We’ve all heard the buzzwords: Robotics, artificial intelligence, predictive and prescriptive analytics, blockchain and digital transformation. In fact, every day, we read about a new technology that is going to revolutionize the way business gets done and supply chains get managed.
Based on the press accounts, it’s easy to think that every competitor in a given industry is already putting next-generation technologies to work while your organization is running in last place. But the truth is, most organizations are still in the investigation, and maybe pilot stage; few have actually deployed those technologies and fewer still have done so at scale.
But, a handful of innovators are putting tomorrow’s supply chain technologies to work today. And it is these foresighted few that Supply Chain Management Review, Peerless Media and IDC honored with our first annual NextGen Supply Chain Awards, recognizing the achievements of early adopters and industry leaders. The award winners were announced in Chicago at the NextGen Supply Chain Conference in April.
Read on to see what our award winners are doing. And, if you think your company is leading the way in the adoption of these technologies, we hope you’ll enter a submission for next year’s awards later this summer. You can learn more at nextgensupplychainconference.com.
Robotics: GEODIS
When 3PL GEODIS piloted mobile collaborative robots in its Indianapolis DC, it wanted to double the picking productivity of women’s apparel by its workforce. And that’s exactly what happened. But as Kevin Stock, senior vice president of engineering, explains, the benefits didn’t stop there. The initial 30-robot installation also included:
- working collaboratively with the existing workforce;
- simplifying the job, reducing travel distances, increasing job satisfaction, and
- reducing training times.
The overall success of the 90-day pilot was so impressive that GEODIS plans to roll out a total of 175 robots from Locus Robotics across four locations by mid-2019. Since the launch of the original pilot in October 2017, a total of ten million items have been picked.
Prior to the implementation, order pickers manually picked items to 50-pound pick carts that they pushed around a 139,000 square foot area of the 300,000 square foot facility. Radio frequency units directed their tasks—definitely an “old school” approach. However, innovation is a corporate objective at GEODIS and the concept of using collaborative robots fit that bill.
According to Stock, due diligence, partner selection and contracting began at ProMat in April 2017 and was completed by July. Prep work for the changeover began in August. “There was some minimal infrastructure needed in the DC to integrate an electric run for robot charging stations and some drops for robot induction areas,” says Stock. “Otherwise the physical setup of our operation didn’t change.” The teams had to determine the format and number of plastic totes each robot would carry. IT work focused on integrating GEODIS’s WMS with the robot management system and creating a digital warehouse map that the robots would follow.
Add in training time and change management sessions with the 60 team members who would be involved with the robots, and the prep work took roughly two months before the October 2017 go live with 30 robots. “We emphasized that the robots were not there to replace associates, but to improve their productivity,” Stock recalls. That effort paid off and the associates have embraced working with robots.
Today, instead of pushing heavy carts through the picking area, robots come to the associates. Each associate wears a Bluetooth badge that communicates with the robot. A green light on the robot indicates it is waiting for an individual to perform a pick. A blue light comes on when the robot is moving to its next location. A pink light indicates it is stuck in a pick and requires attention. It’s that simple.
If he had to do it again, Stock says he’d pick a time other than a month before peak to introduce a new technology. Nonetheless, GEODIS not only survived those challenges, it continues to expand its use of collaborative robots.
Artificial Intelligence: DHL
When it comes to NextGen technologies like artificial intelligence, DHL Supply Chain follows a simple rule: Improve operations by developing specialized tools that supplement people. “We’re trying to develop new tools that allow people to make better decisions and improve accuracy,” explains Justin Ha, director of solutions design at DHL Supply Chain, the company’s contract logistics division. “At the same time, we’re using AI to teach machines how to improve their efficiencies by eliminating touches and relieving people of tedious tasks.”
DHL has already scored gains using AI in three key areas.
In one DHL operation, people used to evaluate incoming shipments to determine if extra handling is required. It was a high-speed manual process with on-the-fly decision making that was fraught with the potential for error. DHL now uses AI and computer vision to evaluate incoming shipments and determine proper handling for people on the line. Productivity has increased by as much as 14%. The accuracy of detecting critical pallet properties has also increased along with the speed of handling. Just as important, explains Ha, false positives have been drastically reduced. This allows DHL to process the inbound loads quicker in an environment under enormous time pressure, and have better traceability than the old method of capturing 2D and 3D images.
