Acme Manufacturing has released its latest offering for aerospace maintenance, repair, and overhaul or MRO operations. Its said its Robotic Auto Path Generation technology is designed to streamline airfoil polishing and jet engine blade repair.
Due to unique part-to-part variations, the repair of aerospace engine components requires meticulous attention to detail, noted Acme. The Auburn Hills, Mich.-based company said its new automated system uses calculated algorithms to rapidly generate part paths, saving time and optimizing finishing operations.
“At Acme Manufacturing, we have harnessed the power of automated measurement and 3D surface scanning to cater specifically to the aerospace MRO industry's unique challenges,” stated Dany DeChamplain, managing director of Acme Singapore.
“Our Robotic Auto Path Generation technology empowers aerospace MROs with an unparalleled tool that enhances precision, reduces downtime, and increases overall operational efficiency,” he asserted. “A recently installed system proved successful. After I provided training to the customer, they were able to introduce 40 unique part models to the production system easily.”
Automating aerospace blade repair
Acme Manufacturing said Robotic Auto Path Generation can simplify the robotic programming process and is suitable for high-mix and low-volume manufacturing. The company added that its system is three to four times faster than traditional CNC grinding or manual finishing.
Acme outlined the following features:
Swift robot path generation: The company said its advanced 3D surface scanning technology is based on a “golden part” to facilitate the automatic generation of a part-specific robot path, reducing manual intervention and programming time. Once a new part is introduced to the system, programs are saved for quick changeover, Acme said.
Precision enhancement: The software-based technology can create precise part paths that produce a consistent surface finish for material removal. Combined with advanced automated inspection, Acme said its new system can eliminate part-to-part variations and enable repair facilities to meet strict tolerances in the aerospace MRO industry.
Seamless integration: The company said its human-machine interface (HMI) provides a user-friendly way for quick and easy system integration, with an intuitive process for operators.
Consistency and quality: There is limited access to original CAD data in the high-mix, low-volume aerospace MRO industry, said Acme. In-service components that have been subject to wear may not match original specifications. The system uses a golden part as a reference to measure each part and generate robot paths to produce accurate specifications.
Increased productivity: Acme said aerospace MRO manufacturers can increase productivity with Robotic Auto Path Generation. In addition, robotic material-removal systems can improve safety and lower unit costs, it said.
About Acme Manufacturing
Since 1910, Acme Manufacturing said it has brought material removal innovations to more than 20 industries globally. The family-owned company has produced over 3,900 robotic systems and a full line of coated abrasive belt centerless grinding systems, suitable for O.D. (outside diameter) precision grinding of bar and tube materials.
For more information about Acme Manufacturing's aerospace MRO technology, visit https://www.acmemfg.com/maintenance-repair-overhaul-robotic-metal-finishing/.
Article topics
Email Sign Up
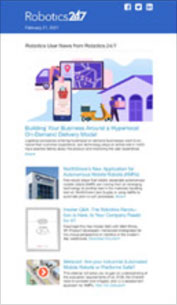
