Projects that leverage additive manufacturing and 3D printing to create really big objects have gotten a lot of attention. Massive robotic printing systems have been developed to create everything from cars to entire buildings.
Those big 3D printers are impressive, but printing very small objects is actually a lot harder. Getting high resolution at smaller scales is difficult, and there are limits to just how detailed you can get once you move into nanoscale territory.
Researchers at MIT appear to have found a way around this problem by printing small objects and then shrinking them to even tinier sizes after the fact.
3D Print with Nanoscale Precision
Using a technique called implosion fabrication, researcher Ed Boyden and his team have been able to print complex shapes and structures at very tiny sizes.
“It’s a way of putting nearly any kind of material into a 3-D pattern with nanoscale precision,” said Boyden, the Y. Eva Tan Professor in Neurotechnology and an associate professor of biological engineering and of brain and cognitive sciences at MIT.
MIT had previously created the technique (known as expansion microscopy) to do exactly the reverse – it was used to magnify details in brain tissue by embedding the tissue in a different material and then expanding it.
Running this process backward enabled them to make small structures even smaller. MIT used scaffolds made of polyacrylate and then built centimeter-sized objects inside. The scaffolds are bathed in a solution that contains fluorescein molecules, which can attach to the scaffold when exposed to laser light. Those molecules act as anchors that can bind to other types of molecules.
“You attach the anchors where you want with light, and later you can attach whatever you want to the anchors,” Boyden said. “It could be a quantum dot, it could be a piece of DNA, it could be a gold nanoparticle.”
“It’s a bit like film photography — a latent image is formed by exposing a sensitive material in a gel to light. Then, you can develop that latent image into a real image by attaching another material, silver, afterwards. In this way implosion fabrication can create all sorts of structures, including gradients, unconnected structures, and multimaterial patterns,” said graduate student Daniel Oran.
Applying acid to the structures shrank them to one-thousandth of the original size or volume without distortion. Among the objects they printed were hollow linked cubes and an etching of a fictional character that knows a thing or two about shrinking – Alice in Wonderland.
According to MIT, the process can be used with a variety of materials, including metals, quantum dots and DNA.
The technique could be used in optics, medicine, robotics and other applications, the researchers say. It also uses commonly available laboratory equipment.
According to this article in New Scientist, Boyden thinks that even tinier objects can be created noting that in tests the researchers were able to expand and shrink structures by as much as 8,000 times.
The research was published in the December 13 issue of Science.
Source: MIT
About the Author
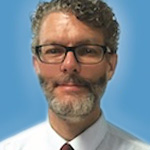
Follow Robotics 24/7 on Linkedin
Article topics
Email Sign Up
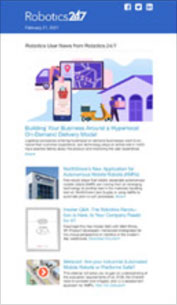