Artificial intelligence is also at work in a big-picture system called Resilience 360, a supply chain risk management platform. Risks can derive from a range of events, such as natural disasters to plant shutdowns. Machine learning identifies alternative solutions capable of keeping the supply chain up and running following a disruption. Ha says the alternative route finder usually takes less than eight seconds to develop post-incident alternative delivery routes.
In a third application, DHL Supply Chain uses smart piece-picking robots with put walls. In this application, a robotic arm, rather than an associate, picks items and places them in the selected cubbie. The robot utilizes machine learning to better identify and grasp a wide variety of items, improving the robot’s handling and grasp success rate over time.
There may even be opportunity for AI to improve warehouse management systems, says Ha. DHL has developed an internal eCommerce Business Intelligent Suite that uses analytical optimization tools to maximize the efficiency of various tasks in the operation and improve overall warehouse productivity as much as 15%. AI could make additional improvements by adding continuous learning and predictive analytics to the suite.
As to the future, Ha says there is room to do more: “As we become more digitized, we want to be in a position to introduce AI to more processes. Right now, we’re in the early stages but we’ll move rapidly down the road from here.”
Analytics: Johnson Controls
Three years ago, the two most common complaints fielded by the Johnson Controls maintenance team were: “my work area is too cold (or warm)” and “our facilities guy says the chiller just doesn’t look right, but he isn’t sure what’s wrong.” Thanks to advanced analytics, that cycle has changed, explains Vineet Sinha, director of digital solutions business at Johnson Controls, a leading supplier of HVAC systems and building controls. “Our Cloud-based analytics platform now pinpoints what the real problem is rather than focusing on a chiller symptom that requires imprecise troubleshooting and often just as imprecise maintenance,” Sinha says. “Furthermore, we have now connected all key systems in buildings including security, safety and external attributes.”
Known as the Connected Equipment Program (CEP), the system uses data from onboard sensors, equipment specifications and past maintenance records to analyze performance and drive predictive diagnostics. Customers can access the Cloud-based platform any time of day from any location. It can even be accessed by smartphones using a 4G cellular network. Dashboards offer real-time data and analytics to monitor equipment, identify problems and perform specific, required maintenance procedures to fix them.
“The result is increased service responsiveness and reliability as well as reduced emergency outages and energy consumption,” says Sinha. “Condition-based maintenance greatly simplifies the maintenance supply chain by right-sizing maintenance parts and optimizing inventory to actual conditions at a location.”
Among the other benefits being realized by condition-based maintenance is a 65% reduction in the mean time to repair, a significant improvement given that the company manages 5,000 connected chillers in 37 countries. It is also contributing to revenue, with a service contract renewal rate of more than 90% for those companies on CEP. “That’s the best metric of success we have,” he says.
The original program is now undergoing next generation improvements with the help of artificial intelligence and machine learning that learns from past condition monitoring. The goal is high-precision predictions of machine performance and efficiency that pinpoint specific maintenance needs in real time. “We’re enabling this through a proprietary Cloud platform called the Digital Vault. It is helping connect diverse building systems and creates insights for buildings and occupants,” says Sinha.
Blockchain: IBM
There are plenty of ways for the electronic parts supply chain to be compromised. One is the loss of visibility as parts move through the supply chain. This could lead to the replacement of genuine parts with counterfeits. And then there is the problem of disputes during the Customs declaration process. None of these problems are easy to solve. But for IBM, blockchain is proving itself as a NextGen supply chain tool of the future to address these issues.
Today, IBM manages about 18,000 suppliers of parts to clients in more than 170 countries. “Our supply chain is vulnerable to disruptions that may have a significant impact on the execution and delivery of products and services,” explains Tom Ward, AI project leader at IBM. “Having blockchain infused in our supply chains provides timely, secure and trusted information about parts and their movements,” he adds.
