Apptronik Inc. today unveiled Apollo, which it claimed is “the world's most capable humanoid robot.” The Austin, Texas-based company said the robot is designed for friendly interaction, mass production, performance, and safety.
“As labor challenges and employment trends continue to impact our economy, we need to fundamentally change the way we think about work, particularly in the warehouse and the supply chain,” said Jeff Cardenas, co-founder and CEO of Apptronik, in a release.
“People don’t want to do robotic, physically demanding work in tough conditions, and they shouldn’t have to,” he added. “Humanoid robots are not just an answer to this challenge, they are a necessity – and because of our deep robotics lineage, Apollo is uniquely positioned to quite literally step in and make an impact.”
In 2016, Apptronik spun out of the Human Centered Robotics Lab at the University of Texas at Austin. The company's stated goal is “to introduce the next generation of robots that will change the way people live and work, while tackling some of our world's largest challenges.”
“Decades of research and development have gone into Apollo, coming out of the DARPA Robotics Challenge,” Cardenas told Robotics 24/7. “We've always believed that versatile, multipurpose robots were the future, but the technology wasn't there yet in 2016.”
Modular machine the result of many lessons
Apptronik added that Apollo is built on research with 10 previous “general-purpose” robots, including work on NASA Valkyrie.
“Since the early days of Apptronik, we've been looking for performance,” recalled Cardenas. “We wanted electric actuators to do what hydraulics could do, and we wanted robustness and low cost.”
Cardenas said his team learned about safety from its development of exoskeletons, about improving payload while maintaining affordability from work on robot arms, dynamic walking from bipedal models, and fine manipulation from upper-body systems.
As a result, Apollo has a modular design, allowing users to decide whether it is best suited for a particular application as a full humanoid, a torso on wheels, or a stationary mounted robot.
In addition, Apptronik has put most real-time processing onboard Apollo, with some fleet management and instructions in the cloud, according to Cardenas. “A lot of that is thinking about low compute and making algorithms more efficient to run onboard,” he said.
Safety a consideration for collaboration
At 5 ft., 8 in. tall, Apollo weighs 160 lb. and is able to lift 55 lb., said Apptronik. It includes a force-control architecture similar to that of collaborative robots for safe operations around people, in contrast to traditional industrial robots. But how safe are humanoids?
“There are some places where humanoids might be safer, while other pose more challenges,” acknowledged Cardenas. “They have far less inertia and footprint than a pallet-moving robot, but they can fall over.”
“Safety standards for AMRs [autonomous mobile robots] and mobile manipulation are well-worn paths that the industry is used to,” he asserted. “Instead of thinking from scratch, we can build on that. There will eventually have to be standards unique to humanoids as they evolve, such as those proposed by ASTM International's committee on legged robots.”
“For mobile manipulation, the ability to reach high and the ground and to take up roughly a square foot is an advantage,” Cardenas added. “Instead of relying on a heavy base like an AMR, a humanoid can just widen its stance.”
Apollo also includes perception-based behaviors to slow or stop if someone enters a perimeter or impact zone, respectively, he said.
Apptronik worked with argodesign to ensure that Argo's design balanced complexity and approachability. Digital panels on the robot's face and chest are intended to facilitate communication, approximating a face-to-face exchange with co-workers for human-machine interaction, said the company.
Apollo designed for ease of manufacturing
Apptronik also noted that Apollo's performance per cost and energy efficiency are the results of a decade of iteration, including 35 different models of electric actuation systems.
“Our unique actuators use one-third less components than traditional actuators and hit 50% higher speeds,” said Cardenas. “Drive trains have become more accessible, and the sensors we're using are more affordable.”
The humanoid robot uses swappable batteries, each of which has a four-hour runtime, to be able to work for a full shift without needing downtime to be plugged in.
The company said it has optimized supply chain resilience for production at scale by eliminating single-sourced components and by locating itself in the Texas-Mexico manufacturing corridor.
“Our operations team took a look at critical components and made sure we didn't select any with a single source,” Cardenas said. “Our target was to have dozens for each. It's easy to say, but hard to do, and it was our benchmark.”
“To grow from hundreds to millions, Mexico has the talent and a third the labor cost of China,” he said. “It takes 2.5 hours to get from Monterey to Texas, compared with 18 days from China to the U.S. by sea.”
From logistics to wider use cases
While Apollo is designed to be “general purpose” and to conduct a wide range of tasks, Apptronik has not designed it to be accurate to 0.2 mm and is not waiting for it to scale to millions of units before it can be affordable, said Cardenas.
“We're initially focused on the most viable applications in the near term—gross manipulation for case handling,” he explained. “We'll be short by 675,000 logistics jobs in the U.S. by 2025, and many of these are just picking up stuff and moving it.”
“A lot of businesses can't adopt specialized automation for high volume and throughput,” Cardenas added. “3PLs [third-party logistics providers] often have shorter-term contracts and need flexibility. We're starting with picking from a conveyor to a pallet, pallet to conveyor, and lineside delivery.”
“Robotics solutions are in high demand in the logistics sector as companies grapple with a shortage of labor and volatile demand,” said Ash Sharma, managing firector at Interact Analysis.
“Billions of dollars are being invested in implementing robots to help pick, move and sort goods through warehouses across the world,” he said. “Humanoid robotic solutions are the next step in the evolution of the industry as customers look for more flexible automation that can be used across multiple workflows.”
Apptronik sets sights on terrestrial and space applications
Apptronik said it eventually sees Apollo being used in construction, oil and gas, electronics production, retail, home delivery, elder care, and many other industries. It is continuing to support NASA in reducing human exposure in hazardous environments and preparing to extend humanity's presence in space through teleoperated and autonomous systems.
Apptronik is building a customer center to demonstrate real-world use cases, and it is working on a beta version of Apollo for field pilots next year, said Cardenas. The robot is a platform for further development, he noted.
“Apollo is the 'iPhone' of robots, enabling development partners to expand on Apptronik-developed solutions and extend the digital world into the physical world to work alongside people and do the jobs that they don’t want to do,” the company said.
“Industrial robots are like mainframes—more generalizable, but rigid and infrastructure-heavy,” Cardenas told Robotics 24/7. “The value proposition of a humanoid robot is as a breakout general-purpose platform that could be extended with software. This is a personal computer moment for robotics.”
About the Author
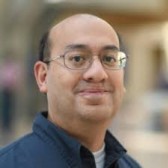
Follow Robotics 24/7 on Linkedin
Article topics
Email Sign Up
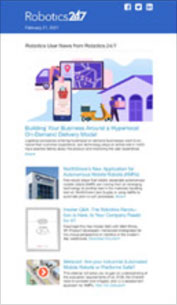