Industrial communications and IT provider HMS Networks AB recently announced the deployment of an upgraded wireless system at Mercedes-Benz’s Ludwigsfelde, Germany factory.
Upgrades to the facility’s wireless communications system supported expanded automated guided vehicle (AGV) operation. HMS said it provided wireless fleet management products and hands-on deployment support.
Deployment objectives included improving efficiency and complying with EU Machinery Regulation 2023/1230, which becomes mandatory in January 2027. According to the EU, the regulation defines essential health and safety requirements that machinery products must fulfill to be placed on the European market.
“Everything worked as we hoped. The connection is very stable, and we are now able to comply with the safety machinery regulation,” said Maximilian Lichan from Mercedes-Benz. “The support for more bandwidth has even allowed us to manage and configure the AGVs remotely.”
Mercedes sought improved performance, EU regulatory compliance
At the Mercedes-Benz automotive manufacturing facility in Ludwigsfelde, over 70 AGVs move parts to the assembly line. These AGVs transport everything from heavy engines to smaller electronics across distances ranging from 300 to 800 meters, or approximately 1,000 to 2,600 feet.
Each AGV is equipped with an on-board programmable logic controller (PLC) from Siemens or Schneider Electric, which ensures their efficient and safe navigation. Effective AGV navigation relies on good communication between the AGVs and the factory’s control system. This communication enables the factory to track each AGVs' location, load, and real-time status.
Mercedes-Benz’s previous AGV system used Bluetooth technology along with HMS’ Anybus Wireless Bolt and Bridge products. However, they wanted to improve the system’s efficiency and prepare to comply with the EU Machinery Regulation.
“While Bluetooth worked well, we now want to enhance our AGV system to support higher throughput, fast roaming, and lower latency,” Lichen said. “We also need to comply with the soon-to-be mandatory EU safety regulations. Equally important, we want the equipment and experts from the same company, and we want them to come onsite, install the equipment, and verify that everything works.”
HMS systems team on site to install and troubleshoot
Mercedes-Benz provided key information, such as floorplans, to the HMS wireless team. Using this information, HMS said it first conducted a predictive site survey to determine optimal placement and number of access points required. HMS then visited the factory to verify the accuracy of the survey and make any necessary adjustments.
HMS Networks’ wireless team configured Anybus wireless products on each AGV and verified the system functioned as planned. Source: HMS Networks
Mercedes-Benz used the updated predictive site survey to install necessary power outlets and network cabling. Once infrastructure was in place, HMS returned to install and configure the Anybus Wireless products on each AGV before verifying that the installation worked as planned.
“A key factor for us was that HMS were on hand to design and install the wireless infrastructure. That was important for us,” Lichan said. “We wanted to have wireless experts onsite to ensure that everything went smoothly. We’re not wireless experts, HMS are. We make cars, which you probably already knew.”
Anybus access points, Bolt II units operate on 5 GHz band
The wireless infrastructure deployed for Mercedes-Benz uses Anybus access points powered by PoE L2 managed switches, with a Wireless Bolt II mounted on each AGV. The Anybus Wireless Bolts handle communication from the AGVs to the traffic control system by connecting through 12 access points in the factory’s ceiling. As an AGV moves out of range of one access point, it transitions to the next, ensuring uninterrupted communication.
HMS said the project utilized the 5 GHz frequency band, and the Bolt II’s similarity to its predecessor model also simplified the installation.
“We wanted to use the 5GHz frequency band where we have four dedicated channels that didn’t interfere with our existing systems,” Lichan said. “It was also convenient that the Bolt II fits in the same hole as the original Bolt.”
Article topics
Email Sign Up
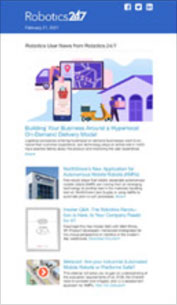