Several attributes of blockchain make the technology attractive to IBM. To begin, all parties can access the blockchain ledger. However, each party sees only the parts of the ledger relevant to them. Transactions, which can’t be altered after the fact, are updated in real time across the blockchain. And as Gergely Szlovak, cognitive advocacy lead explains, IBM’s first three pilots proved blockchain works in the supply chain. Just as important, it resulted in measurable gains.
In the first pilot, IBM worked with hard drive supplier Seagate to guard against counterfeits. A total of 60,000 Seagate drives move through the IBM supply chain monthly. The pilot focused on just one part number that accounts for a significant number of drives. Initial savings to both companies is estimated at $2.2 million a year due to blockchain tracking. In addition, blockchain provides a significant mitigation of risk through improved tracking.
The second pilot focused on collecting real time visibility and other asset data about shipments and individual parts in the IBM supply chain. Disputes about parts in transit for IBM’s $8 billion worth of systems annually are not uncommon. Blockchain improved parts traceability significantly.
The third pilot was intended to improve and expedite Customs clearance. Hard benefits included savings to suppliers of $600 per transaction and an additional $1,000 to IBM, resulting in a 40% cost avoidance just in clearing customs. Meanwhile, use of blockchain increased risk avoidance by 70%.
“There are still plenty of questions about how blockchain works in much of the supply chain, says Ignacio Escobedo, supply chain consultant, “but the pilots show that it is clearly a reality and not simply a fad.”
Adds Ward: “With blockchain, you know you can trust the data. And the transparency of transactions for asset management is huge. None of that is possible with any other technology in the supply chain today. We’ve just started to scratch the surface with blockchain.”
Digital transformation: Cisco
Most people think of Cisco as a world-class high-tech company. But four years ago, the company wondered why it couldn’t also be a world-class logistics company. As Cisco’s senior director of global logistics, Jack Allen was tapped to lead the project dubbed Logistics 3.0. “From the beginning, our objective was to enhance the customer experience, not make money on the logistics of moving parts around for our suppliers and customers,” Allen explains.
Not that the whole idea didn’t give him pause. “A digital transformation of logistics is not just a major undertaking. It fundamentally changes how everything works,” Allen says. “And we were taking on every aspect of the movement of goods between facilities throughout the entire Cisco supply chain. There was more than one night when I wondered if we could pull this off.”
Despite those misgivings, Allen and a team of up to 40 volunteers—no one was assigned to the project—did pull it off. Operational improvements include better visibility across the supply chain, as well as lower costs and greater efficiencies. Since the start of the Digital Transformation initiative, end-customer logistics volume at Cisco has grown more than 39%, with more than 1,500 customers and partners worldwide now leveraging the capabilities developed in the Logistics 3.0 program. They can access—at any time—the status of their order, including expected delivery time. Furthermore, Cisco acts as a one-stop logistics supplier for everything from freight insurance to consolidated delivery.
In addition to delivering an Amazon-like customer experience to industrial customers, new found supply chain efficiencies, savings and additional revenue are delivering benefits to Cisco’s bottom line. Better yet, says Allen, those benefits recur year after year.
In retrospect, the program was hardly a slam-dunk. First, top management had to buy into the concept, according to Darren Mallard, senior manager of marketing strategy, who joined the project part way through. “Management did its due diligence and set benchmarks that had to be met along the way. And we exceeded their expectations,” he says
As a result of the program, Cisco now has supply chain innovation centers in Houston, Texas and Istanbul, Turkey, where they test and implement new digital technologies that will drive continued improvements. Today, there is even an internal talent development angle to Logistics 3.0. Cisco takes on interns and Co-Op students from various universities, works with them over a three-year cycle and rotates them through third-party vendors in their supply chain. Globally, 293 students have participated in the program, with additional students joining each quarter/semester. And, 92 of them have gone on to become full-time Cisco employees. “It’s really exciting to see the dreams of a corporation and of people turned into reality,” says Allen. “I would do this all over again if asked. It’s one of the most rewarding things I’ve ever done.”
Article topics
Email Sign Up
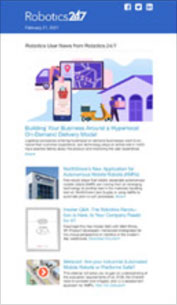
