Dunn-Edwards is a leading manufacturer and supplier of paints and supplies serving professionals and consumers throughout the southwest, and sells most of its paint through its own 109 store network.
In 2010, Dunn-Edwards consolidated all manufacturing and distribution operations into a new, fully automated facility in Phoenix, Ariz. An integral part of the automation portfolio is a high-performing robotic palletizing system that handles 5-gallon buckets of paint. In designing the system, the requirement was to palletize the buckets, 36 buckets to each pallet, at a rate up to 48 buckets per minute, building two pallets every 90 seconds.
While the equation seems daunting, throughput numbers are met using the new palletizing system that includes a single articulated arm robot (ABB, abb.com/robotics) and a vacuum gripper that can pick up four of the 55-pound buckets at a time.
Because the system is able to achieve such high speeds, Dunn-Edwards is able to serve two incoming conveyors and build two pallets at a time. The robot sits between the two conveyors and picks buckets from the left conveyor and puts them on a left pallet or from the right conveyor for placement on the right. And, if needed, the buckets from line A can be placed on pallet B, or from B to A.
While the vacuum gripper is strong enough to pick up the buckets, it’s sensitive enough not to remove the tint plugs that are attached to the top of each pail.
But the biggest consideration was the cycle time, says Clay Fenstermaker, director of engineering at Dunn-Edwards. “We first considered an overheard gantry robot system, but [our supplier] came up with a simulation that showed that the fixed-position robot could deliver the rate we needed.”
About the Author

Follow Robotics 24/7 on Linkedin
About the Author

Follow Robotics 24/7 on Linkedin
Article topics
Email Sign Up
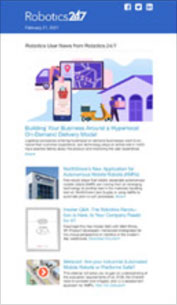