SensorApp uses pre-processed measured values from the Visionary-T that is required to detect the pockets in the pallet in order to accurately pick up the pallet from. It then transmits that data to the control of the automated or manned forklift truck. This helps to cut out any delays associated with lining up both automated and manual forklifts to load pallets in high-bay warehouses.
The Pallet Pocket Detection SensorApp has a working range of 1.5-3 meters, as well as under 800ms of processing time for the detection of coordinates. This makes it the perfect application for industrial vehicles, intralogistics, automotive industry, and more.
More benefits of the Pallet Pocket Detection SensorApp include:
- Increases efficiency of AGVs in logistics
- Low maintenance effort due to stable app hardware combination
- Easy integration on AGVs
Because the Pallet Pocket Detection SensorApp is based on SICK AppSpace, it is also possible to load application-specific Key Apps to the sensor using SICK AppManager. This level of customization comes in useful in many warehouses.
Related White Papers
Autonomous Mobile Robots: The Essential Guide to Safety and Productivity
From production to delivery, automation is happening in all industries. Industry trends show that the use of autonomous mobile robots show no sign of slowing down. Download Now!
Maximum Safety Coverage For Your Small Mobile Robots
For small mobile robot applications, the nanoScan3 provides a competitive advantage for the manufacturing and logistics industries. Download Now!
Article topics
Email Sign Up
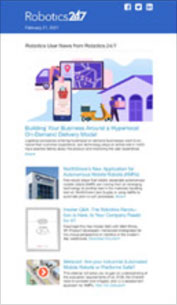
