Additive manufacturing companies have been active during the worldwide pandemic and shutdown, helping health care providers and other companies address supply chain shortages. Digital Engineering spoke to Jonah Myerberg, co-founder and CTO at Desktop Metal, about the company’s activities and experiences during the COVID-19 shutdown.
DE: Desktop Metal has been involved in rapidly developing and producing a new COVID-19 nasal test swab. Can you tell me about that project?
Jonah Myerberg: Although swabs are not made of metal, this was an initiative we identified right away where we could help. This wasn’t something we could print out metal or even print in-house, but it was a problem that could be solved with 3D printing.
We set out to figure out how 3D printing could help, and how we could make that real. This really shows the ability that 3D printing has to help respond quickly, flexibly and in mass quantities to these types of production problems.
To make a swab, what we've learned is it's not easy to tool up if you are set up to make 100,000 swabs a day. If you want to make a million a day, it will take a while. That’s not the case with 3D printing. You can flip a switch and ramp up to making a million swabs very quickly.
In their current design, swabs are not 3D printable. They are a complex assembly of nylon fibers and small features and bristles that are on this flexible stick that you use once and throw away. At first glance you say, this can’t be 3D printed, but if you look at the function, it can. And this is what we face every day in 3D printing; we look at the problem the part is solving, then design for 3D printing. That is what we did here. Went back to the drawing board. These swabs need to collect samples from the back of the nasal cavity. They don't have to be these materials. If we were to 3D print them, how do we collect samples? We made lattice structures at the end that would grab samples and deliver them to the test kits.
You can now distribute this new design around the entire country to every 3D printer available and start massively manufacturing them via distributed manufacturing.
[You can learn more at printedswabs.org.]
DE: In the past, 3D printing has often been described as a solution looking for a problem. The current supply chain challenges in the health care space seem like a problem that was custom-made for 3D printing.
Myerberg: It’s really just one of many perfect scenarios for 3D printing. That’s the Catch-22 of 3D printing. If you develop a tool that is applicable to so many different things, it is viewed as not being applicable to anything.
DE: How do you think this experience will change the way companies view 3D printing’s role in the supply chain?
Myerberg: The companies that were most affected by this outage or interruption will be the first to start to think about how to reduce that risk in the future. That’s what these large companies do. That’s what these supply chain organizations within companies are tasked with. If they mis-predicted these interruptions, then they will be looking at this on their list of potential things that can reduce risk.
In large-scale manufacturing, they refuse to have a single source for any item because of the risk. If you have the best battery in the world that is different than any other, you are going to have a hard time selling that into an automotive company, for example, because you don’t have a competitor with an equivalent battery. Single-sourcing is too much of a risk. If you can create the ability to manufacture that component in-house as well as source it from outside, then you lower risk for them.
DE: You also helped enable a local hospital in Boston to convert some snorkel masks into PPE, correct?
Myerberg: Snorkel mask conversion was a national phenomenon. Doctors were looking around for PPE [personal protective equipment] that could be converted, and some doctors say that in Italy there were providers who converted snorkels into masks for use in the office. They wanted to know if they could do that also. They had filters they could use with the oxygen generators in their offices. If they could combine them with the masks they could have useful, reusable PPE.
They reached out to me, and the next day I had a prototype. We were able to print these converters they could attach to the filters and to the masks. Based on measurements we did for the masks and from talking to the doctors, we were able to put together an adapter that would allow the snorkel mask to become a filter, and to feed oxygen into masks to allow doctors to wear them for long periods of time. It’s just another example of how quickly you can respond if you have the right tools.
DE: What has the remote work transition been like internally for Desktop Metal?
Myerberg: What a tornado that was! Yes. With the tools that we use today in our office, you can work remotely at the drop of a hat. Everyone was able to go home, quarantine themselves and still tap into the resources they need to get their jobs done.
We have a skeleton crew in-house to support essential workers. We were able to set up an array of cameras so we can remotely watch what is going on. It’s amazing what you can accomplish. This isn’t unique to Desktop Metal. The world is going to be changed when we emerge from this. There will be more remote work than there was before.
DE: How are you handling remote customer support?
Myerberg: Our customer service team has many levels of support. On-site visits are not possible right now. We have to do remote support exclusively over the phone or over video conference. So far it’s been well received.
DE: What lessons do you think you’ll take out of this experience?
Myerberg: The question every company needs to ask is, how do they help themselves, help employees and customers, as well how do they help society in situations like this? How do you stay essential? How do you stay flexible? Do you have the tools in-house to change and adapt to the unknown?
Look at all of the work that is going on across the country on ventilator projects. It's so amazing to me that hospitals had to put out requests that they were running out of ventilators, and all of a sudden there were 50 ventilator projects born. How does that happen? From people working in their garage to big companies like Tesla, they are coming up with designs, but everyone is utilizing 3D printing. That is how you move fast.
We have a number of sister companies who have stopped what they were doing and are now designing ventilators. It’s as if they could do anything in their building. It’s been an amazing response.
How do you remain digital when you are producing a physical product? 3D printing allows you to stay as close to the digital environment as possible. You can bridge from digital to physical quickly, without an investment in tooling.
A lot of amazing things have happened so far, and there are still a lot of really cool things that will be exposed in the future. I think a lot of those will have to do with vaccine deployment. That’s another great example of a long-lead item that 3D printing can potentially help accelerate.
This isn’t over. There will be a new normal out there.
About the Author
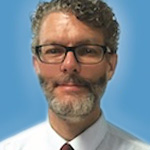
Follow Robotics 24/7 on Linkedin
Article topics
Email Sign Up
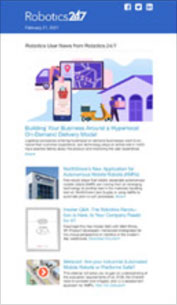