Plus One Robotics, a provider of AI machine vision software and solutions for robotic parcel handling, recently announced the launch of InductOne - a dual-arm automated parcel induction solution designed to optimize parcel singulation and induction in high-volume fulfillment and distribution centers.
The company shared more details about its new technology during its launch event at Automate 2024. The trade show is being held May 6-9 at the McCormick Place Convention Center in Chicago, Illinois. Attendance is free.
A3 said this year’s show is the biggest yet, featuring more than 365,000 square feet of exhibit space, over 800 exhibitors, and an expected 30,000 registrants, with learning and networking opportunities. Attendees will be able to see the latest in robotics, machine vision, AI, and motion control.
Plus One Robotics said it has leveraged its industry knowledge and track record of over one billion picks to engineer InductOne as a solution for the parcel shipping industry. The company’s learnings from handling over a million picks per day and the required reliability for such high-volume operations have been manifested in this new dual-arm machine.
Induction robot engineered for efficiency and flexibility
A key characteristic of InductOne is its dual-arm design, which Plus One said outperforms single-arm solutions. While a single-arm system typically tops out at around 1,600 picks per hour, the coordinated motion of InductOne’s two arms can achieve sustained pick rates of 2,200 to 2,300 per hour. InductOne’s peak rate maxes out at a rate of 3,300 picks per hour.
“Parcel variability is a significant challenge of automation within the warehouse,” said Erik Nieves, CEO of Plus One Robotics. “That’s why InductOne is equipped with our innovative individual cup control gripper, which can precisely handle a wide range of parcel sizes and shapes. But it’s not just about what InductOne picks, it’s also about what it doesn’t pick. The system avoids picking non-conveyable items, allowing them to automatically convey to a designated exception path and preventing the robots from wasting precious cycles handling items which should not be inducted.”
The Plus One Robotics engineering team put a strong focus on the physical design of the InductOne system, engineering the machine to have the smallest possible footprint and lowest weight, all while maximizing its capabilities. The company said these features enable the system to integrate into brownfield facilities, while minimizing the need for site modifications.
“The engineering approach behind InductOne has been focused on efficiency and flexibility,” Nieves said. “We designed the system to be as compact and lightweight as possible, making it easier to deploy in limited spaces, including on existing mezzanines. The modular and configurable nature of InductOne also allows it to seamlessly integrate into a variety of fulfillment center layouts.”
Want to learn more about robots picking, packing and packaging? This article was featured in the October 2024 Robotics 24/7 Special Focus Issue titled “Robots picking and packing with precision.”
Article topics
Email Sign Up
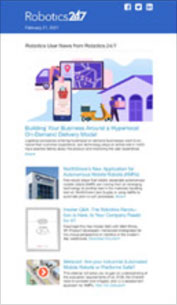